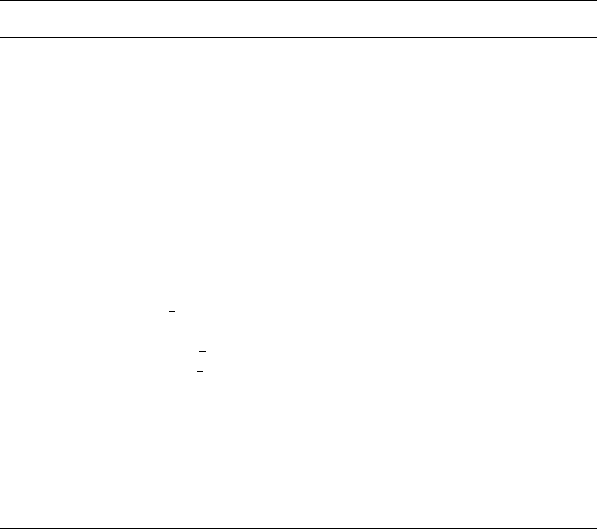
minimum of n
pmax
and n
p
. In other words, P
L
remains
constant when the number of purlin lines exceeds n
pmax
.
The brace location factor C
1
in Eq. (10.10) represents
the percentage of total restraint that is allocated to each
brace in the system. The sum of the C
1
coef®cients for the
braces in a span length is approximately equal to unity. The
values for C
1
were determined from a regression analysis
and are tabulated for each bracing con®guration in Table
10.1. For multiple span systems, the C
1
values are larger
for exterior restraints than the corresponding interior
restraints, as expected from structural mechanics.
Figure 10.16 shows a typical plot comparing the Eq.
(10.10) with, g 0, to the AISI Speci®cation Eq. (10.9) with
respect to slope angle y. Equation (10.10) predicts slightly
TABLE 10.1 Anchorage Force Coef®cients for Use in Eq. (10.10)
Bracing con®guration C
1
C
2
C
3
Support anchorages only
Single span 0.50 5.9 0.35
Multispan, exterior supports 0.50 5.9 0.35
Multispan, interior supports 1.00 9.2 0.45
Third-point anchorages
Single span 0.50 4.2 0.25
Multispan, exterior spans 0.50 4.2 0.25
Multispan, interior spans 0.45 4.2 0.35
Midspan anchorages
Single span 0.85 5.6 0.35
Multispan, exterior spans 0.80 5.6 0.35
Multispan, interior spans 0.75 5.6 0.45
Quarter-point anchorages
Single span, outside
1
4
points 0.25 5.0 0.35
Single span, midspan location 0.45 3.6 0.15
Multispan, exterior span
1
4
points 0.25 5.0 0.40
Multispan, interior span
1
4
points 0.22 5.0 0.40
Multispan, midspan locations 0.45 3.6 0.25
Third-point plus support anchorages
Single span, at supports 0.17 3.5 0.35
Single span, interior locations 0.35 3.0 0.05
Multispan, exterior support 0.17 3.5 0.35
Multispan, interior support 0.30 5.0 0.45
Multispan, third-point locations 0.35 3.0 0.10
Chapter 10
324