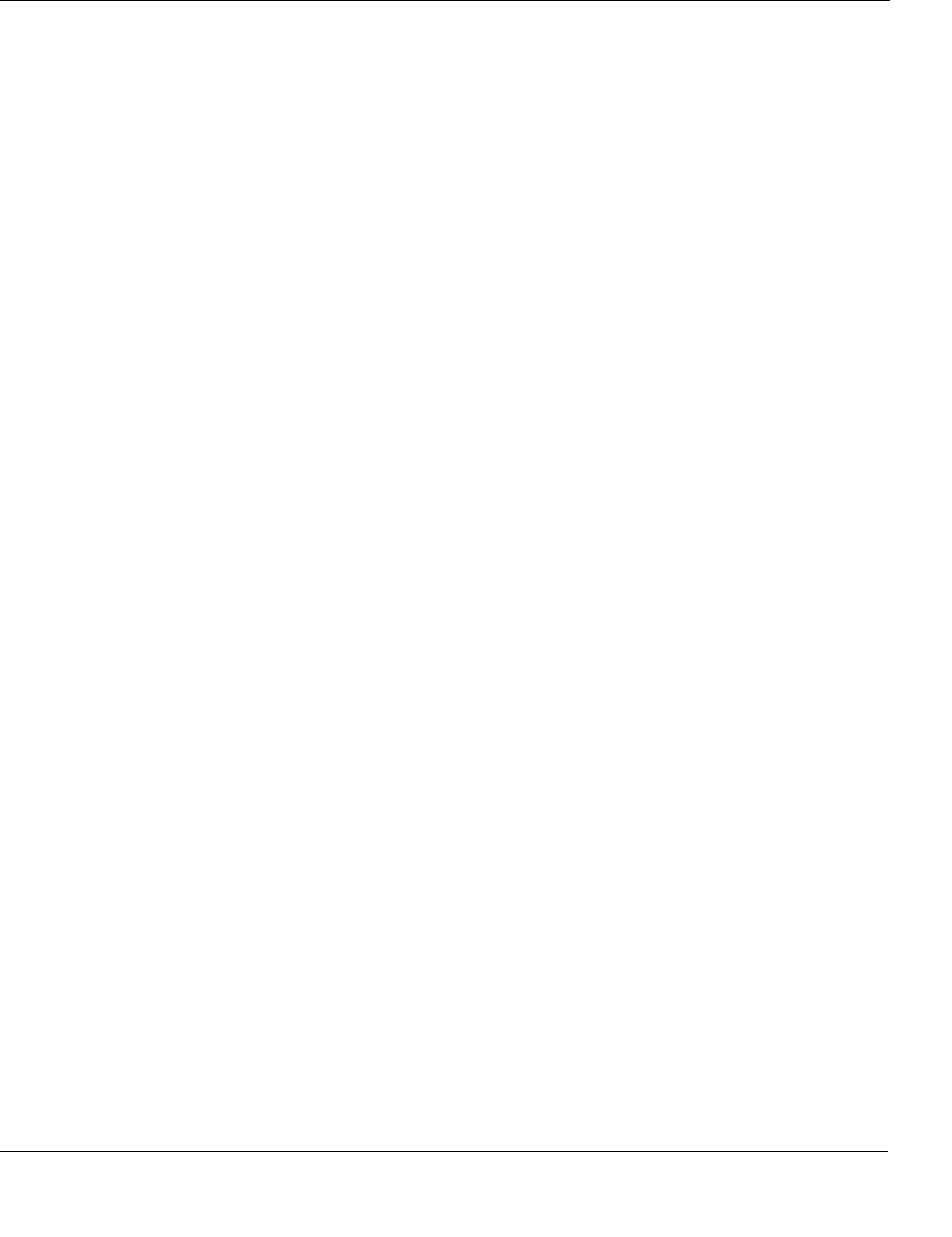
ptg6843605
Warehouse Management System (WMS) – water spider
The Encyclopedia of Operations Management Page 384
See ABC classification, aggregate inventory management, Automated Storage & Retrieval System (AS/RS),
carousel, cross-docking, cube utilization, discrete order picking, distribution center (DC), Distribution
Requirements Planning (DRP), dock, facility location, First-In-First-Out (FIFO), flow rack, forklift truck,
forward pick area, fulfillment, locator system, logistics, materials management, numeric-analytic location model,
pallet, part number, periodic review system, pick face, pick list, picking, pull system, Radio Frequency
Identification (RFID), random storage location, receiving, reserve storage area, safety stock, slotting, square
root law for warehouses, supply chain management, task interleaving, Third Party Logistics (3PL) provider,
voice picking, Warehouse Management System (WMS), wave picking, zone storage location.
Warehouse Management System (WMS) – A software application that helps organizations manage the
operations of a warehouse or distribution center.
WMSs manage the storage and retrieval of materials in a building and handle the transactions associated with
those movements, such as receiving, put away (stocking), cycle counting, picking, consolidating, packing, and
shipping. The WMS guides the operator or machine with information about item locations, quantities, units of
measure and other relevant information to determine where to stock, where to pick, and in what sequence to
perform each operation. Newer warehouse management systems include tools that support more complex tasks,
such as inventory management, product allocations, shipment planning, workforce planning/labor management,
and productivity analysis. WMSs can be stand-alone systems, modules in an ERP system, or modules in a
supply chain execution suite. The benefits of a good WMS include reduced inventory, reduced labor cost,
increased storage capacity, improved customer service, and improved inventory accuracy. Traditionally, WMSs
have used barcodes or smart codes to capture data; however, more recently, Radio Frequency Technology
(RFID) technology has been added to provide real-time information. However, most firms, especially in
manufacturing and distribution, still use barcodes to capture data because of their simplicity, universality, and
low cost.
See ABC classification, Advanced Shipping Notification (ASN), Automated Data Collection (ADC), bill of
material (BOM), cross-docking, distribution center (DC), Distribution Requirements Planning (DRP), dock-to-
stock, fixed storage location, forward pick area, fulfillment, inventory management, locator system, logistics,
materials management, Over/Short/Damaged Report, picking, Radio Frequency Identification (RFID), random
storage location, real-time, receiving, slotting, slotting fee, task interleaving, Transportation Management
System (TMS), voice picking, warehouse, wave picking, zone picking, zone storage location.
warranty – A guarantee given from the seller to the purchaser stating that a product is free from known defects and
that the seller will repair or replace defective parts within a given time limit and under certain conditions.
A warranty and a service guarantee have identical legal obligations for the seller. The difference is that a
warranty is for a product (a tangible good) and a service guarantee is for a service (an intangible product).
Blischke and Murty (1992) and Murty and Blischke (1992) provide a good summary of the warranty literature.
See caveat emptor, product design quality, service guarantee, Service Level Agreement (SLA).
waste – See 8 Wastes.
waste walk – The lean practice of walking through a place where work is being done to look for wasteful activities;
also called a gemba walk.
When conducting a waste walk, it is wise to engage with the gemba, ask the “5 Whys,” take notes as you go,
and follow-up as necessary.
See 3Gs, 8 Wastes, gemba, lean thinking, management by walking around.
water spider – A lean manufacturing practice of assigning a skilled worker to re-supply parts to the point of use on
the production line; a worker who follows a timed material delivery route; also known as mizusumashi (in
Japanese), water strider, water beetle, water-spider, or material delivery route.
The water spider’s job is to follow the schedule and maintain the inventory on a production line between a
minimum and maximum level. They typically use a cart to deliver materials to workstations in predefined
quantities at least every one to two hours on a fixed time schedule. This ensures that the manufacturing line has
the right amount of inventory at the right time. Compared to traditional methods, material delivery routes stock
line bins more frequently and in smaller quantities, resulting in reduced WIP inventory and reduced waiting time.