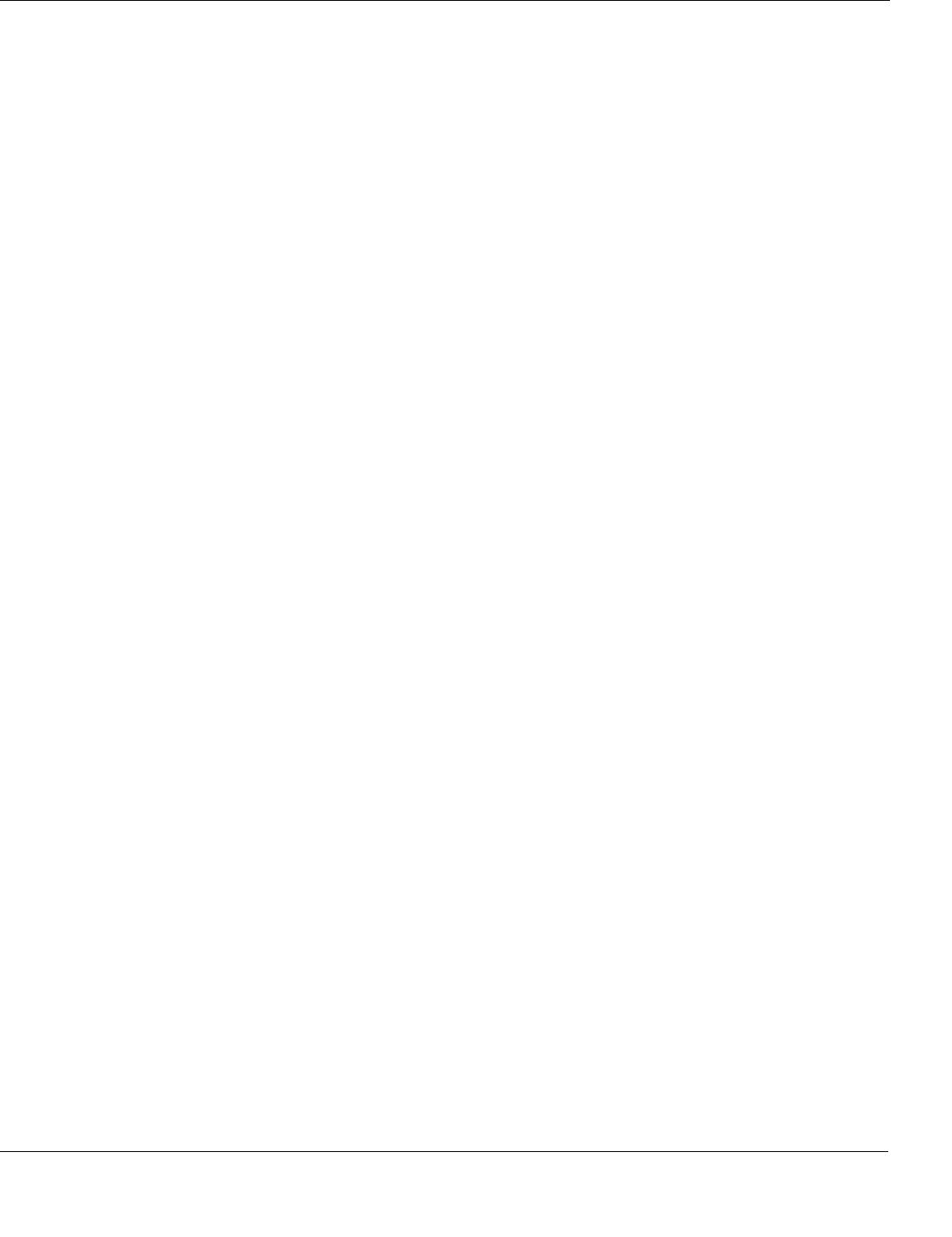
ptg6843605
unnecessary waste – value chain
The Encyclopedia of Operations Management Page 374
See barcode, Electronic Product Code (EPC), part number, Point-of-Sale (POS), Radio Frequency
Identification (RFID).
unnecessary waste – See 8 wastes.
upstream – A manufacturing and supply chain term referring to any process that comes before a given process.
This term makes an analogy between a stream or a river and a manufacturing or supply chain system. Just as
water moves downstream, the product flows “downstream.” A downstream process is any process that comes
after a given process. Therefore, if the painting process comes after the molding process, the painting process is
said to be downstream from the molding. Likewise, an “upstream” process is one that comes before. Therefore,
the molding process is said to be “upstream” from the painting process.
See bullwhip effect, Design Structure Matrix (DSM), Drum-Buffer-Rope (DBR), pacemaker, process map,
reverse logistics.
utilization – The percentage of the available work time that a resource is working.
Utilization is the ratio of the actual time worked for a resource to the time available. Utilization is a
fundamental concept in operations management, capacity management, and queuing theory. It is also one of the
three elements of the Overall Equipment Effectiveness (OEE) metric. In queuing theory, utilization is defined as
the ratio of the average arrival rate to the average service rate. See the queuing theory entry for more detail.
Operations managers sometimes seek to maximize productivity by maximizing utilization to amortize fixed
costs over more units. However, maximizing utilization is often a foolish strategy because high utilization can
also mean high inventory, long customer waiting time, and poor customer service. The ideal utilization,
therefore, will minimize the sum of the waiting and capacity costs. For example, the ideal utilization for a fire
engine is close to zero because the waiting cost is very high. The capacity entry discusses these issues further.
In a factory context, most organizations consider setup time to be part of the work time when calculating
utilization. However, the Theory of Constraints (TOC) literature defines utilization as the ratio of the run time
(excluding setup time) to the time the resource is scheduled to produce.
See bottleneck, capacity, cellular manufacturing, efficiency, operations performance metrics, Overall
Equipment Effectiveness (OEE), productivity, queuing theory, Theory of Constraints (TOC), wait time.
V
validation – See process validation.
validation protocol – See process validation.
value added ratio – The ratio of the processing time (direct value-adding time) to the total cycle time (throughput
time); also called Manufacturing Cycle Effectiveness (MCE), throughput ratio, and cycle time efficiency.
In a manufacturing context, the total cycle time (throughput time) is the total time in the system, which
usually includes the queue time (wait time), run time, post-operation wait time, and move time. The value-
adding time is the “touch time” plus time spent in other value-adding operations, such as baking in an oven,
curing, drying, etc. In labor-intensive manufacturing operations, the value-adding time is just the “touch time.”
In a service context, the value added ratio is often defined as the percentage of the time that the customer is
receiving actual value-added service divided by the time that the customer is in the system. In this author’s
experience, most manufacturing plants have a value added ratio far less than 20%.
See batch-and-queue, cellular manufacturing, cycle time, labor intensive, lean thinking, Overall Equipment
Effectiveness (OEE), queuing theory, time-based competition, touch time, wait time.
Value Added Reseller (VAR) – An organization that adds value to a system and resells it.
For example, a VAR could purchase computer components (e.g., CPU, motherboard, case, and monitor) and
graphics software from a number of different suppliers and package them together as a specialized CAD system.
Although VARs typically only repackage and sell products, they might also include software or services they
have developed themselves. Adapted from www.pcmag.com/ encyclopedia_term, October 25, 2006.
See Original Equipment Manufacturer (OEM).
value analysis – See value engineering.