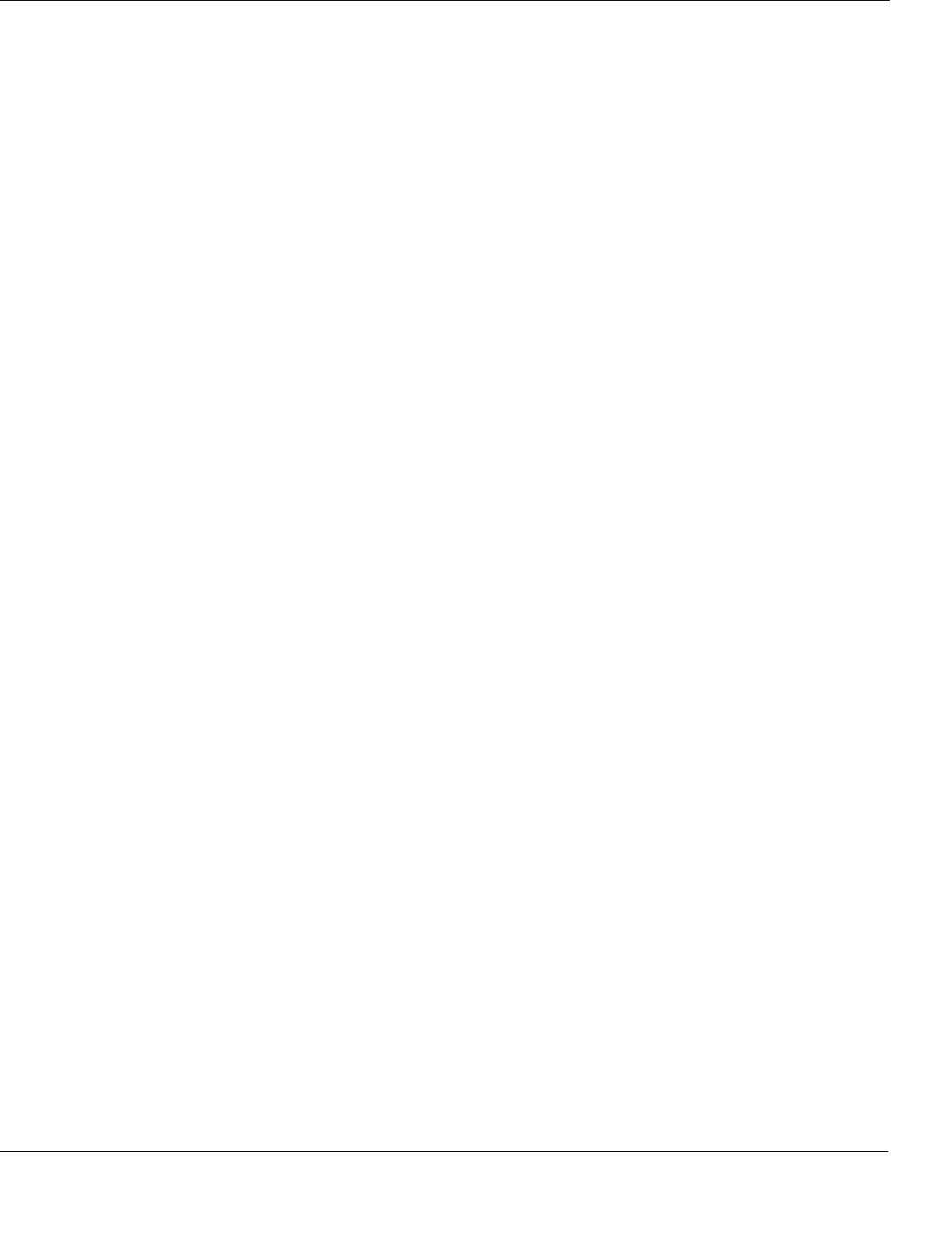
ptg6843605
capacity cushion – capital intensive
The Encyclopedia of Operations Management Page 58
of three and probably has a capacity of at least three. For many years, this author wrote APICS certification
exam questions related to this concept. It was amazing how many people answered this question incorrectly.
The best capacity will minimize the total relevant cost, which is the sum of the capacity and waiting costs.
All systems have a trade-off between capacity utilization and waiting time. These two variables have a non-
linear relationship. As utilization goes to 100%, the waiting time tends to go to infinity. Maximizing utilization
is not the goal of the organization. The goal of capacity management is to minimize the sum of two relevant
costs: the cost of the capacity and the cost of waiting.
For example, the optimal utilization for a fire engine is not 100%, but much closer to 1%. Utilization for an
office copy machine should be relatively low because the cost of people waiting is usually higher than the cost of
the machine waiting. One humorous question to ask students is: “Should you go make copies to keep the
machine utilized?” The answer, of course, is “no” because utilization is not the goal. The goal, therefore, is to
find the optimal balance between the cost of the machine and the cost of people waiting.
In contrast, some expensive machines, such as a bottling system, will run three shifts per day 365 days per
year. The cost of downtime is the lost profit from the system and can be quite expensive.
In a manufacturing context, capacity management is executed at four levels: Resource Requirements
Planning (RRP), Rough Cut Capacity Planning (RCCP), Capacity Requirements Planning (CRP), and
input/output control. See those entries in this encyclopedia to learn more.
The newsvendor model can be used to find the optimal capacity. The model requires that the analyst define
a time horizon, estimate the distribution of demand, and estimate the cost of having one unit of capacity too
much and the cost of having one unit of capacity too little.
In some markets, customers can buy capacity rather than products. For example, a customer might buy the
capacity of a supplier’s factory for one day per week. This can often help the customer reduce the procurement
leadtime. Of course, if the customer does not use the capacity, the supplier will still be paid.
See absorptive capacity, bill of resources, bottleneck, capacity management, Capacity Requirements
Planning (CRP), closed-loop MRP, downtime, input/output control, Little’s Law, load, newsvendor model,
Overall Equipment Effectiveness (OEE), process design, queuing theory, Resource Requirements Planning
(RRP), Rough Cut Capacity Planning (RCCP), safety capacity, utilization, yield management.
capacity cushion – See safety capacity.
capacity management – Planning, building, measuring, and controlling the output rate for a process.
See capacity.
Capacity Requirements Planning (CRP) – The planning process used in conjunction with Materials
Requirements Planning (MRP) to convert open and planned shop orders into a load report in planned shop hours
for each workcenter.
The CRP process is executed after the MRP planning process has produced the materials plan, which
includes the set of all planned and open orders. CRP uses the order start date, order quantity, routing, standard
setup times, and standard run times to estimate the number of shop hours required for each workcenter. It is
possible for CRP to indicate that a capacity problem exists during specific time periods even when Resource
Requirements Planning (RRP) and Rough Cut Capacity Planning (RCCP) have indicated that sufficient
capacity is available. This is because RRP and RCCP are not as detailed as CRP with respect to timing the load.
The output of the CRP process is the capacity plan, which is a schedule showing the planned load (capacity
required) and planned capacity (capacity available) for each workcenter over several days or weeks. This is also
called a load profile.
See Business Requirements Planning (BRP), capacity, closed-loop MRP, input/output control, Master
Production Schedule (MPS), Materials Requirements Planning (MRP), planned order, Resource Requirements
Planning (RRP), Rough Cut Capacity Planning (RCCP), routing, Sales & Operations Planning (S&OP).
capacity utilization – See utilization.
CAPEX – An abbreviation for the CAPital EXpenditure used as the initial investment in new machines, equipment,
and facilities.
See capital.
capital – Money available for investing in assets that produce output.
See CAPEX, capital intensive.