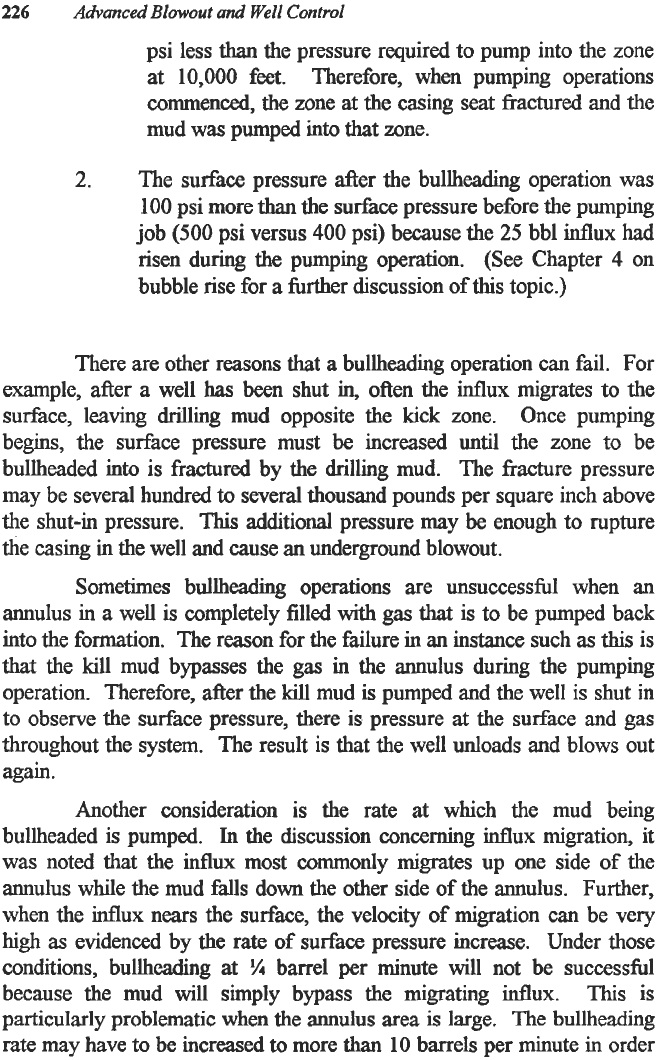
226
Advanced
Blowout
and
Well
Control
psi less
than
the pressure required to pump into the zone
at
10,000
feet. Therefore, when pumping operations
commenced, the zone at the casing seat fractured and the
mud was pumped into
that
zone.
2.
The surface pressure after the bullheadmg operation was
100
psi more
than
the surface pressure before the pumping
job
(500
psi versus
400
psi) because the
25
bbl influx
had
risen during the pumping operation. (See Chapter
4
on
bubble rise for a further discussion
of
this
topic.)
There are other reasons that
a
bullheading operation can fail. For
example, after a well
has
been shut in, often the influx migrates
to
the
sufice, leaving drilling mud opposite the kick zone. Once pumping
begins, the surface pressure must
be
increased until the zone to be
bullheaded into is fractured by the drilling mud. The fracture pressure
may be several hundred
to
several thousand pounds per square inch above
the shut-in pressure.
This
additional pressure may
be
enough to rupture
the casing in the well and cause an underground blowout.
Sometimes bullheading operations are unsuccessful when
an
annulus in a well is completely filled with gas that is to be pumped back
into the formation. The reason for the failure in an instance such
as
this
is
that
the kill mud bypasses the gas in the annulus during the pumping
operation. Therefore, after the
kill
mud is pumped and the well is shut in
to observe the surface pressure, there is pressure at the surface and
gas
throughout the system, The result is that the well
unloads
and blows out
again.
Another consideration
is
the rate
at
which the mud being
bullheaded is pumped.
In the discussion concerning influx migration, it
was noted that the influx most commonly migrates up one side of the
annulus while the mud falls down the other side of the annulus. Further,
when the influx nears the surface, the velocity of migration
can
be very
high
as
evidenced by the rate
of
surface pressure increase. Under those
conditions, bullheading
at
!4
barrel per minute will not be successful
because the mud will simply bypass the migrating influx. This is
particularly problematic when the annulus area is large. The bullheading
rate may have to be increased
to
more
than
10
barrels per minute
in
order