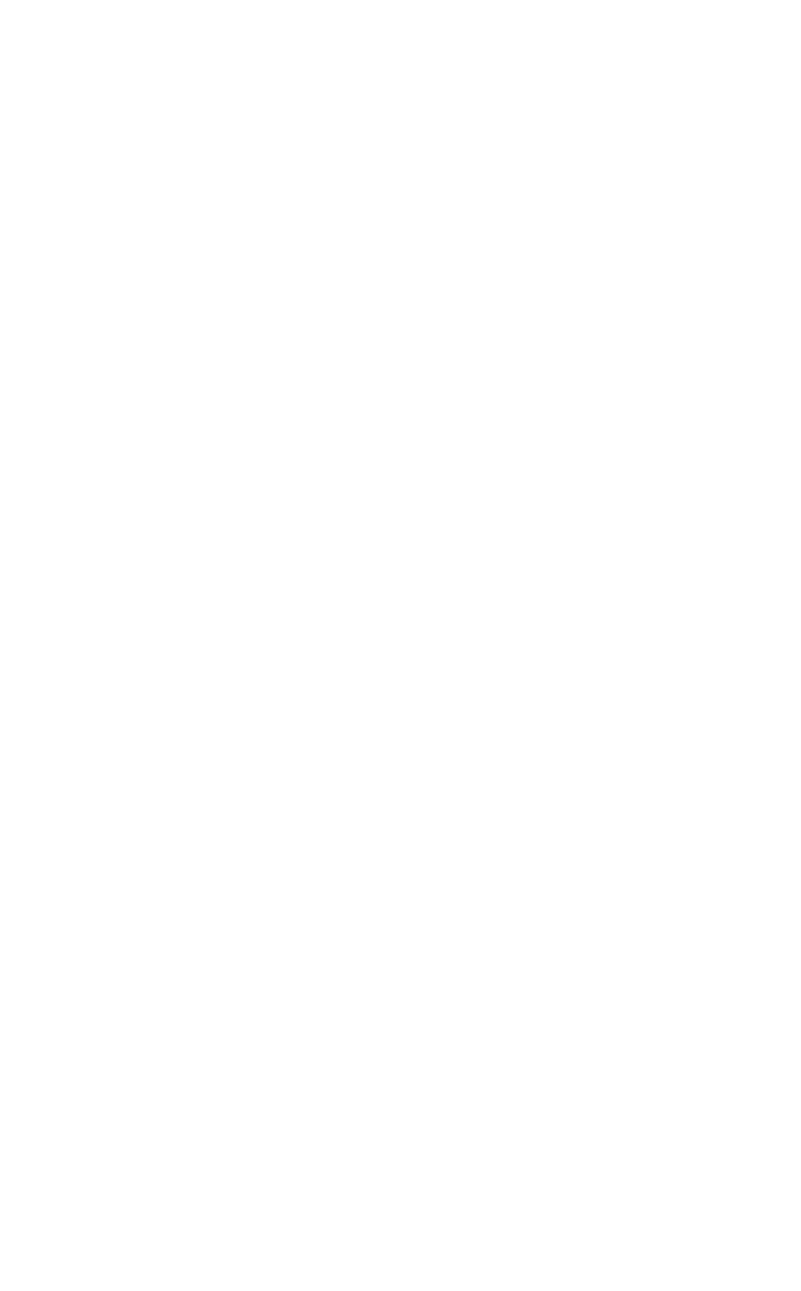
100 / Cold and Hot Forging: Fundamentals and Applications
solved by the following variational equation [Li
et al., 2001],
˙
dp(v,p) ⳱ ¯rd ¯edV Ⳮ pd ˙e dV Ⳮ ˙edp
vv
冮冮冮
VV V
ⳮ F dudS ⳱ 0 (Eq 9.39)
ii
冮
S
F
where p is the pressure.
Equations 9.37 to 9.39 can be converted into
a set of algebraic equations by utilizing the stan-
dard FEM discretization procedures. Due to the
nonlinearity involved in the material properties
and frictional contact conditions, this solution is
obtained iteratively.
The temperature distribution of the workpiece
and/or dies can be obtained readily by solving
the energy balance equation rewritten by using
the weighted residual method as [Li et al., 2001]:
˙
kT dTdVⳭ qcTdTdV
ij ij
冮冮
VV
˙
ⳮ ␣ ¯r ¯edTdV ⳱ q dTdS (Eq 9.40)
n
冮冮
VS
where k is the thermal conductivity, T the tem-
perature, q the density, c the specific heat, ␣ a
fraction of deformation energy that converts into
heat, and q
n
the heat flux normal to the boundary,
including heat loss to the environment and fric-
tion heat between two contacting objects. Using
FEM discretization, Eq 9.40 can also be con-
verted to a system of algebraic equations and
solved by a standard method. In practice, the
solutions of mechanical and thermal problems
are coupled in a staggered manner. After the
nodal velocities are solved at a given step, the
deformed configuration can be obtained by up-
dating the nodal coordinates [Li et al., 2001].
9.4.2 Computer Implementation of the
Finite Element Method
Computer implementation of the basic steps
in a standard finite element analysis consists of
three distinct units, viz. the preprocessor, pro-
cessor, and the postprocessor.
Preprocessor. This operation precedes the
analysis operation. It takes in minimal infor-
mation from the user (input) to generate all nec-
essary problem parameters (output) required for
a finite element analysis.
The input to the preprocessor includes infor-
mation on the solid model, discretization re-
quirements, material identification and parame-
ters, and boundary conditions; whereas the
output includes coordinates for nodes, element
connectivity and element information, values of
material parameters for each element, and
boundary loading conditions on each node.
In the preprocessing stage, a continuum is di-
vided into a finite number of subregions (or ele-
ments) of simple geometry (triangles, rectan-
gles, tetrahedral, etc.). Key points are then
selected on elements to serve as nodes where
problem equations such as equilibrium and com-
patibility are satisfied.
In general, preprocessing involves the follow-
ing steps to run a successful simulation using a
commercial FE package:
1. Select the appropriate geometry/section for
simulation based on the symmetry of the
component to be analyzed.
2. Assign workpiece material properties in the
form of the flow stress curves. These may be
user defined or selected from the database
provided in the FE package.
3. Mesh the workpiece using mesh density win-
dows, if necessary, to refine mesh in critical
areas.
4. Define the boundary conditions (velocity,
pressure, force, etc.). Specify the movement
and direction for the dies. Specify the inter-
face boundary and friction conditions. This
prevents penetration of the dies into the
workpiece and also affects the metal flow de-
pending on the friction specified. In massive
forming processes such as forging, extrusion,
etc., the shear friction factor “m” is specified.
Note: If die stress analysis or thermal analysis
is required, one would need to mesh the dies and
specify the material properties for them. Also
die and workpiece temperatures and interface
heat transfer coefficients would need to be spec-
ified. Material data at elevated temperatures
would be required for the tools and the work-
piece. The die stress analysis procedure is de-
scribed in Chapter 16 on process modeling in
impression die forging.
Processor. This is the main operation in the
analysis. The output from the preprocessor (in-
cluding nodal coordinates, element connectivity,
material parameters, and boundary/loading con-
ditions) serves as the input to this module. It
establishes a set of algebraic equations that are
to be solved, from the governing equations of
the boundary value problem. The governing