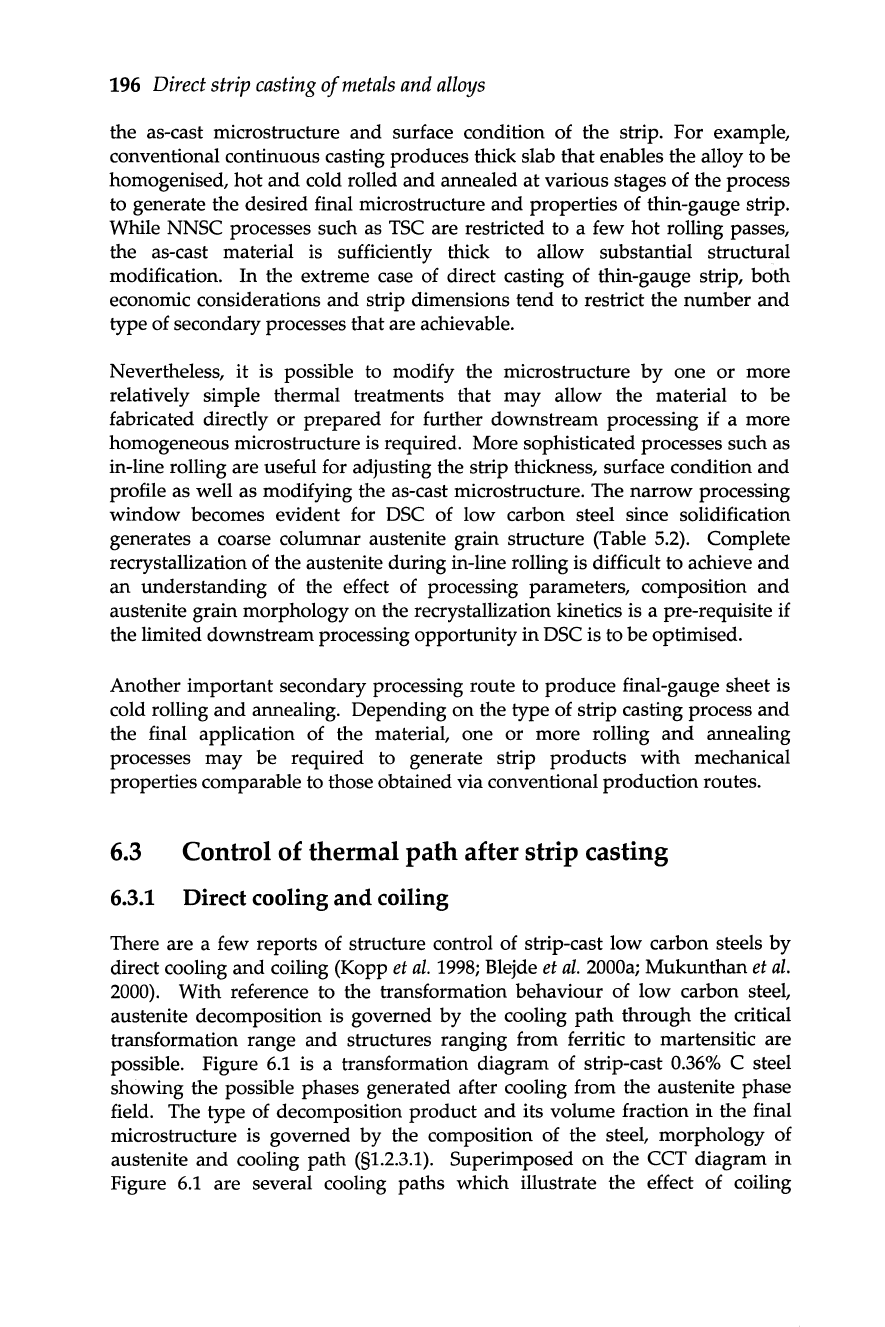
196
Direct
strip
casting
of
metals
and
alloys
the as-cast microstructure
and
surface condition of the strip. For example,
conventional continuous casting produces thick slab that enables the alloy to be
homogenised,
hot
and
cold rolled
and
annealed
at
various stages of the process
to generate the desired final microstructure
and
properties of thin-gauge strip.
While NNSC processes such as
TSC
are restricted to a few
hot
rolling passes,
the as-cast material is sufficiently thick to allow substantial structural
modification. In the extreme case of direct casting of thin-gauge strip, both
economic considerations
and
strip dimensions tend to restrict the
number
and
type of secondary processes that are achievable.
Nevertheless,
it
is possible to modify the microstructure
by
one
or
more
relatively simple thermal treatments that
may
allow the material to be
fabricated directly
or
prepared for further downstream processing if a more
homogeneous microstructure is required. More sophisticated processes such as
in-line rolling are useful for adjusting the strip thickness, surface condition and
profile as well as modifying the as-cast microstructure. The narrow processing
window
becomes evident for DSC of low carbon steel since solidification
generates a coarse columnar austenite grain structure (Table 5.2). Complete
recrystallization of the austenite during in-line rolling is difficult to achieve
and
an
understanding of the effect of processing parameters, composition
and
austenite grain morphology on the recrystallization kinetics is a pre-requisite if
the limited downstream processing opportunity
in
DSC is to be optimised.
Another important secondary processing route to produce final-gauge sheet is
cold rolling
and
annealing. Depending
on
the type of strip casting process
and
the final application of the material, one or more rolling
and
annealing
processes may be required to generate strip products
with
mechanical
properties comparable to those obtained via conventional production routes.
6.3
Control
of
thermal path after strip casting
6.3.1 Direct cooling and coiling
There are a few reports of structure control of strip-cast low carbon steels
by
direct cooling
and
coiling (Kopp
et
al.
1998; Blejde
et
al.
2000a;
Mukunthan
et
al.
2000).
With reference to the transformation behaviour of low carbon steel,
austenite decomposition is governed
by
the cooling
path
through the critical
transformation range
and
structures ranging from ferritic to martensitic are
possible. Figure
6.1
is a transformation diagram of strip-cast 0.36% C steel
showing the possible phases generated after cooling from the austenite phase
field. The type of decomposition product
and
its volume fraction
in
the final
microstructure is governed
by
the composition of the steel, morphology of
austenite
and
cooling
path
(§1.2.3.1). Superimposed
on
the CCT diagram in
Figure
6.1
are several cooling paths which illustrate the effect of coiling