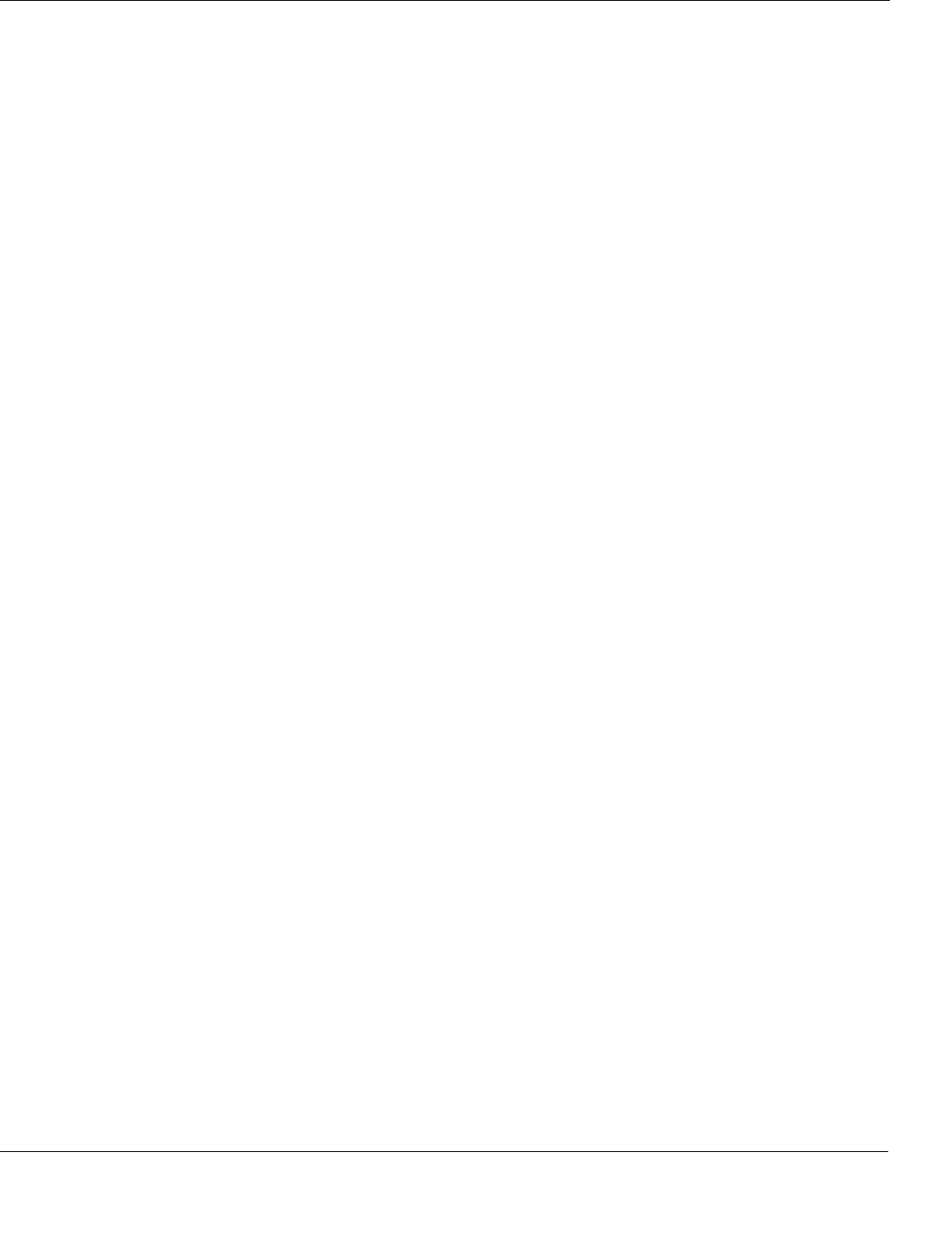
ptg6843605
beta test – bill of material (BOM)
The Encyclopedia of Operations Management Page 42
beta test – An external test of a pre-production product, typically used in the software development context.
A beta test is an evaluation of new software by a user under actual work conditions and is the final test before
release to the public. The purpose of a beta test is to verify that the product functions properly in actual customer
use. The term is often used in the context of software released to a limited population of users for evaluation
before the final release to customers. In contrast, the alpha test is the first test conducted by the developer in test
conditions.
See agile software development, pilot test, prototype.
bias – (1) In a statistics context: The difference between the expected value and the true value of a parameter. (2) In
a forecasting context: An average forecast error different from zero. (3) In an electrical engineering context: A
systematic deviation of a value from a reference value. (4) In a behavioral context: A point of view that prevents
impartial judgment on an issue.
See forecast bias, forecast error metrics.
bid rigging – A form of fraud where a contract is promised to one party even though for the sake of appearance
several other parties also present a bid.
This form of collusion is illegal in most countries. It is a form of price fixing often practiced where contracts
are determined by a request for bids, a common practice for government construction contracts. Bid rigging
almost always results in economic harm to the organization seeking the bids. In the U.S., price fixing, bid
rigging, and other forms of collusion are illegal and subject to criminal prosecution by the Antitrust Division of
the U.S. Department of Justice.
See antitrust laws, bribery, predatory pricing, price fixing.
big box store – A retailer that competes through stores with large footprints, high volumes, and economies of scale.
Examples of big box stores in North America include Home Depot, Walmart, OfficeMax, and Costco.
Carrefour is an example in western Europe. Historically, these big box stores have been built in the suburbs of
large metropolitan areas where land was less expensive.
See category killer, distribution channel, economy of scale.
bill of lading – A transportation/logistics term for a contract between the shipper and the carrier.
The bill of lading (BOL) serves many purposes, such as (1) providing a receipt for the goods delivered to the
carrier for shipment, (2) describing the goods, including the quantity and weight, (3) providing evidence of title,
(4) instructing the carrier on how the goods should be shipped, and (5) providing a receiving document for the
customer; sometimes abbreviated B/L.
See consignee, manifest, packing slip, purchasing, receiving, waybill.
bill of material (BOM) – Information about the assemblies, subassemblies, parts, components, ingredients, and
raw materials needed to make one unit of a product; also called bill of materials, bill, product structure, formula,
formulation, recipe, or ingredients list.
The item master (part master or product master) is a database that provides information for each part (item
number, stock keeping unit, material, or product code). A record in the item master may include the item
description, unit of measure, classification codes (e.g., ABC classification), make or buy code, accounting
method (LIFO or FIFO), leadtime, storage dimensions, on-hand inventory, on-order inventory, and supplier.
The BOM provides the following information for the relationships between items in the item master.
BOM structure – The hierarchical structure for how the product is fabricated or assembled through multiple
levels. In a database, this is a double-linked list that shows the “children” and the “parents” for each item.
Quantity per – The quantity of each component required to make one unit of the parent item.
Yield – Yield information is used to inflate production quantities to account for yield losses.
Effectivity date – This indicates when an item is to be used or removed from a BOM.
A simple multi-level BOM product structure for a toy car is shown below. The final product (Item 1, the car
assembly) is at level 0 of the BOM. Level 1 in this example has the body and the axle subassembly. Note that
plastic is used for both items 2 and 4, but is planned at level 3 rather than at level 2. If plastic were planned at
level 2, it would have to be planned again at level 3 when the gross requirements for item 4 were created. Each
item should be planned at its “low level code.”