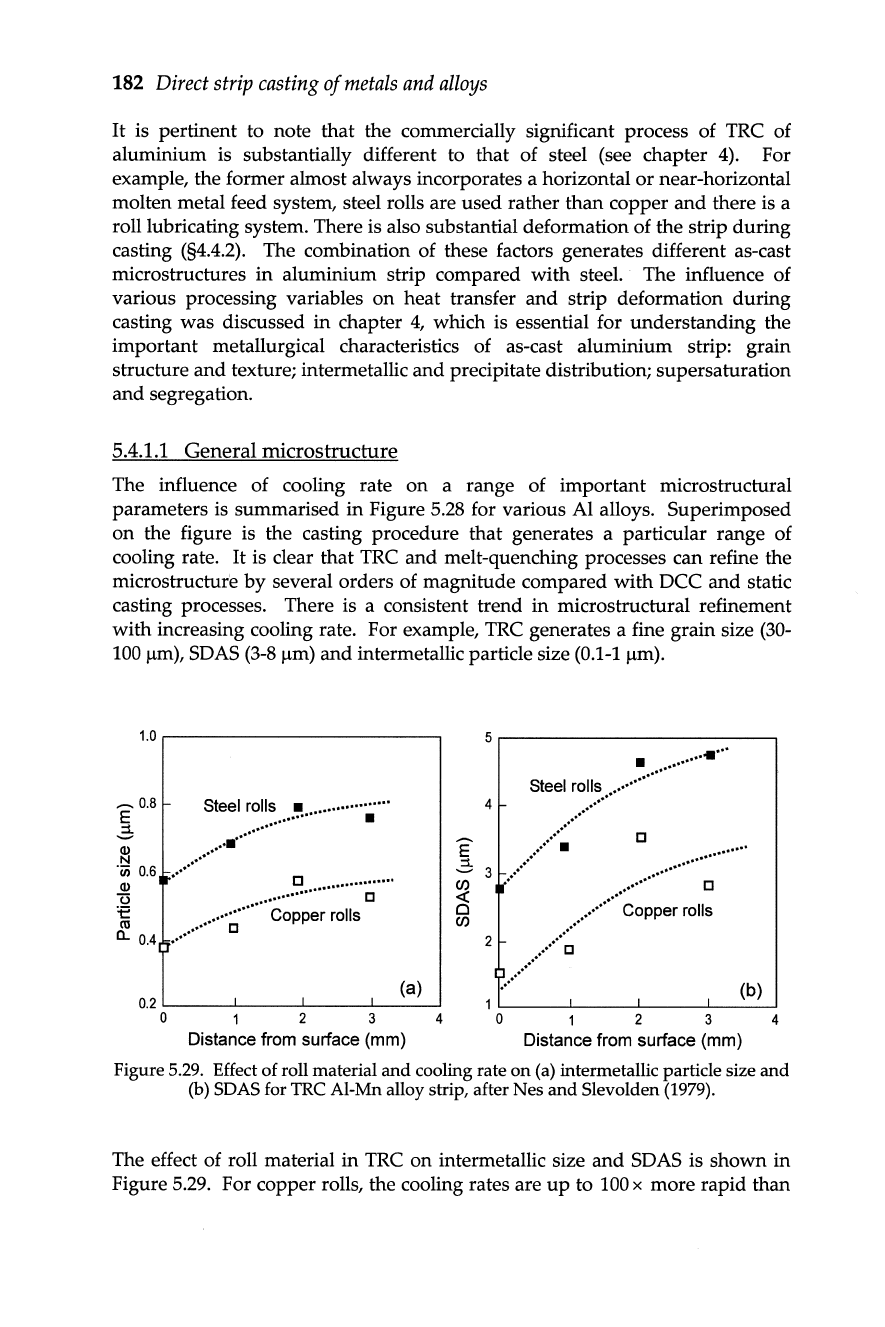
182
Direct
strip
casting
of
metals
and
alloys
It
is pertinent to note that the commercially significant process of
TRC
of
aluminium is substantially different to that of steel (see chapter
4).
For
example, the former almost always incorporates a horizontal or near-horizontal
molten metal feed system, steel rolls are used rather than copper and there is a
roll lubricating system. There is also substantial deformation of the strip during
casting
(§4.4.2).
The combination of these factors generates different as-cast
microstructures
in
aluminium strip compared with steel. The influence of
various processing variables
on
heat transfer
and
strip deformation during
casting was discussed
in
chapter
4,
which is essential for understanding the
important metallurgical characteristics of as-cast aluminium strip: grain
structure and texture; intermetalIic and precipitate distribution; supersaturation
and segregation.
5.4.1.1
General
microstructure
The influence of cooling rate
on
a range of important microstructural
parameters is summarised in Figure
5.28
for various Al alloys. Superimposed
on
the figure is the casting procedure that generates a particular range of
cooling rate.
It
is clear that
TRC
and
melt-quenching processes can refine the
microstructure
by
several orders of magnitude compared with DCC and static
casting processes. There is a consistent trend in microstructural refinement
with increasing cooling rate. For example,
TRC
generates a fine grain size
(30-
100
/lm),
SDAS
(3-8/lm) and intermetalIic particle size (O.l-l/lm).
1.0
r-------------,
.......
E
0.8
Steel rolls - ................ .
.............
-
i
....
··········
'iii
O.S
t
.•
•··
~
••••••
E!
....
••
......
·;;··
..
:e
...........
Copper rolls
III
••
' C
0.
0.4
T
••
••••••
(a)
0.2
l..-
__
-'--
__
"--
__
"--_---'
o
1 2 3
4
Distance from surface (mm)
5r------------.
-
........
.
Steel rolls
•••••••••••
......
.'
......
4
....
. '
.......
.
......
-
-§,
.'
- 3
••••
~
(
en
.'
2
••••••
~
~
......
.
. '
.'
..
'
c
...........................
......
c
••••••••
Copper
rolls
(b)
1L.-
__
"--
__
"--
__
"--_---'
o
1 2 3 4
Distance from surface (mm)
Figure 5.29. Effect
of
roll material
and
cooling rate
on
(a) intermetallic particle size
and
(b) SDAS for TRC AI-Mn alloy strip, after Nes
and
Slevolden (1979).
The effect of roll material
in
TRC
on intermetalIic size and SDAS is shown
in
Figure
5.29.
For copper rolls, the cooling rates are
up
to
100
x more rapid than