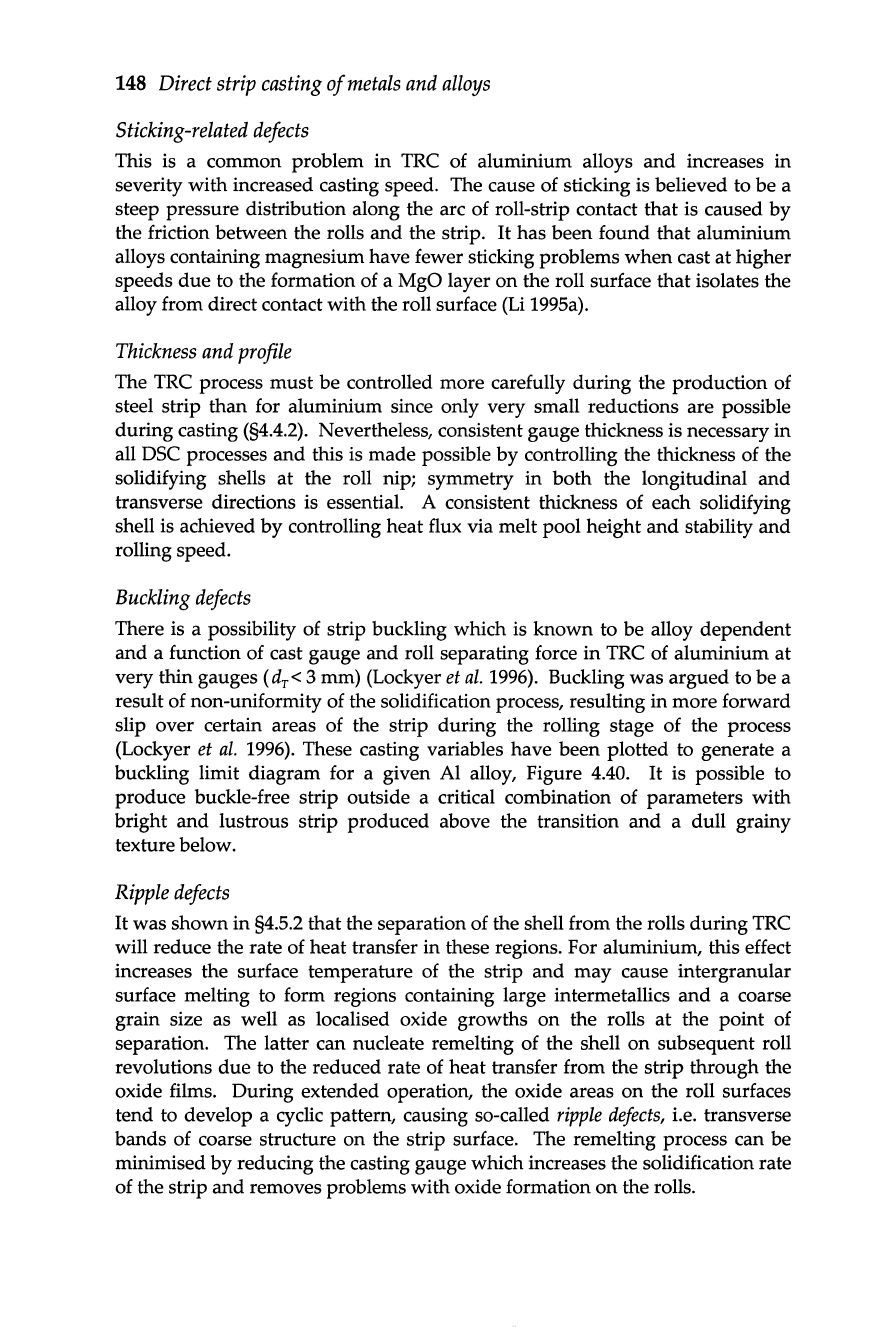
148
Direct
strip
casting
of
metals
and
alloys
Sticking-related
defects
This is a common problem in mc of aluminium alloys
and
increases in
severity with increased casting speed. The cause of sticking is believed to be a
steep pressure distribution along the arc of roll-strip contact that is caused by
the friction between the rolls and the strip.
It
has been found that aluminium
alloys containing magnesium have fewer sticking problems when cast
at
higher
speeds
due
to the formation of a MgO layer
on
the roll surface that isolates the
alloy from direct contact with the roll surface
(Li 1995a).
Thickness
and
profile
The mc process
must
be controlled more carefully during the production of
steel strip than for aluminium since only very small reductions are possible
during casting
(§4.4.2).
Nevertheless, consistent gauge thickness is necessary
in
all
DSC
processes and this is made possible
by
controlling the thickness of the
solidifying shells at the roll nip; symmetry
in
both the longitudinal and
transverse directions is essential. A consistent thickness of each solidifying
shell is achieved
by
controlling heat flux via melt pool height
and
stability and
rolling speed.
Buckling
defects
There is a possibility of strip buckling which is known to be alloy dependent
and a function of cast gauge and roll separating force
in
TRC
of aluminium
at
very thin gauges (d
r
< 3 mm) (Lockyer
et
al.
1996).
Buckling was argued to be a
result of non-uniformity of the solidification process, resulting
in
more forward
slip over certain areas of the strip during the rolling stage of the process
(Lockyer
et
al.
1996).
These casting variables have been plotted to generate a
buckling limit diagram for a given Al alloy, Figure
4.40.
It
is possible to
produce buckle-free strip outside a critical combination of parameters with
bright
and
lustrous strip produced above the transition
and
a dull grainy
texture below.
Ripple
defects
It
was shown
in
§4.5.2 that the separation of the shell from the rolls during mc
will reduce the rate of heat transfer in these regions. For aluminium, this effect
increases the surface temperature of the strip
and
may cause intergranular
surface melting to form regions containing large intermetallics
and
a coarse
grain size as well as localised oxide growths on the rolls
at
the point of
separation. The latter can nucleate remelting of the shell
on
subsequent roll
revolutions
due
to the reduced rate of heat transfer from the strip through the
oxide films. During extended operation, the oxide areas on the roll surfaces
tend to develop a cyclic pattern, causing so-called
ripple
defects,
i.e. transverse
bands of coarse structure
on
the strip surface. The remelting process can be
minimised
by
reducing the casting gauge which increases the solidification rate
of the strip and removes problems with oxide formation
on
the rolls.