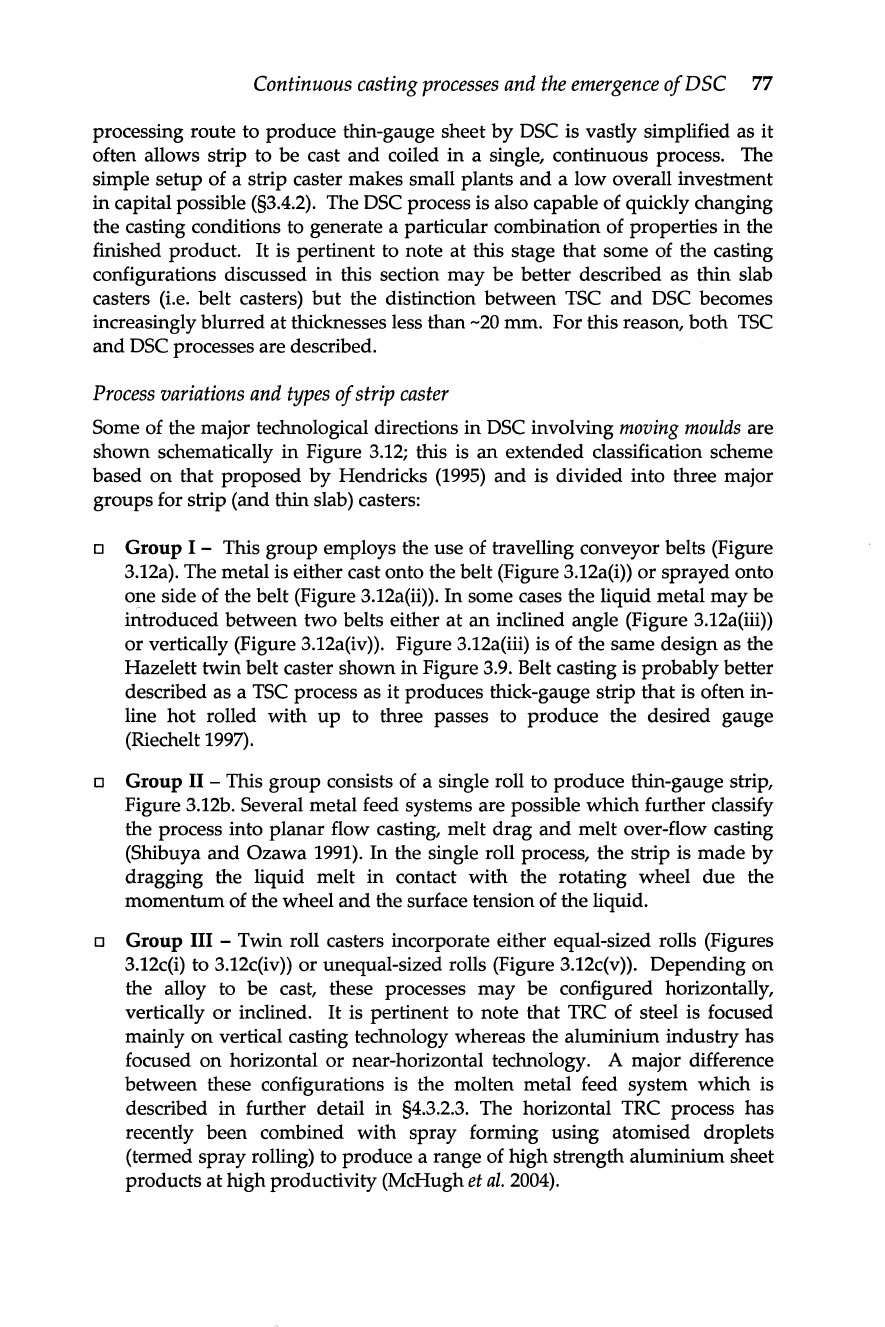
Continuous
casting
processes
and
the
emergence
of
DSC
77
processing route to produce thin-gauge sheet
by
DSC is vastly simplified as
it
often allows strip to be cast
and
coiled in a single, continuous process. The
simple setup of a strip caster makes small plants
and
a low overall investment
in capital possible (§3.4.2). The DSC process is also capable of quickly changing
the casting conditions to generate a particular combination of properties in the
finished product.
It
is pertinent to note
at
this stage that some of the casting
configurations discussed in this section
may
be better described as thin slab
casters (i.e. belt casters)
but
the distinction between
TSC
and
DSC becomes
increasingly blurred
at
thicknesses less than -20 mm. For this reason, both
TSC
and
DSC processes are described.
Process
variations
and
types
of strip
caster
Some of the major technological directions
in
DSC involving moving
moulds
are
shown schematically in Figure
3.12;
this is
an
extended classification scheme
based
on
that proposed
by
Hendricks
(1995)
and
is divided into three major
groups for strip (and thin slab) casters:
o
Group
I - This
group
employs the use of travelling conveyor belts (Figure
3.12a). The metal is either cast onto the belt (Figure 3.12a(i))
or
sprayed onto
one side of the belt (Figure 3.12a(ii)). In some cases the liquid metal
may
be
introduced between two belts either
at
an
inclined angle (Figure 3.12a(iii))
or
vertically (Figure 3.12a(iv)). Figure 3.12a(iii) is of the same design as the
Hazelett twin belt caster shown in Figure 3.9. Belt casting is probably better
described as a
TSC
process as
it
produces thick-gauge strip
that
is often in-
line
hot
rolled
with
up
to three passes to produce the desired gauge
(Riechelt 1997).
o
Group
II - This
group
consists of a single roll to produce thin-gauge strip,
Figure 3.12b. Several metal feed systems are possible which further classify
the process into planar flow casting, melt
drag
and
melt over-flow casting
(Shibuya
and
Ozawa 1991). In the single roll process, the strip is
made
by
dragging the liquid melt in contact
with
the rotating wheel
due
the
momentum of the wheel
and
the surface tension of the liquid.
o
Group
III
- Twin roll casters incorporate either equal-sized rolls (Figures
3.12c(i) to 3.12c(iv))
or
unequal-sized rolls (Figure 3.12c(v)). Depending
on
the alloy to be cast, these processes
may
be
configured horizontally,
vertically
or
inclined.
It
is pertinent to note that TRC of steel is focused
mainly
on
vertical casting technology whereas the aluminium industry has
focused
on
horizontal
or
near-horizontal technology. A major difference
between these configurations is the molten metal feed system which is
described in further detail in §4.3.2.3. The horizontal TRC process has
recently been combined
with
spray forming using atomised droplets
(termed spray rolling) to produce a range of high strength aluminium sheet
products
at
high productivity (McHugh et
al.
2004).