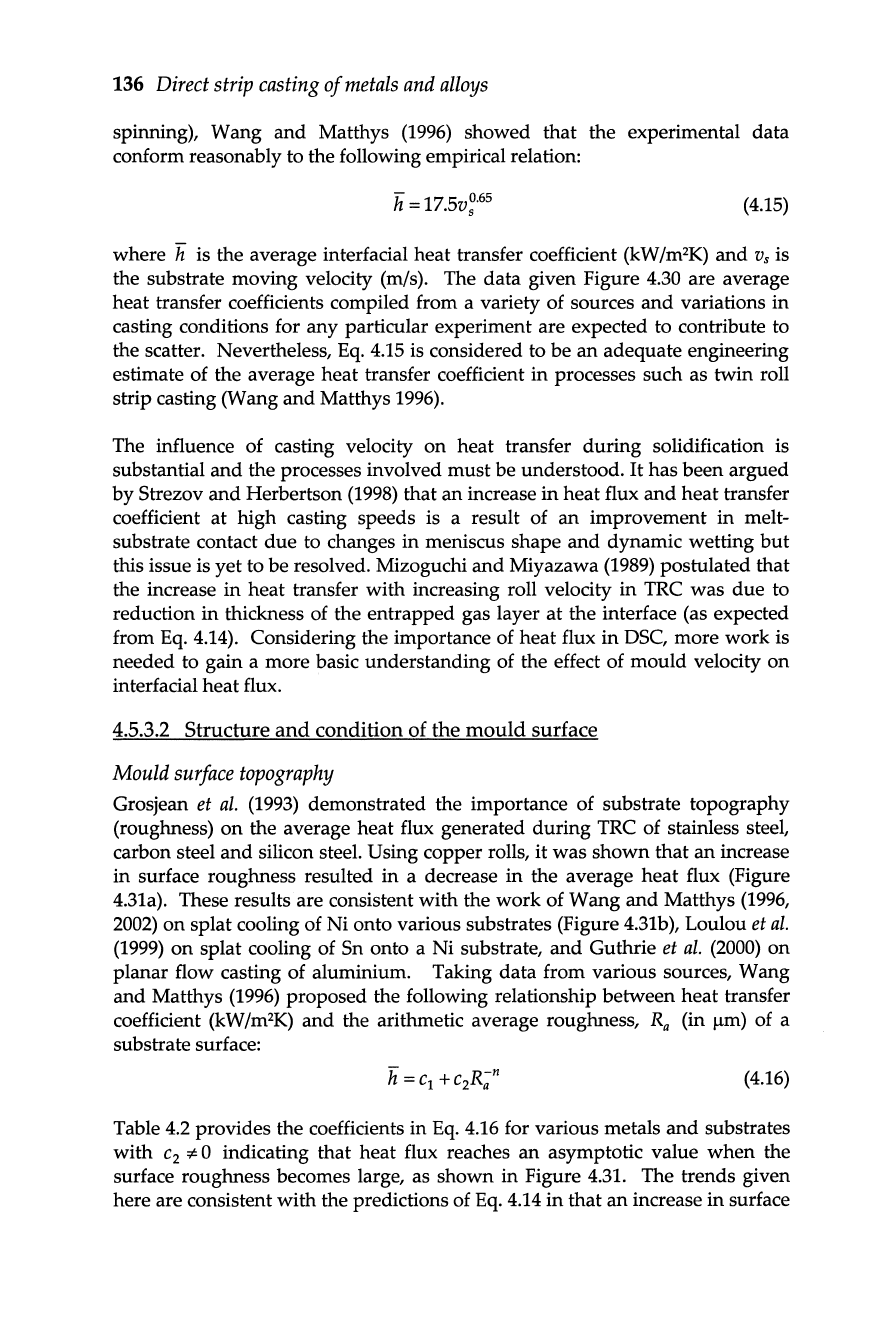
136
Direct
strip
casting
of
metals
and
alloys
spinning), Wang
and
Matthys
(1996)
showed that the experimental data
conform reasonably to the following empirical relation:
(4.15)
where
Ii
is the average interfacial heat transfer coefficient (kW/m2K)
and
Vs is
the substrate moving velocity (m/s). The
data
given Figure 4.30 are average
heat transfer coefficients compiled from a variety of sources
and
variations in
casting conditions for any particular experiment are expected to contribute to
the scatter. Nevertheless,
Eq.
4.15
is considered to be
an
adequate engineering
estimate of the average heat transfer coefficient in processes such as twin roll
strip casting (Wang
and
Matthys
1996).
The influence of casting velocity
on
heat transfer
during
solidification is
substantial
and
the processes involved
must
be understood.
It
has been argued
by
Strezov
and
Herbertson
(1998)
that an increase in heat flux
and
heat transfer
coefficient
at
high casting speeds is a result of
an
improvement
in
melt-
substrate contact
due
to changes in meniscus shape
and
dynamic wetting
but
this issue is yet to be resolved. Mizoguchi
and
Miyazawa
(1989)
postulated that
the increase in heat transfer
with
increasing roll velocity
in
TRC
was
due
to
reduction
in
thickness of the entrapped gas layer
at
the interface (as expected
from Eq. 4.14). Considering the importance of heat flux
in
DSC, more
work
is
needed to gain a more basic understanding of the effect of mould velocity
on
interfacial heat flux.
4.5.3.2
Structure
and
condition
of
the
mould
surface
Mould
surface
topography
Grosjean
et
al.
(1993)
demonstrated the importance of substrate topography
(roughness)
on
the average heat flux generated
during
TRC of stainless steel,
carbon steel
and
silicon steel. Using copper rolls, it
was
shown
that
an
increase
in
surface roughness resulted in a decrease in the average
heat
flux (Figure
4.31a). These results are consistent
with
the work of Wang
and
Matthys
(1996,
2002)
on
splat cooling of Ni onto various substrates (Figure 4.31b), Loulou
et
ai.
(1999)
on
splat cooling of Sn onto a Ni substrate,
and
Guthrie
et
ai.
(2000)
on
planar flow casting of aluminium. Taking
data
from various sources, Wang
and
Matthys
(1996)
proposed the following relationship between heat transfer
coefficient (kW/m2K)
and
the arithmetic average roughness,
Ra
(in !lm) of a
substrate surface:
(4.16)
Table
4.2
provides the coefficients in
Eq.
4.16 for various metals
and
substrates
with
c
2
;I.
0 indicating that heat flux reaches
an
asymptotic value
when
the
surface roughness becomes large, as shown in Figure 4.31. The trends given
here are consistent
with
the predictions of Eq. 4.14 in that
an
increase in surface