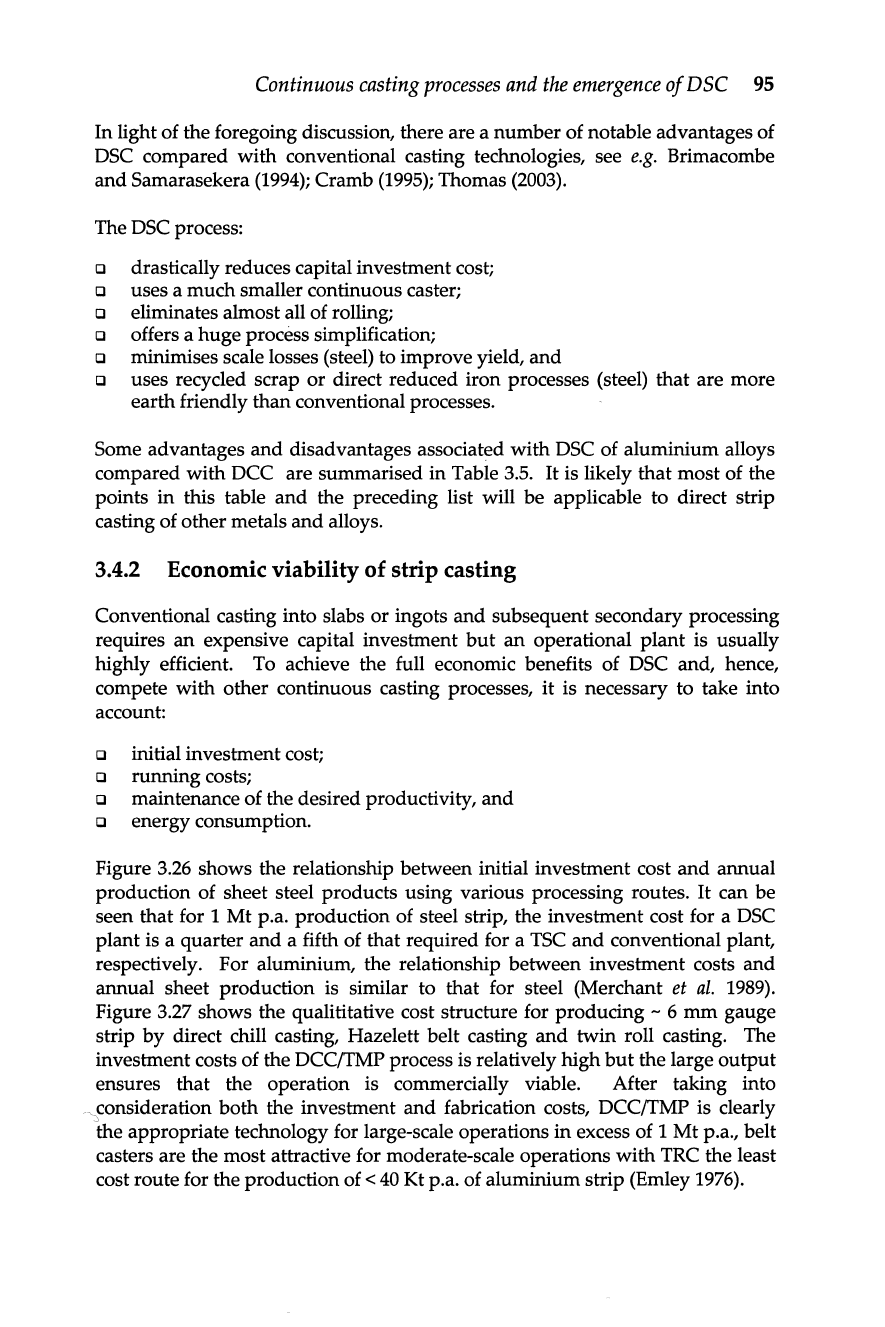
Continuous
casting
processes
and
the
emergence
of
DSC
95
In light of the foregoing discussion, there are a
number
of notable advantages of
DSC
compared with conventional casting technologies, see
e.g.
Brimacombe
and
Samarasekera
(1994);
Cramb
(1995);
Thomas
(2003).
The DSC process:
[J
drastically reduces capital investment cost;
[J
uses a
much
smaller continuous caster;
[J
eliminates almost all of rolling;
[J
offers a
huge
process simplification;
[J
minimises scale losses (steel) to improve yield,
and
[J
uses recycled scrap
or
direct reduced iron processes (steel) that are more
earth friendly than conventional processes.
Some advantages
and
disadvantages associated
with
DSC of aluminium alloys
compared
with
DCC are summarised in Table
3.5.
It
is likely that most of the
points
in
this table
and
the preceding list will be applicable to direct strip
casting of other metals
and
alloys.
3.4.2 Economic viability of strip casting
Conventional casting into slabs or ingots
and
subsequent secondary processing
requires
an
expensive capital investment
but
an
operational
plant
is usually
highly efficient. To achieve the full economic benefits of DSC and, hence,
compete with other continuous casting processes,
it
is necessary to take into
account:
[J
initial investment cost;
[J
running costs;
[J
maintenance of the desired productivity,
and
[J
energy consumption.
Figure 3.26 shows the relationship between initial investment cost
and
annual
production of sheet steel products using various processing routes.
It
can be
seen that for 1
Mt
p.a. production of steel strip, the investment cost for a DSC
plant is a quarter
and
a fifth of that required for a
TSC
and
conventional plant,
respectively. For aluminium, the relationship between investment costs
and
annual sheet production is similar to that for steel (Merchant et
al.
1989).
Figure 3.27 shows the qualititative cost structure for producing - 6
mm
gauge
strip
by
direct chill casting, Hazelett belt casting
and
twin roll casting. The
investment costs of the
DCC(fMP process is relatively high
but
the large
output
ensures that the operation is commercially viable. After taking into
.consideration
both
the investment
and
fabrication costs,
DCC(fMP
is clearly
the appropriate technology for large-scale operations
in
excess of 1
Mt
p.a., belt
casters are the most attractive for moderate-scale operations
with
TRC the least
cost route for the production of
<
40
Kt p.a. of aluminium strip (Emley
1976).