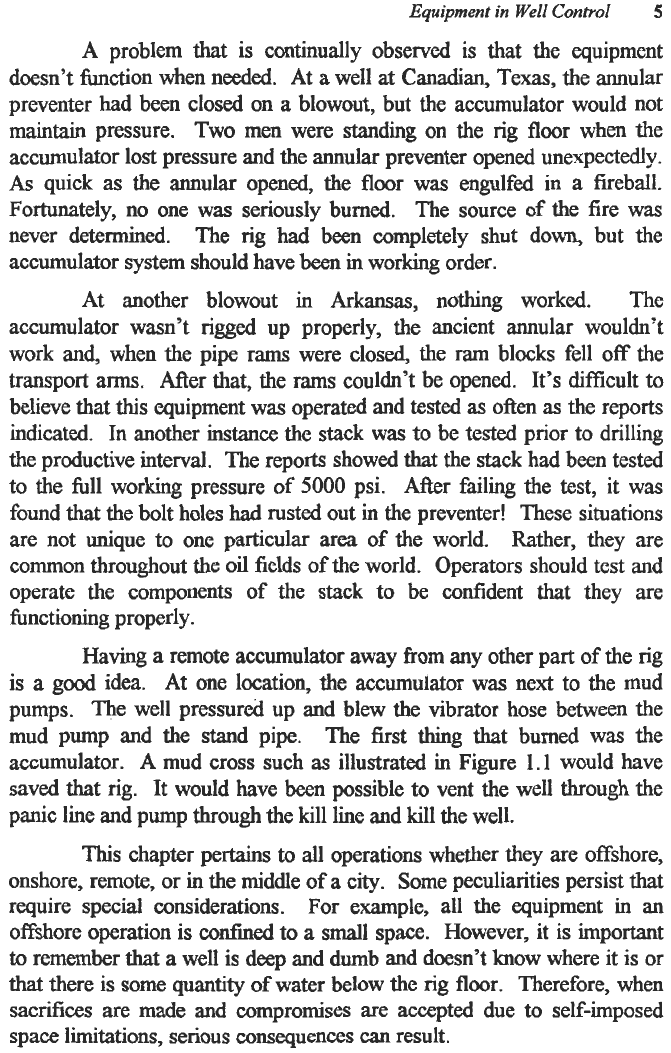
Equipment
in
Well
Control
5
A problem
that
is continually observed is that the equipment
doesn’t function when needed. At
a
well
at
Canadian,
Texas,
the annular
preventer had been closed on a blowout, but the accumulator would not
maintain pressure.
Two men were standing on the rig floor when the
accumulator lost pressure and the annular preventer opened unexpectedly.
As
quick as the annular opened, the floor was engulfed in a fireball.
Fortunately, no one was seriously burned.
The source
of
the fire was
never determined.
The rig had been completely shut down, but the
accumulator system should have
been
in working order.
At another blowout
in
Arkansas, nothing worked. The
accumulator wasn’t rigged up properly, the ancient annular wouldn‘t
work and, when the pipe
rams
were closed, the
ram
blocks fell
off
the
transport arms. After that, the rams couldn’t be opened. It’s difficult to
believe that
this
equipment was operated and tested
as
often
as
the reports
indicated. In another instance the stack
was
to be tested prior to drilling
the productive interval. The reports showed that the stack had been tested
to the fill working pressure of
5000
psi.
After failing the test, it was
found that the bolt holes
had
rusted out in the preventer! These situations
are not unique
to
one particular area of the world. Rather, they are
common throughout the
oil
fields
of
the world. Operators should test and
operate the components of the stack to be confident that they are
tknctioning properly.
Having
a
remote accumulator away
from
any other part of the rig
is
a
good idea. At one location, the accumulator was next to the mud
pumps. The well pressured up and blew the vibrator hose between the
mud pump and the stand pipe. The first thing that burned was the
accumulator. A mud cross such
as
illustrated in Figure
1.1
would have
saved that rig. It would have
been
possible to vent the well through the
panic line and pump through the kill line and kill the well.
This
chapter pertains
to
all operations whether they are offshore,
onshore, remote, or in the middle of a city. Some peculiarities persist that
require special considerations. For example, all the equipment
in
an
offshore operation
is
codmed
to
a
small space. However, it is important
to
remember that
a
well
is
deep and dumb and doesn’t
know
where it is or
that
there is some quantity of water below the rig floor. Therefore, when
sacrifices are made and compromises are accepted due to self-imposed
space limitations, serious consequences
can
result.