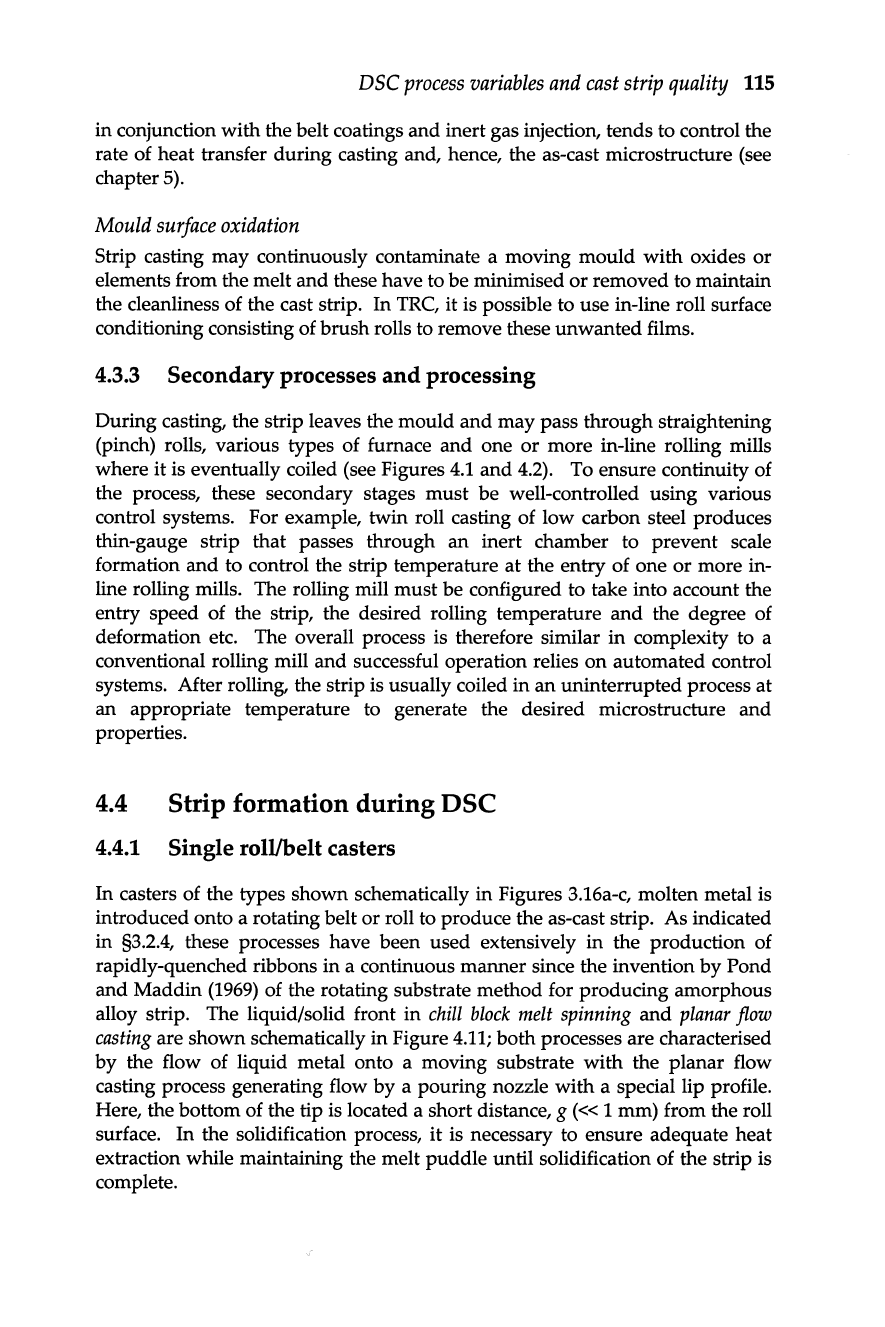
DSC
process
variables
and
cast
strip quality
115
in
conjunction
with
the belt coatings and inert gas injection, tends to control the
rate of heat transfer during casting and, hence, the as-cast microstructure (see
chapter
5).
Mould
surface
oxidation
Strip casting may continuously contaminate a moving
mould
with
oxides
or
elements from the melt and these have to be minimised
or
removed to maintain
the cleanliness of the cast strip.
In
TRC,
it
is possible to use in-line roll surface
conditioning consisting of brush rolls to remove these
unwanted
films.
4.3.3
Secondary processes
and
processing
During casting, the strip leaves the mould
and
may pass through straightening
(pinch) rolls, various types of furnace
and
one
or
more in-line rolling mills
where
it
is eventually coiled (see Figures
4.1
and
4.2). To ensure continuity of
the process, these secondary stages
must
be
well-controlled using various
control systems. For example,
twin
roll casting of low carbon steel produces
thin-gauge strip
that
passes through
an
inert chamber to prevent scale
formation
and
to control the strip temperature
at
the entry of one
or
more in-
line rolling mills. The rolling mill
must
be configured to take into account the
entry speed of the strip, the desired rolling temperature
and
the degree of
deformation etc. The overall process is therefore similar
in
complexity to a
conventional rolling mill and successful operation relies
on
automated control
systems. After rolling, the strip is usually coiled
in
an
uninterrupted process at
an
appropriate temperature to generate the desired microstructure
and
properties.
4.4 Strip formation
during
DSC
4.4.1
Single rolVbelt casters
In casters of the types shown schematically in Figures 3.16a-c, molten metal is
introduced onto a rotating belt
or
roll to produce the as-cast strip. As indicated
in §3.2.4, these processes have been used extensively
in
the production of
rapidly-quenched ribbons in a continuous manner since the invention
by
Pond
and Maddin
(1969)
of the rotating substrate method for producing amorphous
alloy strip. The liquid/solid front
in
chill
block
melt
spinning
and
planar
flow
casting
are shown schematically
in
Figure
4.11;
both processes are characterised
by
the flow of liquid metal onto a moving substrate
with
the planar flow
casting process generating flow
by
a pouring nozzle
with
a special lip profile.
Here, the bottom of the tip is located a short distance,
g
(<<
1 mm) from the roll
surface.
In
the solidification process,
it
is necessary to ensure adequate heat
extraction while maintaining the melt
puddle
until solidification of the strip is
complete.