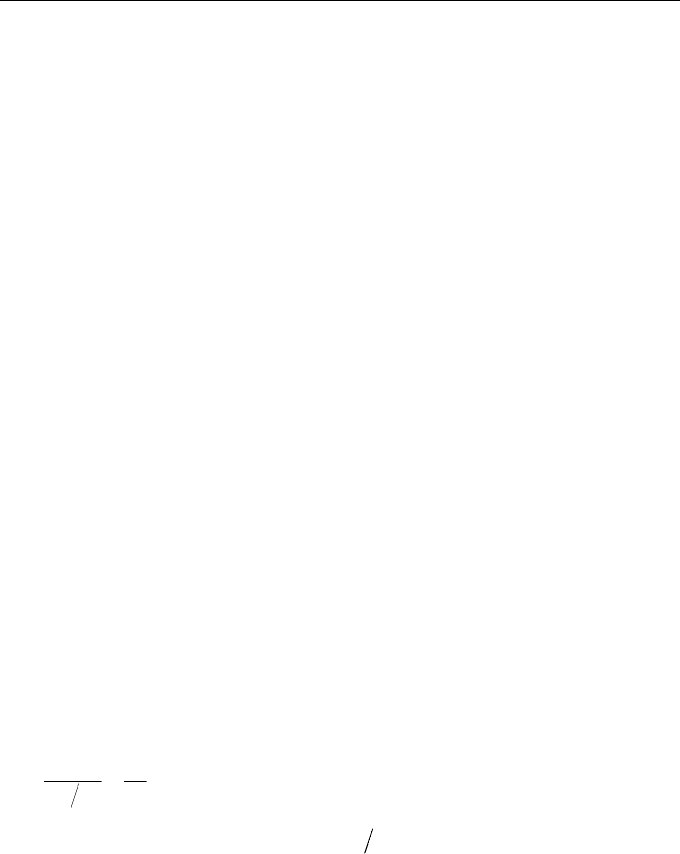
Guidelines for design of SMALL HYDROPOWER PLANTS
- 114 -
the most important source of flow disturbances and their modelling is crucial for
a reliable computational model as a design aid tool.
The turbine modelling, especially in what concerns the reaction turbines (e.g.
Francis and Kaplan turbines), the turbine couples the upstream and downstream
sides of the pressurised hydraulic circuit. In these cases, the turbine modelling
implies the knowledge of the complete characteristic curves based on the
manufactures’ tests. These curves are very difficult to obtain for small
hydroplants.
In what concerns the action turbines (e.g. Pelton turbines), the pressure transients
will need to be considered along the upstream penstock. The disturbance source
will be the turbine nozzles, a special type valve that can control the flow by
changing the position of an internal part known as the needle. In this case, as in
all pressure transients induced by a flow control device placed downstream a
long pipe, it is very important to know the characteristic equation of such control
device, or the controlled flow for each nozzle (or valve) opening and each head
variation across the upstream and downstream sides or nodes of this specific
component.
Small hydropower schemes when installed in mountainous regions are typically
associated to long penstocks, in order to increase the available head, and to
action or impulse turbines (e.g. Pelton turbines).
With computational models it is possible to include the real nozzle
characteristics and the headloss variation along the penstock during the transient
regimes. The friction headloss can be characterised by the following pipe
parameter (RAMOS, 1995):
D
fL
g2V
H
F
2
p
=
∆
=
(7.14)
where ∆H is the flow total head loss;
g2V
2
is the kinetic head; f is Darcy-
Weisbach friction factor; L the pipe or penstock length; and D the pipe or
penstock diameter.
The computer simulations indicate that for high Fp values the flow control can
be very difficult to obtain, because the time duration of the physical manoeuvre
of the nozzle or valve differs very much of the real flow change duration T
C
. In
these cases, for a nozzle linear time closure, the discharge variation will be only
effective near the full closed position: the duration of the nozzle mechanical