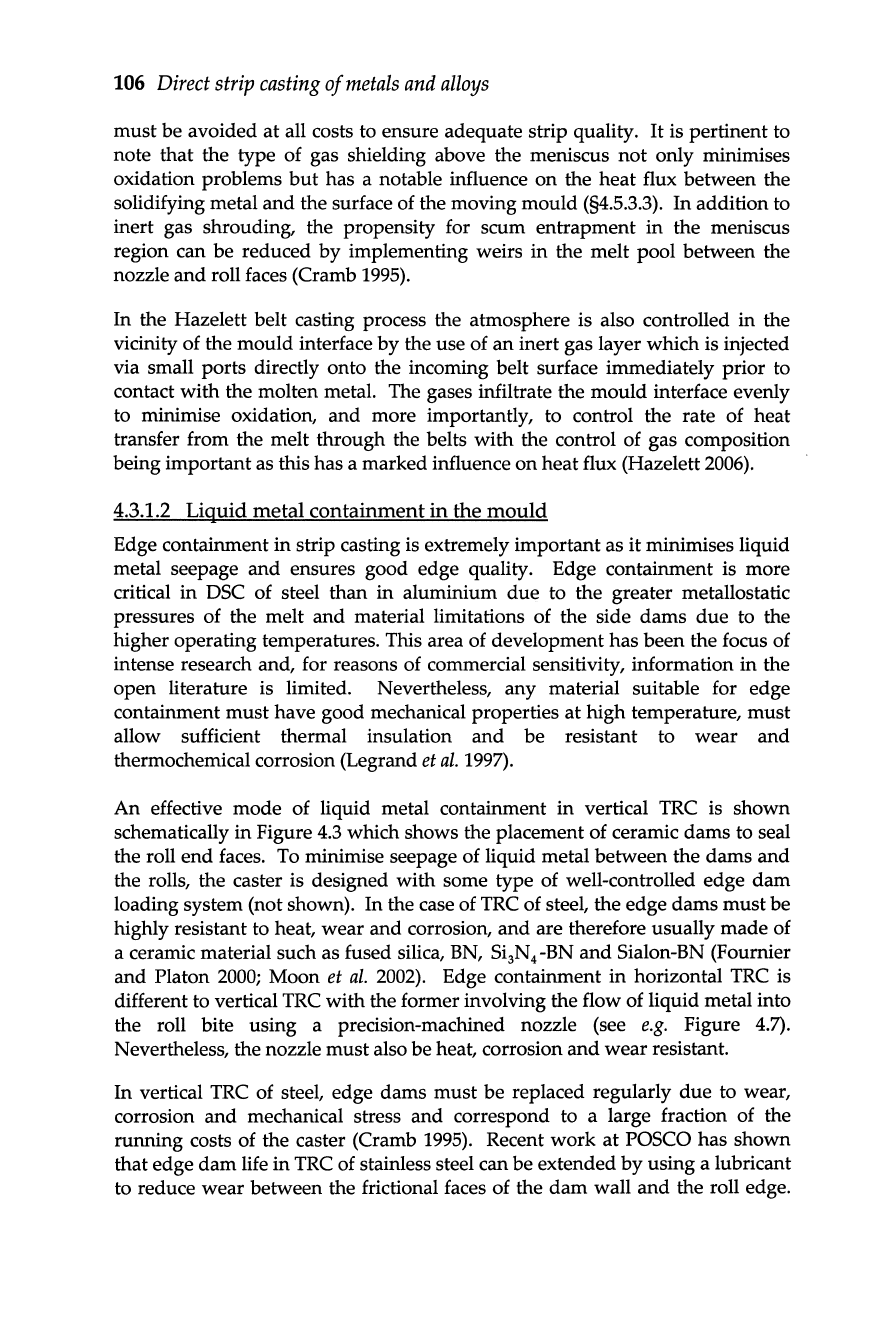
106
Direct
strip
casting
of
metals
and
alloys
must be avoided
at
all costs to ensure adequate strip quality.
It
is pertinent to
note that the type of gas shielding above the meniscus
not
only minimises
oxidation problems
but
has a notable influence
on
the heat flux between the
solidifying metal and the surface of the moving mould
(§4.5.3.3). In addition to
inert gas shrouding, the propensity for scum entrapment
in
the meniscus
region can be reduced
by
implementing weirs
in
the melt pool between the
nozzle and roll faces (Cramb
1995).
In the Hazelett belt casting process the atmosphere is also controlled in the
vicinity of the mould interface
by
the use of
an
inert gas layer which is injected
via small ports directly onto the incoming belt surface immediately prior to
contact with the molten metal. The gases infiltrate the mould interface evenly
to minimise oxidation, and more importantly, to control the rate of heat
transfer from the melt through the belts with the control of gas composition
being important as this has a marked influence
on
heat flux (Hazelett
2006).
4.3.1.2 Liquid metal containment
in
the mould
Edge containment in strip casting is extremely important as it minimises liquid
metal seepage
and
ensures good edge quality. Edge containment is more
critical
in
DSC of steel than
in
aluminium
due
to the greater metallostatic
pressures of the melt
and
material limitations of the side dams
due
to the
higher operating temperatures. This area of development has been the focus of
intense research and, for reasons of commercial sensitivity, information
in
the
open literature is limited. Nevertheless, any material suitable for edge
containment
must
have good mechanical properties at high temperature, must
allow sufficient thermal insulation
and
be resistant to wear
and
thermochemical corrosion (Legrand
et
al.
1997).
An effective mode of liquid metal containment
in
vertical TRC is shown
schematically
in
Figure 4.3 which shows the placement of ceramic dams to seal
the roll end faces. To minimise seepage of liquid metal between the dams
and
the rolls, the caster is designed with some type of well-controlled edge
dam
loading system (not shown).
In
the case of
TRC
of steel, the edge dams
must
be
highly resistant to heat, wear and corrosion, and are therefore usually made of
a ceramic material such as fused silica,
BN,
Si3N4
-BN
and
Sialon-BN (Fournier
and Platon
2000;
Moon
et
al.
2002).
Edge containment
in
horizontal
TRC
is
different to vertical
TRC
with the former involving the flow of liquid metal into
the roll bite using a precision-machined nozzle (see
e.g.
Figure 4.7).
Nevertheless, the nozzle must also be heat, corrosion
and
wear resistant.
In
vertical
TRC
of steel, edge dams must be replaced regularly
due
to wear,
corrosion and mechanical stress and correspond to a large fraction of the
running costs of the caster (Cramb
1995).
Recent work
at
pasco has shown
that edge
dam
life
in
TRC of stainless steel can be extended
by
using a lubricant
to reduce wear between the frictional faces of the
dam
wall
and
the roll edge.