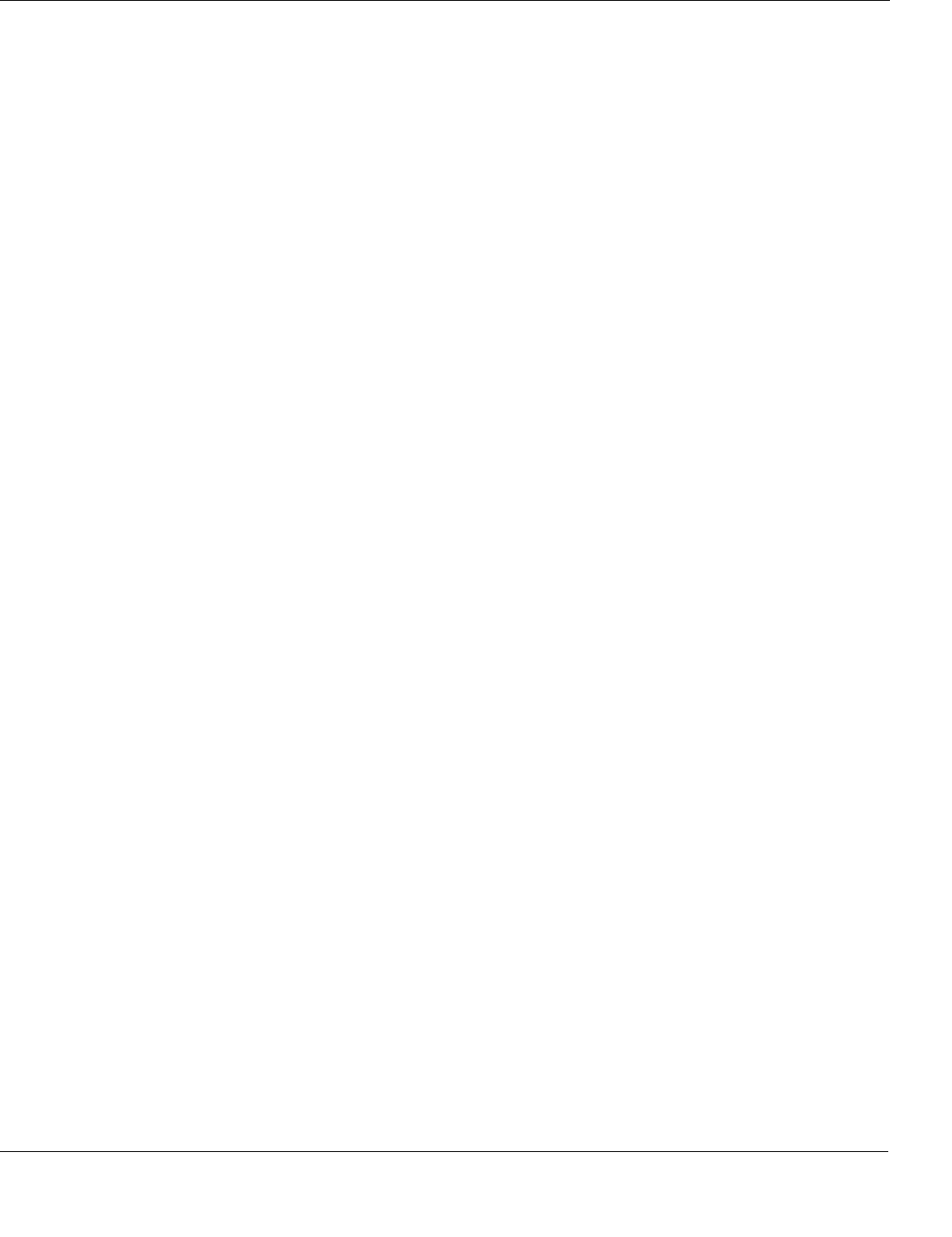
ptg6843605
Acceptable Quality Level (AQL) − acquisition
Page 19 The Encyclopedia of Operations Management
The term “absorptive capacity” was first introduced in an article by Cohen and Levinthal (1990). According
to the ISI Web of Science, this article has been cited more than 1500 times. This entire article can be found at
http://findarticles.com/p/articles/mi_m4035/is_n1_v35/ai_8306388 (May 10, 2010).
Adapted from http://en.wikipedia.org/wiki/Absorptive_capacity and http://economics.about.com/cs/
economics glossary/g/absorptive_cap.htm, May 10, 2010.
See capacity, empowerment, human resources, New Product Development (NPD), organizational design,
outsourcing, workforce agility.
Acceptable Quality Level (AQL) – The maximum percentage defective that can be considered satisfactory as a
process average.
When deciding whether to accept a batch, a sample of n parts is taken from the batch and a decision is made
to accept the batch if the percentage of defects is less than the AQL. The AQL is the highest proportion defective
that is considered acceptable as a long-run average for the process.
For example, if 4% nonconforming product is acceptable to both the producer and consumer (i.e.,
AQL = 4.0), the producer agrees to produce an average of no more than 4% nonconforming product.
See acceptance sampling, consumer’s risk, incoming inspection, Lot Tolerance Percent Defective (LTPD),
producer’s risk, quality management, Statistical Process Control (SPC), Statistical Quality Control (SQC), zero
defects.
acceptance sampling – Methods used to make accept/reject decisions for each lot (batch) based on inspecting a
limited number of units.
With attribute sampling plans, accept/reject decisions are based on a count of the number of units in the
sample that are defective or the number of defects per unit. In contrast, with variable sampling plans,
accept/reject decisions are based on measurements. Plans requiring only a single sample set are known as single
sampling plans; double, multiple, and sequential sampling plans may require additional samples.
For example, an attribute single sampling plan with a sample size n = 50 and an accept number a = 1 requires
that a sample of 50 units be inspected. If the number of defectives in that sample is one or zero, the lot is
accepted. Otherwise, it is rejected. Ideally, when a sampling plan is used, all bad lots will be rejected and all
good lots will be accepted. However, because accept/reject decisions are based on a sample of the lot, the
probability of making an incorrect decision is greater than zero. The behavior of a sampling plan can be
described by its operating characteristic curve, which plots the percentage defective against the corresponding
probabilities of acceptance.
See Acceptable Quality Level (AQL), attribute, consumer’s risk, incoming inspection, inspection, Lot
Tolerance Percent Defective (LTPD), operating characteristic curve, producer’s risk, quality management,
sampling, Statistical Process Control (SPC), Statistical Quality Control (SQC).
Accounts Payable (A/P) – The money owed to suppliers for goods and services purchased on credit; a current
liability; also used as the name of the department that pays suppliers.
Analysts look at the relationship between accounts payable and purchases for indications of sound financial
management. Working capital is controlled by managing accounts payable, accounts receivable, and inventory.
See Accounts Receivable (A/R), invoice, purchase order (PO), purchasing, supplier, terms.
Accounts Receivable (A/R) – The money customers owe an organization for products and services provided on
credit; a current asset on the balance sheet; also used as the name of the department that applies cash received
from customers against open invoices.
A sale is treated as an account receivable after the customer is sent an invoice. Accounts receivable may also
include an allowance for bad debts. Working capital is controlled by managing accounts payable, accounts
receivable, and inventory.
See Accounts Payable (A/P), invoice, purchase order (PO), purchasing, supplier, terms.
acquisition – A contracting term used when an organization takes possession of a product, technology, equipment,
or another organization.
In a mergers and acquisitions context, acquisition refers to one firm buying another firm. In a learning
context, learning is often called acquisition of new knowledge, skills, or behaviors. In a marketing context, the
customer acquisition cost is the cost of finding and winning new customers and is sometimes measured as the