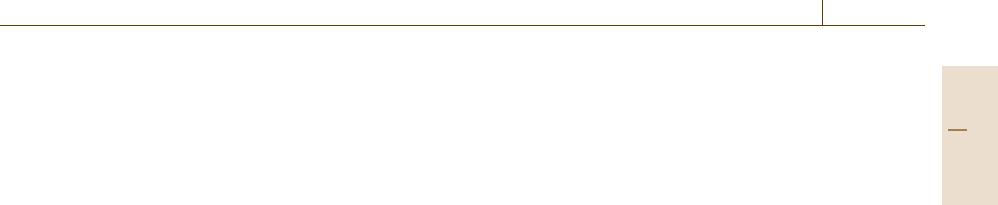
Mechanical Properties 7.1 Elasticity 341
being put into tension, the rest being put into compres-
sion. He assigned the neutral axis to one-half the height
of the beam and used this assumption to correctly solve
the force distribution in the cantilever beam. Young fur-
ther developed Hooke’s law in 1807 by introducing the
idea of a modulus of elasticity [7.8,9]. Young’s modulus
was not expressed simply as a proportionality constant
between tensile stress and tensile strain. Instead, he de-
fined the modulus as the relative diminution of the length
of a solid at the base of a long column of the solid. Nev-
ertheless, his contribution was used in the development
of general equations of the theory of elasticity.
The first attempt to develop general equations of
elastic equilibrium was by Navier, whose model was
based on central-force interactions between molecules
of a solid [7.10]. He developed a set of differen-
tial equations that could be used to calculate internal
displacements in an isotropic body. The form of the
equations was correct, but because of an oversimplifica-
tion of the force law, the equations contained only one
elastic constant.
Stimulated by the work of Navier, Cauchy in 1822
developed a theory of elasticity that contained two elas-
tic constants and is essentially the one we use today
for isotropic solids (presented to the French Academy
of Sciences on Sept. 30, 1822; Cauchy published the
work in his Excercices de mathématique, 1827 and
1828. See footnote 32 in the first chapter of [7.3]). For
nonisotropic solids, many more elastic constants are
needed, and for a long time an argument raged over
whether the number of constants for the most general
type of anisotropic material should be 15 or 21. The
controversy was settled by experiments that were car-
ried out on single crystals with pronounced anisotropy,
which showed that 21 is the correct number of constants
in the most anisotropic elastic case. This number is also
supported by crystal symmetry theory.
Once the theory of elasticity was completely devel-
oped, equations could then be derived for experimental
measurement of the elastic constants. This has now
been done quite generally so that the techniques that
have been developed have a good scientific basis in the
theory of elasticity. Elastic constants can be measured
statically (tension, compression, torsion or flexure), or
dynamically through the study of vibrating bars, or by
measuring the velocity of sound through the material.
Most of these measurements are made on materials that
are isotropic, so that only two constants are determined;
however, with the development of composite materials
for structural members, isotropy is lost and other con-
stants have to be considered.
7.1.2 Definition of Stress and Strain,
and Relationships Between Them
The theory of linear elasticity begins by defining stress
and strain [7.1, 3, 4]. Stress gives the intensity of the
mechanical forces that pass through the body, whereas
strain gives the relative displacement of points within
the body. In the theory of linear elasticity, stress and
strain are related by the elastic constants, which are ma-
terial properties. In this section we define and discuss
stress and strain and show how they are related through
the elastic constants. It is these elastic constants that
must be determined in order to evaluate stress distribu-
tions in structural components.
Stresses
When a body is under load by external forces, internal
forces are set up between different parts of the body.
The intensities of these forces are usually described by
the force per unit area on the test surface through which
they act. One can imagine cutting a small test surface
within a material and replacing the material on one side
of the surface by forces that would maintain the posi-
tion of the surface in exactly the same position as it was
before the cut was made. As the size of the test surface
is diminished to zero, the sum of the forces on the sur-
face divided by the area of the surface is defined as the
magnitude of the stress on the surface. The direction of
the stress is given by the direction of the force on the
surface and need not be normal to the surface.
From the definition of stress, it is clear that the stress
on a surface will vary with orientation and position of the
surface within the solid. It is also usual to break down
the components of stress into stresses normal and paral-
lel to the surface. The stresses parallel to the surface are
called shear stresses. Because stress depends on both the
orientation of the surface, and the direction of the forces
on the surface, the symbol indicating stress will have two
subscripts attached to it, the first indicating the surface
normal, the second indicating the direction of the forces
on the surface. Consider a Cartesian coordinate system
with three mutually perpendicular axes, x
1
, x
2
,andx
3
.
Atestsurfacenormaltothe x
1
-axiswillhavestresses,σ
11
,
σ
12
,andσ
13
, where σ is the symbol for stress. The force
indicated by the stress σ
11
is on the x
1
-surface,and its ori-
entation is parallel to the x
1
-axis. The stress σ
11
is either
a tensile stress (positive sign by convention), or a com-
pressive stress (negative sign). The stresses, σ
12
and σ
13
,
are shear stresses: σ
12
beingonthex
1
-surface and ori-
entedinthex
2
-direction; σ
13
being on the x
1
-surface and
oriented in the x
3
-direction.
Part C 7.1