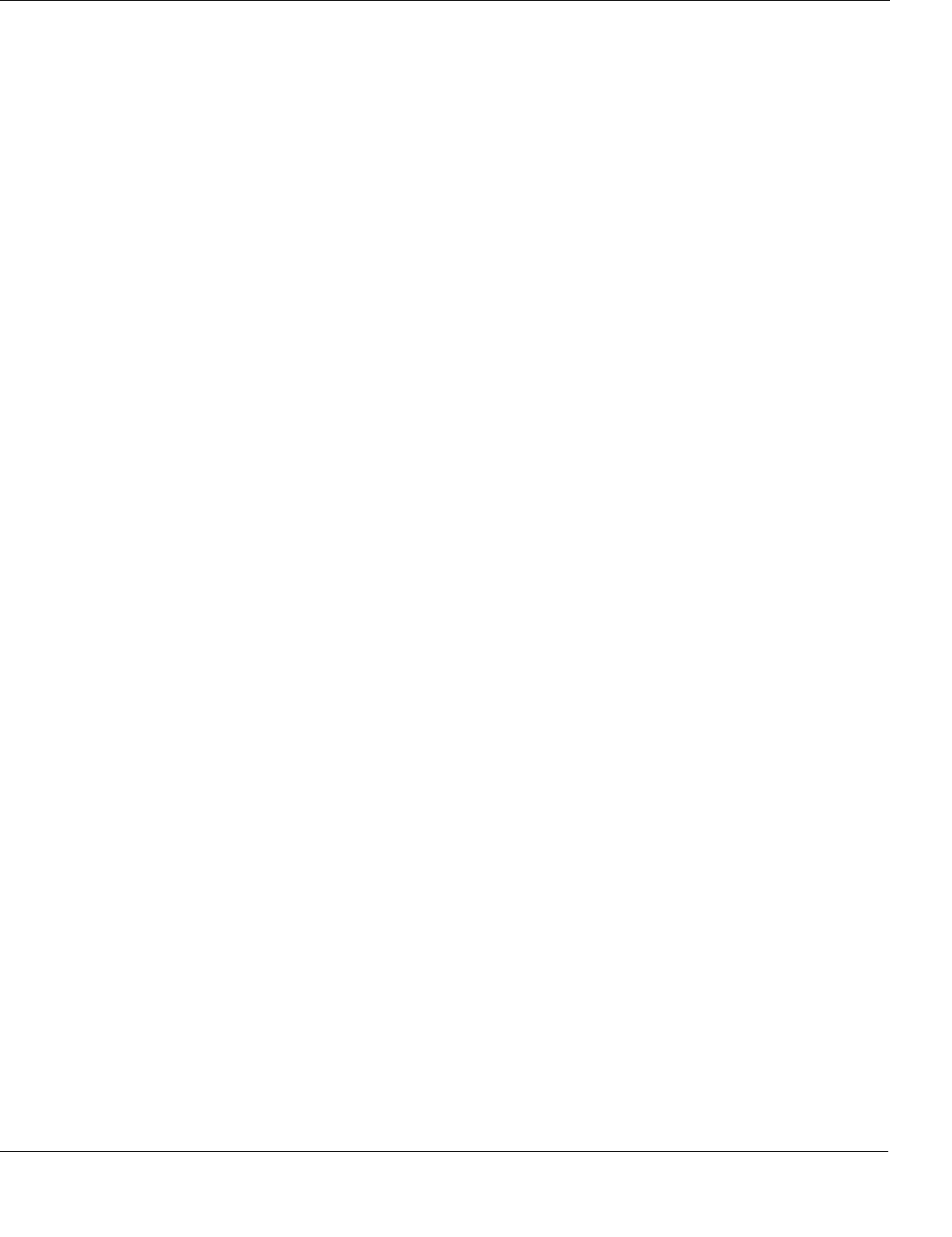
ptg6843605
control limit − co-opetition
Page 83 The Encyclopedia of Operations Management
If all points are within the upper and lower statistical control limits, variation may be ascribed to “common
causes” and the process is said to be “in control.” If points fall outside the limits, it is an indication that “special
causes” of variation are occurring and the process is said to be “out of control.” Eliminating the special causes
first and then reducing common causes can improve quality. Control charts are based on the work of Shewhart
(1939). The most commonly used control charts are the run chart, x-bar chart, r-chart, c-chart, and p-chart. Less
commonly used control charts include the s-chart, s
2
-chart, u-chart, and np-chart.
See c-chart, common cause variation, cumulative sum control chart, lean sigma, np-chart, outlier, p-chart,
process capability and performance, quality management, r-chart, run chart, seven tools of quality, special cause
variation, specification limits, Statistical Process Control (SPC), Statistical Quality Control (SQC), tampering,
u-chart, x-bar chart.
control limit – See Statistical Process Control.
control plan – A formal document that defines how an organization will continue to benefit from an organizational
intervention, such as a lean sigma project.
When a process improvement project has been completed, it is important that the organization “sustain the
gains.” This is often difficult given the normal organizational “entropy,” where the system tends to fall back into
the old state of disorder. A good control plan includes the following elements:
• Procedure – What solutions were implemented to attain the project goals? What control device is in place?
• Responsible party – Who is responsible for this? See the RACI Matrix entry for a methodology.
• Nature of control – How does the control measure sustain the gain? What is the control measure for early
detection?
• What to check – What does the responsible party inspect/observe? What are the failure modes?
• Action/Reaction – What does the responsible party do if the situation is out of control?
If statistical process control is appropriate, the following data items should be specified for each Key Process
Output Variable (KPOV): Target value, lower specification limit, upper specification limit, C
pk
, and the
measurement system used to collect the data.
Good control plans go beyond statistical process control and include clear job descriptions, aligned reward
systems, standard operating procedures, visual signals and instructions, and error proofing.
See ADKAR Model for Change, lean sigma, Lewin/Schein Theory of Change, RACI Matrix.
CONWIP – An approach for manufacturing planning and control that maintains a constant work-in-process
inventory in the system.
With CONWIP (Spearman, Hopp, & Woodruff 1989), every time the last step in the process completes one
unit, the first step in the process is given permission to start one unit. As a result, CONWIP maintains a constant
WIP inventory. This is similar to the Theory of Constraints “drum buffer rope” (DBR) concept, except that
CONWIP does not send a signal from the bottleneck, but rather sends the signal from the final step in the
process. This concept is similar to a JIT pull system, except that CONWIP does not need to have buffers
(kanbans) between each pair of workcenters. Given that CONWIP does not require the firm to identify the
bottleneck and does not need to implement any type of kanban system between workcenters, it is clearly easier to
operate than many other systems. CONWIP can be implemented with a simple visual control system that has the
final operation signal the first operation every time a unit is completed. CONWIP can be applied at almost any
level: at a machine, a workcenter, a plant, or even an entire supply chain. Some research suggests that CONWIP
is superior to both DBR and JIT in terms of system performance (inventory, capacity, etc.).
See blocking, Drum-Buffer-Rope (DBR), gateway workcenter, kanban, pacemaker, POLCA (Paired-cell
Overlapping Loops of Cards with Authorization), pull system, Theory of Constraints (TOC), Work-in-Process
(WIP) inventory.
co-opetition – A blending of the words “cooperation” and “competition” to suggest that competing firms can
sometimes work together for mutual benefit; also called co-competition and coopetition.
Cooperation with suppliers, customers, and firms producing complementary or related products can lead to
expansion of the market and the formation of new business relationships, perhaps even the creation of new forms
of business. An example can be found in group buying, where multiple, normally competitive, buying group
members (such as hospitals) leverage the buying power of the group to gain reduced prices. All members of the
buying group benefit from this relationship.