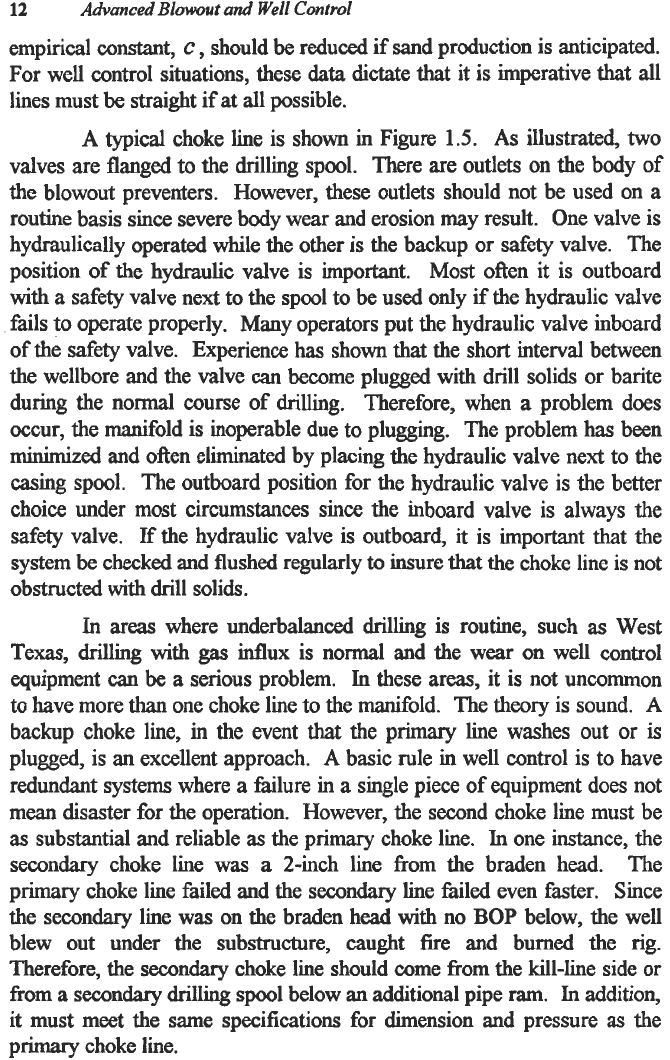
12
empirical constant,
c
,
should be reduced if sand production is anticipated.
For well control situations, these
data
dictate that it is imperative
that
all
lines must
be
straight if
at
all
possible.
A typical choke line is shown in Figure
1.5.
As
illustrated, two
valves are flanged
to
the drilling spool. There are outlets on the body of
the blowout preventers. However, these outlets should not be used on a
routine basis since severe body wear and erosion may result. One valve is
hydraulically operated while the other is the backup or safety valve. The
position of the hydraulic valve is important.
Most
often it is outboard
with a safety valve next to the spool to be used only if the hydraulic valve
fails
to
operate properly. Many operators put the hydraulic valve inboard
of the safety valve. Experience
has
shown that the short interval between
the wellbore and the valve
can
become plugged with
drill
solids or barite
during the normal course of drilling. Therefore, when
a
problem does
occur, the manifold is inoperable due to plugging. The problem
has
been
minimized and often eliminated by placing the hydraulic valve next to the
casing spool. The outboard position for the hydraulic valve is the better
choice under
most
circumstances since the inboard valve is always the
safety valve. If the hydraulic valve is outboard, it is important that the
system be checked and flushed regularly
to
insure that
the
choke line
is
not
obstructed with drill solids.
In
areas where underbalanced drilling is routine, such
as
West
Texas, drilling with
gas
influx is normal and the wear on well control
equipment
can
be
a
serious problem.
In
these areas, it is not uncommon
to have more
than
one choke line to the manifold.
The
theory is sound.
A
backup choke line, in the event
that
the primary line washes out or is
plugged, is
an
excellent approach.
A
basic rule in well control is to have
redundant systems where a fiiilure in
a
single piece of equipment does not
mean disaster for the operation. However, the second choke line must be
as
substantial and reliable
as
the primary choke line. In one instance, the
secondary choke line
was
a
2-inch line from the braden head. The
primary choke line failed and the secondary line failed even faster. Since
the secondary line was on the braden head with no
BOP
below, the well
blew out under the substructure, caught fire and burned the rig.
Therefore, the secondary choke line should come from the kill-line side or
from
a
secondary drilling spool below an additional pipe
ram.
In addition,
it must meet the same specifications for dimension and pressure
as
the
primary choke line.
Advanced
Blowout
and
Well
Cmtrol