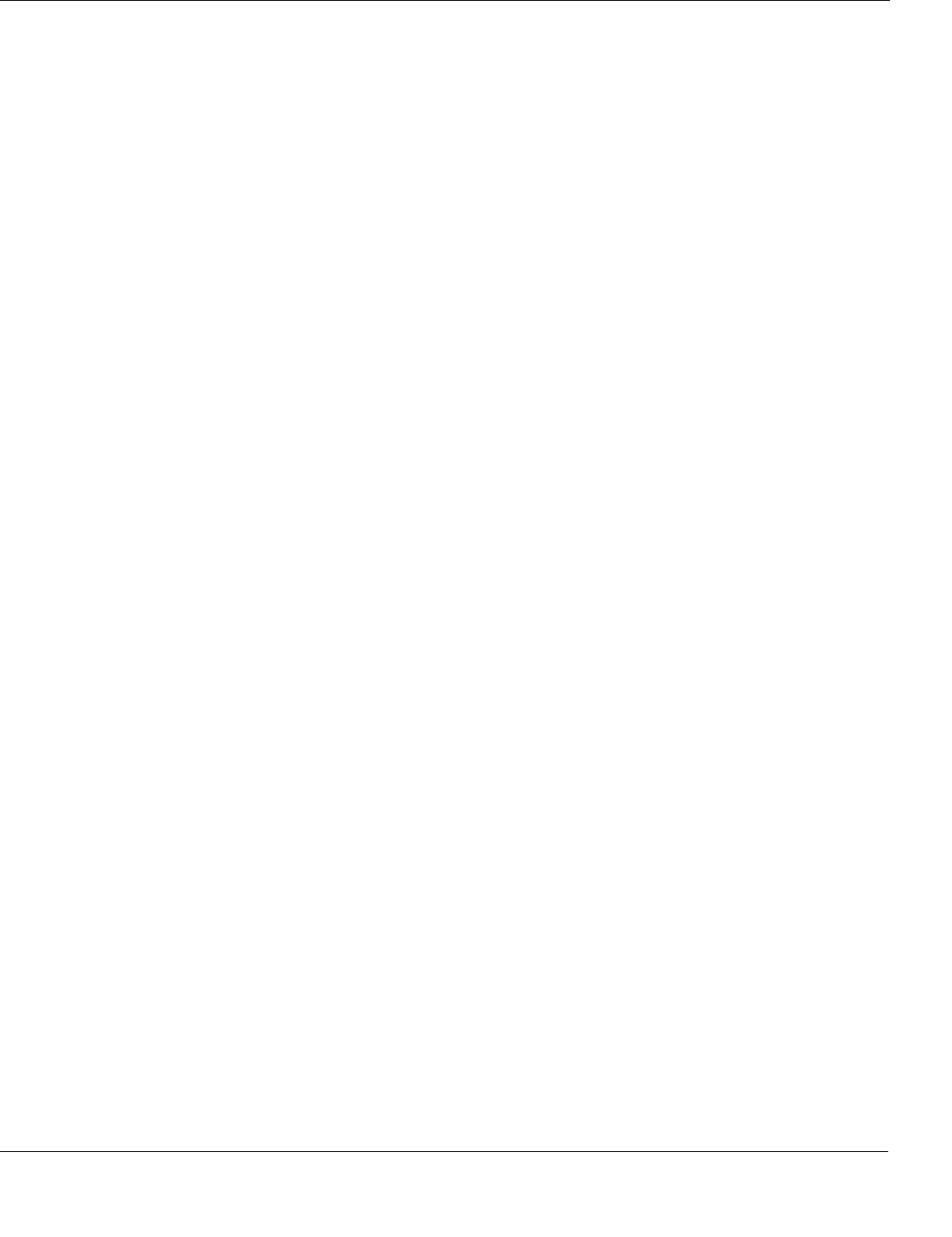
ptg6843605
Automated Identification and Data Capture (AIDC) – autonomous workgroup
The Encyclopedia of Operations Management Page 32
AGVs typically follow a path defined by wires embedded in the floor to transport materials and tools
between workstations. Many firms have found AGVs to be inefficient and unreliable.
See automation, robotics.
Automated Identification and Data Capture (AIDC) – See Automated Data Collection (ADC).
Automated Storage & Retrieval System (AS/RS) – A computer-controlled robotic device used for storing and
retrieving items from storage locations; also called ASRS.
Automated Storage and Retrieval Systems are a combination of equipment, controls, and information
systems that automatically handle, store, and retrieve materials, components, tools, raw material, subassemblies,
or products with great speed and accuracy. Consequently, they are used in many manufacturing and warehousing
applications. An AS/RS includes one or more of the following technologies: horizontal carousels, vertical
carousels, vertical lift modules (VLM), and the traditional crane-in-aisle storage and retrieval systems that use
storage retrieval (SR) cranes.
See automation, batch picking, carousel, warehouse, zone picking.
Automatic Call Distributor (ACD) – A computerized phone system that responds to the caller with a voice
menu and then routes the caller to an appropriate agent; also known as Automated Call Distribution.
ACDs are the core technology in call centers and are used for order entry, direct sales, technical support, and
customer service. All ACDs provide some sort of routing function for calls. Some ACDs use sophisticated
systems that distribute calls equally to agents or identify and prioritize a high-value customer based on the calling
number. Some ACDs recognize the calling number via ANI or Caller ID, consult a database, and then route the
call accordingly. ACDs can also incorporate “skills-based routing” that routes callers along with appropriate data
files to the agent who has the appropriate knowledge and language skills to handle the call. Some ACDs can also
route e-mail, faxes, Web-initiated calls, and callback requests.
The business benefits of an ACD include both customer benefits (less average waiting time and higher
customer satisfaction) and service provider benefits (more efficient service, better use of resources, and less need
for training). However, some customers intensely dislike ACDs because they can be impersonal and confusing.
See automation, call center, customer service.
automation – The practice of developing machines to do work that was formerly done manually.
Automation is often a good approach for reducing variable cost, improving conformance quality of a process,
and manufacturing run time per unit. However, automation requires capital expense, managerial and technical
expertise to install, and technical expertise to maintain. Additionally, automation often reduces the product mix
flexibility (highly automated equipment is usually dedicated to a narrow range of products), decreases volume
flexibility (the firm must have enough volume to justify the capital cost), and increases risk (the automation
becomes worthless when the process or product technology becomes obsolete or when the market demand for
products requiring the automation declines).
Automation is best used in situations where the work is dangerous, dirty, or dull (“the 3Ds”). For example,
welding is dangerous, cleaning a long underground sewer line is dirty, and inserting transistors on a printed
circuit board is dull. All three of these tasks can and should be automated when possible. Repetitive (dull) work
often results in poor quality work, so automated equipment is more likely to produce defect-free results.
See 3Ds, Automated Guided Vehicle (AGV), Automated Storage & Retrieval System (AS/RS), Automatic Call
Distributor (ACD), cellular manufacturing, Flexible Manufacturing System (FMS), flexibility, islands of
automation, jidoka, labor intensive, multiplication principle, robotics.
autonomation – See error proofing, jidoka, Toyota Production System (TPS).
autonomous maintenance – A Total Productive Maintenance (TPM) principle that has maintenance performed by
machine operators rather than maintenance people.
Maintenance activities include cleaning, lubricating, adjusting, inspecting, and repairing machines.
Advantages of autonomous maintenance include increased “ownership” of the equipment, increased uptime, and
decreased maintenance costs. It can also free up maintenance workers to focus more time on critical activities.
See maintenance, Total Productive Maintenance (TPM).
autonomous team – A group of people who work toward specific goals with very little guidance from a manager
or supervisor; also called an autonomous workgroup.