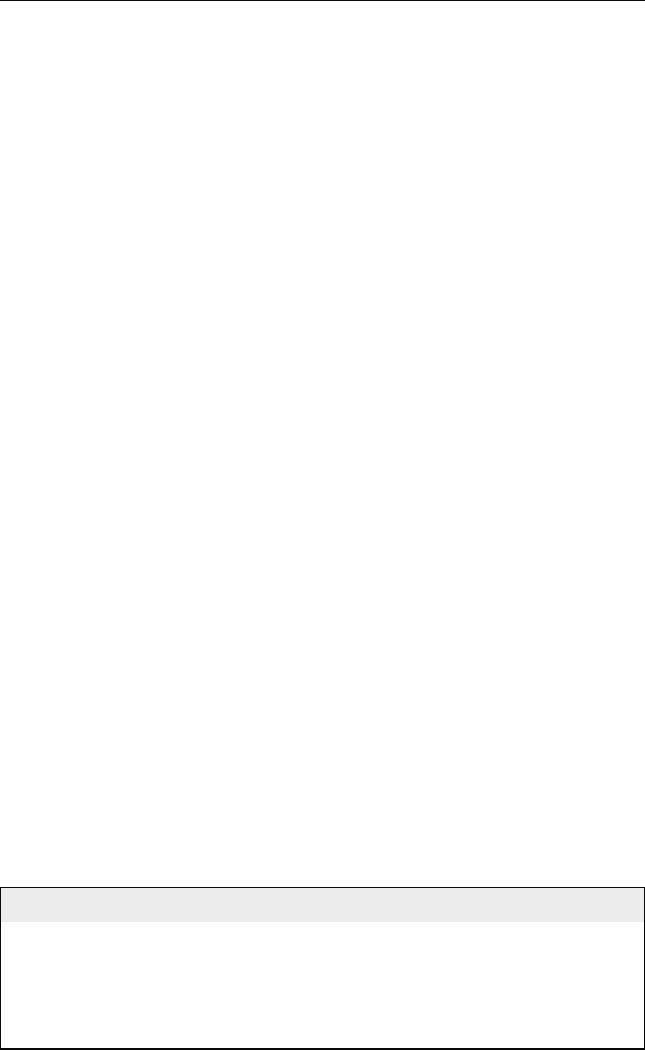
The feed is introduced into the heaterwheresteamisinjected(to
prevent c oking ) to a temperature below 371
C(700
F). The heat ed
recycled hydrogen is mixed with feed and together, they are introduced
into a guard reactor which contains a hydrogenation catalyst similar to that
in the main reactor but usually cheaper. The catalyst s hould have
wide pores to avoid plugging due to metal deposition. In the reactor,
organo-metalic compounds are hydrogenated and metal is deposited. Salts
from crude desalters are also removed here. Due to the fast deactivation of
this catalyst, usually two reactors are used and the catalyst is cha nged in
one of them w hile the other reactor is still online. The catalyst in the
guard reactor contains 8% of the total catalyst used i n the process. Desul-
phurization, denitrification and hydrodemet allizat ion reactions require
severe conditions. Three to four reactors are usually used with diff erent
combinations of catalysts to achieve desired objectives. In some units there
is a provision for online catalyst replacement in the guard reactor
(Parakash, 2003).
The stream leaving the guard reactor is quenched with cold recycle
hydrogen and introduced to the first of the three fixed bed reactors. The
main reactions of hydrodemetallization, hydrodesulphurization, denitro-
genation and aromatic hydrogenation take place in the reactors. The flow
diagram also contains high and low pressure separators, recycled hydrogen
stream with online amine treatment and purge. The liquid stream from the
separators are send to a fractionator to produce naphtha, diesel and low
sulphur fuel oil (LSFO).
The ARDS unit reactor temperature is increased at the end of the run
(EOR) to burn off any deposited carbon; where thermal cracking occurs at
these temperatures. It is possible to use the same unit as a hydrocracker by
switching the catalyst to a bifunctional type in which hydrotreating and
hydrocracking take place as explained under hydrocracking. Typical ARDS
feed and products properties are given in Table 7.6, and typical ARDS
yields are given in Table 7.7 (Parakash, 2003).
Table 7.6 Typical ARDS feed and product properties
Feed Naphtha Diesel LSFO
TBP cut point (
F) 680 C
5
–320 320–680 680
API gravity 13.2 52.5 33.5 22. 7
Sulphur (wt%) 4.2 0.1 0.05 0.5
Nitrogen (wt%) 0.26 – 0.02 0.13
Metal (Ni þ V) (wppm) 75–90 – – 28
Hydroconversion 169