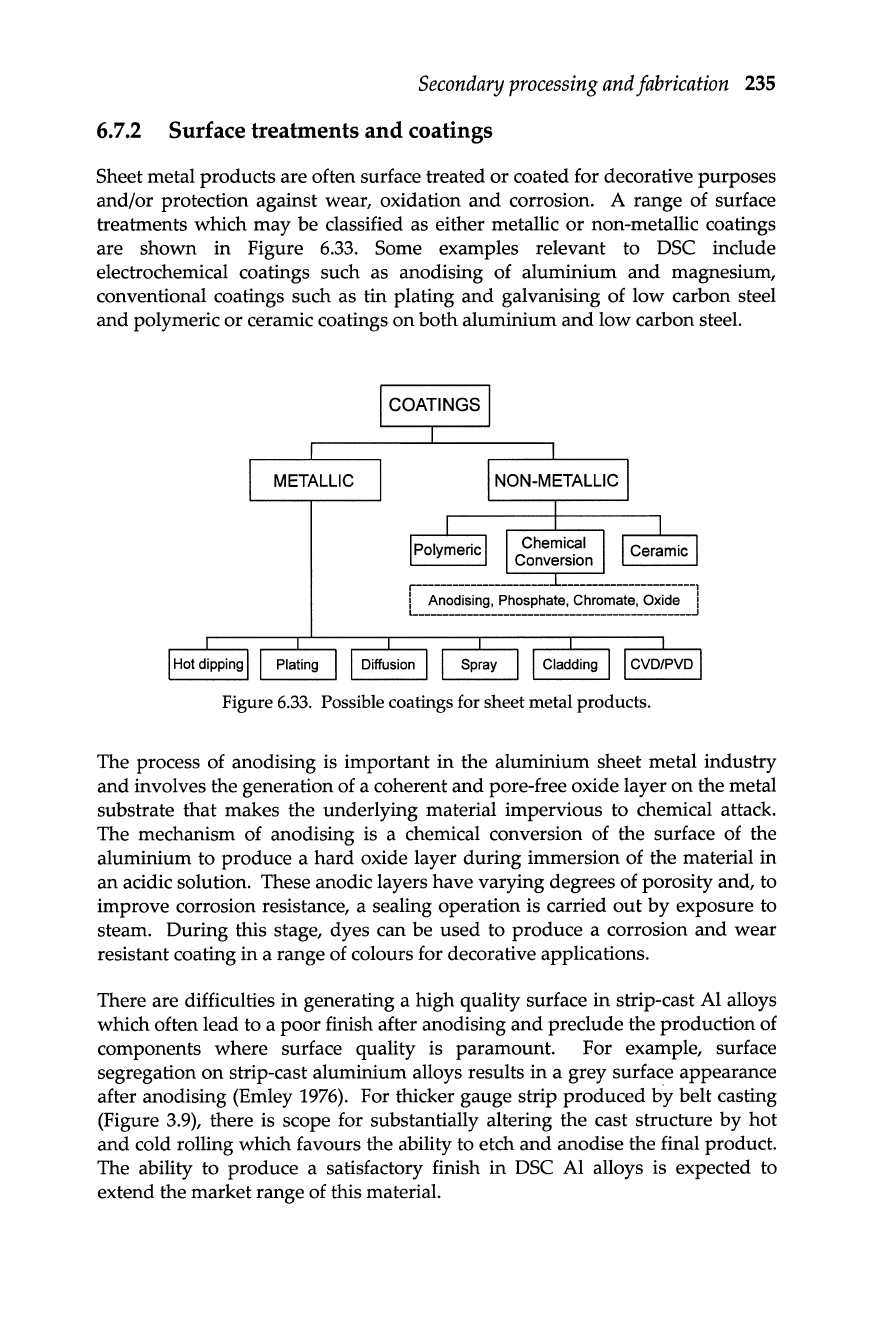
Secondary
processing
and
fabrication
235
6.7.2
Surface treatments and coatings
Sheet metal products are often surface treated
or
coated for decorative purposes
and/or protection against wear, oxidation
and
corrosion. A range of surface
treatments which may be classified as either metallic or non-metallic coatings
are shown in Figure
6.33.
Some examples relevant to
DSC
include
electrochemical coatings such as anodising of aluminium
and
magnesium,
conventional coatings such as tin plating
and
galvanising of low carbon steel
and polymeric or ceramic coatings
on
both aluminium
and
low carbon steel.
,---------
-----------1
i Anodising, Phosphate, Chromate, Oxide J
,------------------------------------
Figure
6.33.
Possible coatings for sheet metal products.
The process of anodising is important
in
the aluminium sheet metal industry
and
involves the generation of a coherent and pore-free oxide layer
on
the metal
substrate that makes the underlying material impervious to chemical attack.
The mechanism of anodising is a chemical conversion of the surface of the
aluminium to produce a
hard
oxide layer during immersion of the material in
an acidic solution. These anodic layers have varying degrees of porosity and, to
improve corrosion resistance, a sealing operation is carried
out
by
exposure to
steam. During this stage, dyes can be used to produce a corrosion and wear
resistant coating in a range of colours for decorative applications.
There are difficulties
in
generating a high quality surface in strip-cast Al alloys
which often lead to a poor finish after anodising
and
preclude the production of
components where surface quality is paramount. For example, surface
segregation
on
strip-cast aluminium alloys results
in
a grey surface appearance
after anodising (Emley
1976).
For thicker gauge strip produced
by
belt casting
(Figure
3.9),
there is scope for substantially altering the cast structure by hot
and cold rolling which favours the ability to etch and anodise the final product.
The ability to produce a satisfactory finish
in
DSC Al alloys is expected to
extend the market range of this material.