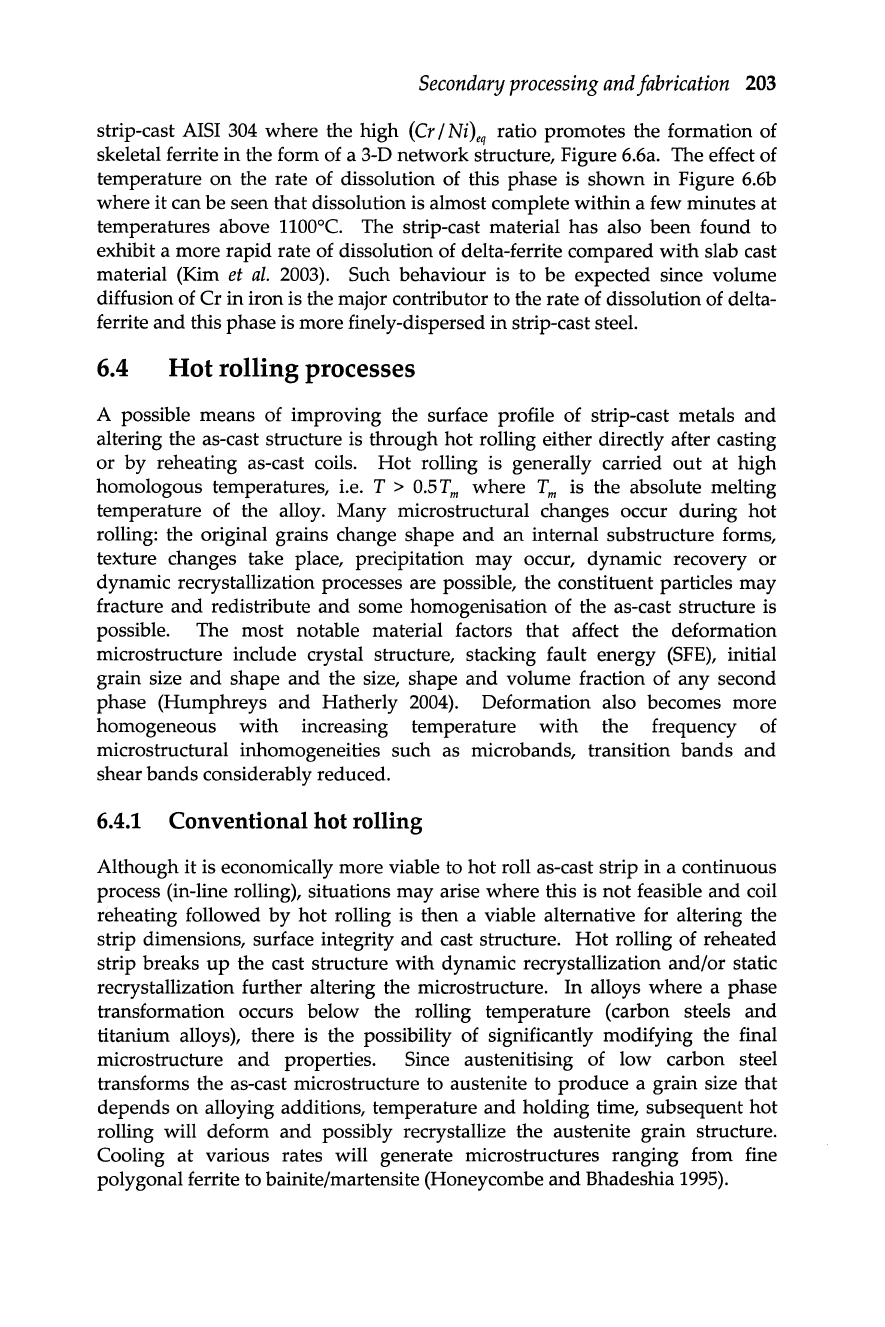
Secondary
processing
and
fabrication
203
strip-cast
AISI
304 where the high
(Cr
/
Ni)eq
ratio promotes the formation of
skeletal ferrite in the form of a 3-D network structure, Figure 6.6a. The effect of
temperature on the rate of dissolution of this phase is shown in Figure 6.6b
where it can be seen that dissolution is almost complete within a few minutes at
temperatures above
1l00°C. The strip-cast material has also been found to
exhibit a more rapid rate of dissolution of delta-ferrite compared
with
slab cast
material (Kim
et
al.
2003).
Such behaviour is to be expected since volume
diffusion of Cr
in
iron is the major contributor to the rate of dissolution of delta-
ferrite and this phase is more finely-dispersed
in
strip-cast steel.
6.4
Hot rolling processes
A possible means of improving the surface profile of strip-cast metals and
altering the as-cast structure is through
hot
rolling either directly after casting
or
by
reheating as-cast coils.
Hot
rolling is generally carried
out
at
high
homologous temperatures, i.e.
T >
0.5Tm
where
Tm
is the absolute melting
temperature of the alloy. Many microstructural changes occur during
hot
rolling: the original grains change shape
and
an internal substructure forms,
texture changes take place, precipitation may occur, dynamic recovery or
dynamic recrystallization processes are possible, the constituent particles may
fracture
and
redistribute and some homogenisation of the as-cast structure is
possible. The most notable material factors that affect the deformation
microstructure include crystal structure, stacking fault energy
(SFE),
initial
grain size and shape and the size, shape
and
volume fraction of any second
phase (Humphreys
and
Hatherly
2004).
Deformation also becomes more
homogeneous with increasing temperature
with
the frequency of
microstructural inhomogeneities such as microbands, transition bands
and
shear bands considerably reduced.
6.4.1
Conventional hot rolling
Although it is economically more viable to
hot
roll as-cast strip
in
a continuous
process (in-line rolling), situations may arise where this is
not
feasible and coil
reheating followed by
hot
rolling is then a viable alternative for altering the
strip dimensions, surface integrity
and
cast structure.
Hot
rolling of reheated
strip breaks
up
the cast structure with dynamic recrystallization and/or static
recrystallization further altering the microstructure. In alloys where a phase
transformation occurs below the rolling temperature (carbon steels and
titanium alloys), there is the possibility of significantly modifying the final
microstructure and properties. Since austenitising of low carbon steel
transforms the as-cast microstructure to austenite to produce a grain size that
depends on alloying additions, temperature
and
holding time, subsequent hot
rolling will deform
and
possibly recrystallize the austenite grain structure.
Cooling at various rates will generate microstructures ranging from fine
polygonal ferrite to bainite/martensite (Honeycombe
and
Bhadeshia
1995).