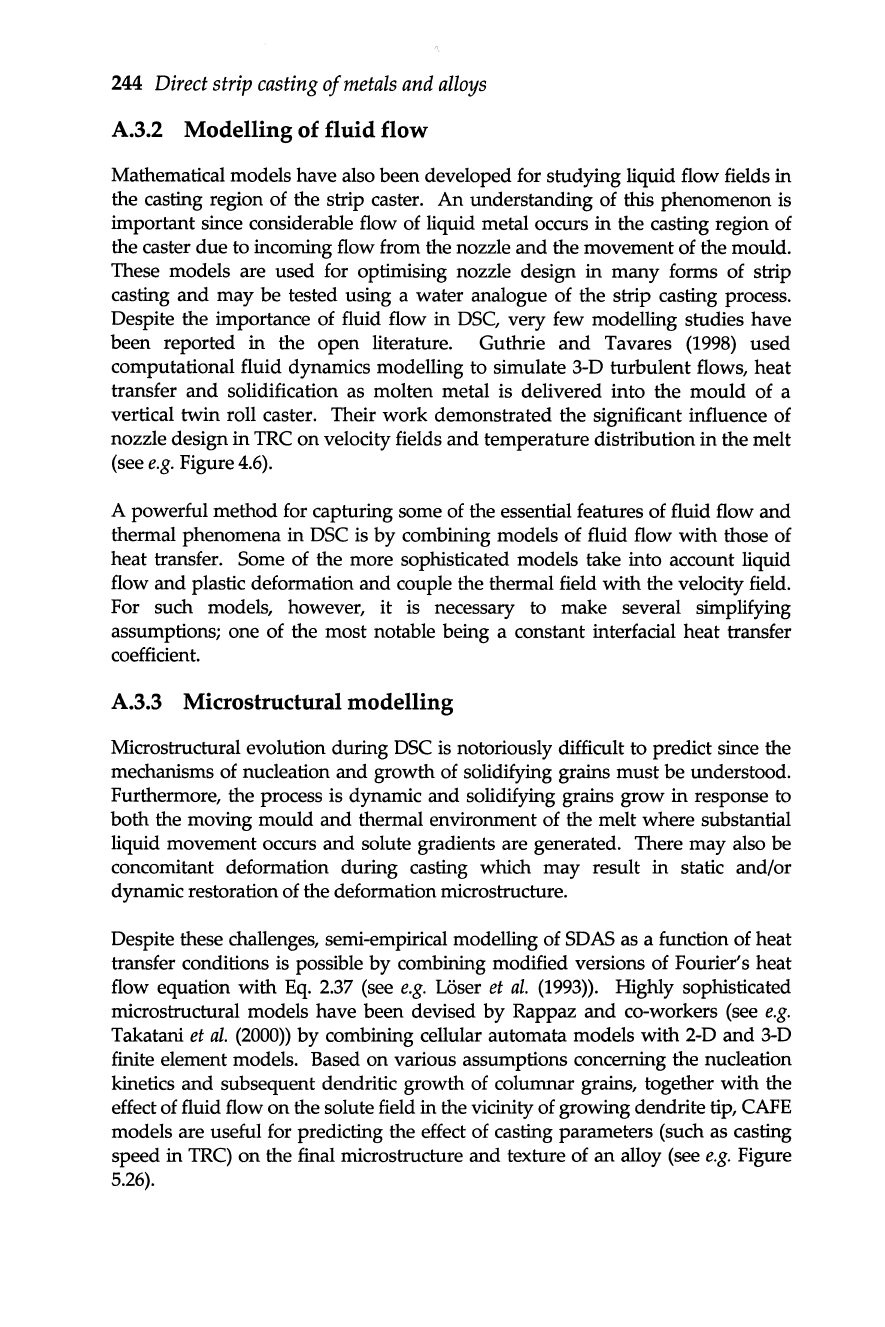
244
Direct
strip
casting
of
metals
and
alloys
A.3.2 Modelling of fluid flow
Mathematical models have also been developed for studying liquid flow fields in
the casting region of the strip caster. An understanding of
this phenomenon is
important since considerable flow of liquid metal occurs in the casting region of
the caster due to incoming flow from the nozzle and the movement of the mould.
These models are used for optimising nozzle design in many forms of strip
casting and may be tested using a water analogue of the strip casting process.
Despite the importance of fluid flow in
DSC,
very few modelling studies have
been reported in the open literature. Guthrie
and
Tavares
(1998)
used
computational fluid dynamics modelling to simulate 3-D turbulent flows, heat
transfer
and
solidification as molten metal is delivered into the mould of a
vertical
twin
roll caster. Their work demonstrated the significant influence of
nozzle design
in
TRC
on
velocity fields
and
temperature distribution
in
the melt
(see
e.g.
Figure
4.6).
A powerful method for capturing some of the essential features of fluid flow and
thermal phenomena in
DSC
is by combining models of fluid flow with those of
heat transfer. Some of the more sophisticated models take into account liquid
flow and plastic deformation and couple the thermal field with the velocity field.
For such models, however, it is necessary to make several simplifying
assumptions; one of the most notable being a constant interfacial heat transfer
coefficient.
A.3.3 Microstructural modelling
Microstructural evolution during
DSC
is notoriously difficult to predict since the
mechanisms of nucleation and growth of solidifying grains must be understood.
Furthermore, the process is dynamic and solidifying grains grow in response to
both the moving mould and thermal environment of the melt where substantial
liquid movement occurs and solute gradients are generated. There may also be
concomitant deformation during casting which may result in static and/or
dynamic restoration of the deformation microstructure.
Despite these challenges, semi-empirical modelling of
SDAS
as a function of heat
transfer conditions is possible by combining modified versions of Fourier's heat
flow equation with
Eq.
2.37
(see
e.g.
Loser
et
al.
(1993». Highly sophisticated
microstructural models have been devised by Rappaz and co-workers (see
e.g.
Takatani
et
al.
(2000»
by
combining cellular automata models with
2-D
and
3-D
finite element models. Based on various assumptions concerning the nucleation
kinetics and subsequent dendritic growth of columnar grains, together with the
effect of fluid flow
on
the solute field in the vicinity of growing dendrite tip,
CAFE
models are useful for predicting the effect of casting parameters (such as casting
speed in
TRC)
on
the final microstructure and texture of an alloy (see
e.g.
Figure
5.26).