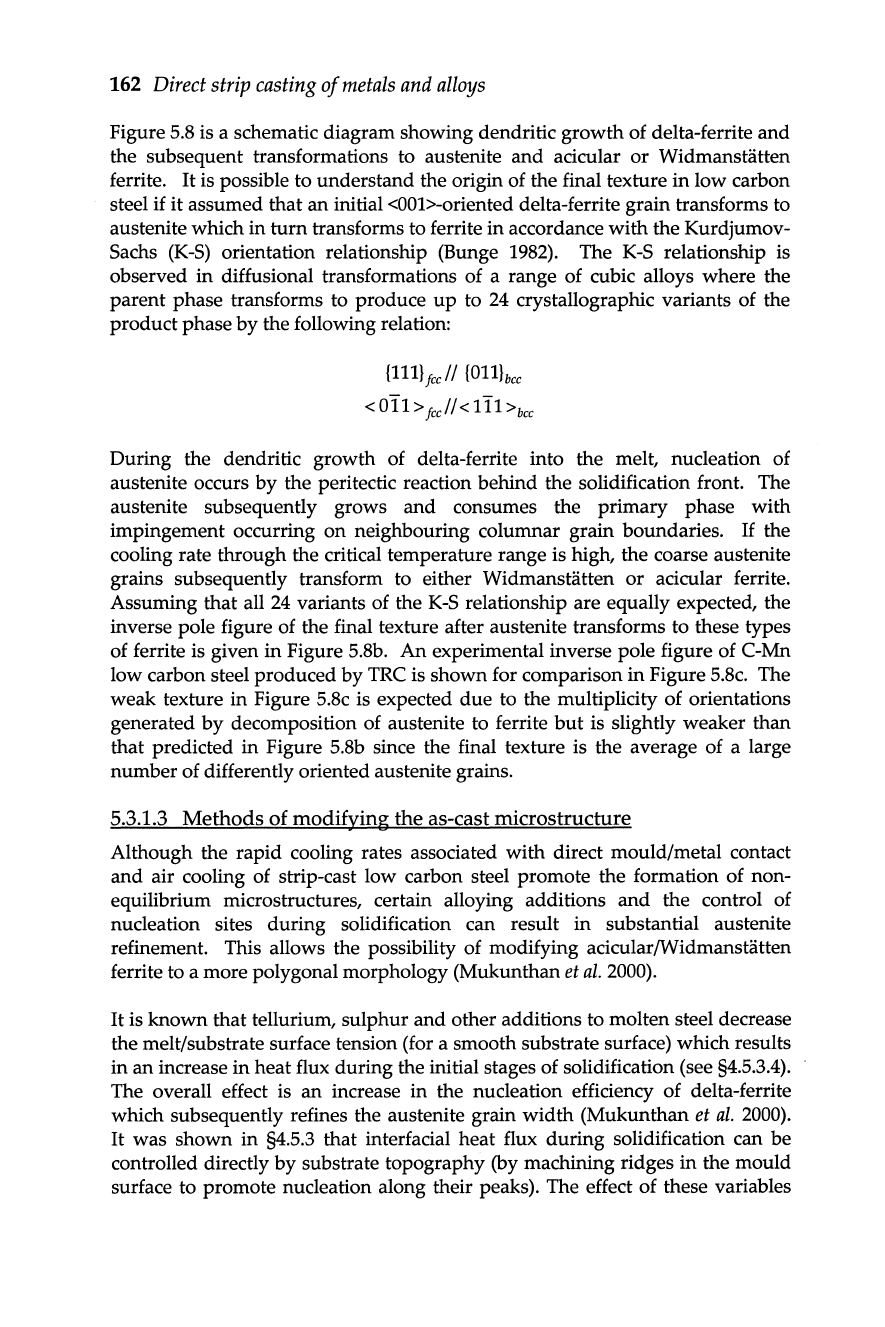
162
Direct
strip
casting
of
metals
and
alloys
Figure 5.8 is a schematic diagram showing dendritic growth of delta-ferrite
and
the subsequent transformations to austenite and acicular
or
Widmanstatten
ferrite.
It
is possible to understand the origin of the final texture
in
low carbon
steel if
it
assumed that an initial <OOl>-oriented delta-ferrite grain transforms to
austenite which in
turn
transforms to ferrite
in
accordance
with
the Kurdjumov-
Sachs
(K-S)
orientation relationship (Bunge
1982).
The
K-S
relationship is
observed in diffusional transformations of a range of cubic alloys where the
parent
phase transforms to produce
up
to
24
crystallographic variants of the
product
phase
by
the following relation:
{lll}feell
{Ollhee
< 011 >
fcc
II < 111
>bce
During the dendritic growth of delta-ferrite into the melt, nucleation of
austenite occurs
by
the peritectic reaction behind the solidification front. The
austenite subsequently grows
and
consumes the primary phase
with
impingement occurring
on
neighbouring columnar grain boundaries.
If
the
cooling rate through the critical temperature range is high, the coarse austenite
grains subsequently transform to either Widmanstatten
or
acicular ferrite.
Assuming that all
24
variants of the
K-S
relationship are equally expected, the
inverse pole figure of the final texture after austenite transforms to these types
of ferrite is given
in
Figure 5.8b.
An
experimental inverse pole figure of C-Mn
low carbon steel produced
by
TRC
is shown for comparison in Figure 5.8c. The
weak texture in Figure 5.8c is expected
due
to the multiplicity of orientations
generated
by
decomposition of austenite to ferrite
but
is slightly weaker
than
that predicted in Figure 5.8b since the final texture is the average of a large
number of differently oriented austenite grains.
5.3.1.3
Methods
of
modifying
the
as-cast
microstructure
Although the rapid cooling rates associated
with
direct mould/metal contact
and
air cooling of strip-cast low carbon steel promote the formation of non-
equilibrium microstructures, certain alloying additions
and
the control of
nucleation sites
during
solidification can result
in
substantial austenite
refinement. This allows the possibility of modifying acicular/Widmanstatten
ferrite to a more polygonal morphology (Mukunthan
et
al. 2000).
It
is
known
that tellurium,
sulphur
and
other additions to molten steel decrease
the melt/substrate surface tension (for a smooth substrate surface) which results
in an increase
in
heat flux during the initial stages of solidification (see §4.5.3.4).
The overall effect is
an
increase in the nucleation efficiency of delta-ferrite
which subsequently refines the austenite grain
width
(Mukunthan et al. 2000).
It
was shown in §4.5.3 that interfacial heat flux
during
solidification can be
controlled directly
by
substrate topography (by machining ridges
in
the mould
surface to promote nucleation along their peaks). The effect of these variables