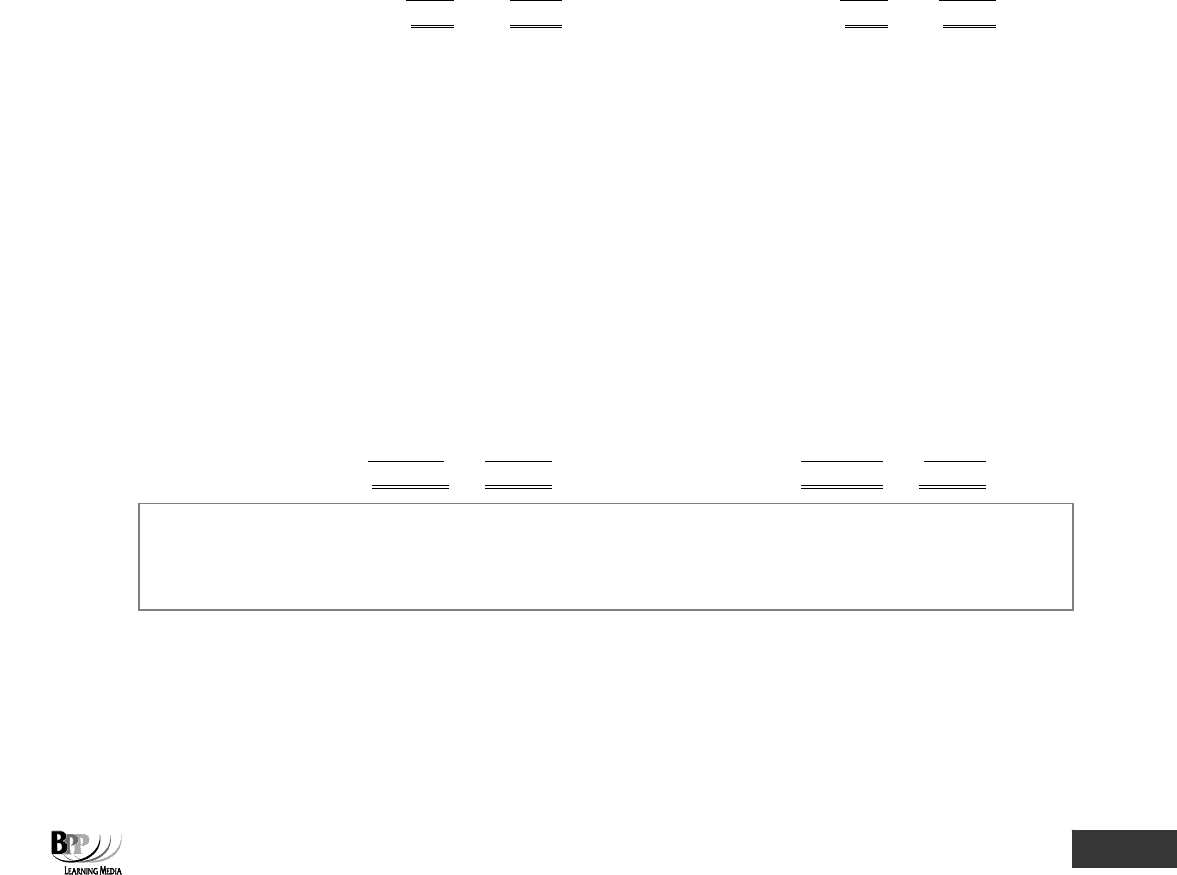
Part D Costing and accounting systems ⏐ 12: Process costing
265
(ii) Some of the material input might evaporate or get spilled or damaged, so there would be losses.
So we record the loss units and the cost of the loss.
(iii) At the end of a period, some units of input might be in the process of being turned into finished
units so would be work in progress (WIP). We record the units of WIP and the cost of these units.
The quantity columns on each side of the account should total to the same amount. Why? Well think about it. If we put
100 kgs of material in to a process (which we record on the left hand side of the account) we should know what has
happened to those 100 kgs. Some would be losses maybe, some would be WIP, some would be finished units, but the
total should be 100 kgs.
Likewise the cost of the inputs to the process during a period (ie the total of the costs recorded on the left hand side of
the account) is the cost of the outputs of the process. If we have recorded material, labour and overhead costs totalling
$1,000 and at the end of the process we have 100 finished units (and no losses or WIP), then that output cost $1,000.
Here’s a very simple example of a process account.
PROCESS ACCOUNT
Units
$
Units
$
Material
1,000
11,000
Closing WIP
200
2,000
Labour
4,000
Finished units
800
16,000
Overhead
3,000
1,000
18,000
1,000
18,000
As you can see, the quantity columns on each side balance (ie they are the same), as do the monetary columns. (Don’t
worry at this stage about how the costs are split between WIP and finished units.)
2.2 Example: basics of process costing
Suppose that Purr and Miaow Co make squeaky toys for cats. Production of the toys involves two processes, shaping
and colouring. During the year to 31 March 20X3, 1,000,000 units of material worth $500,000 were input to the first
process, shaping. Direct labour costs of $200,000 and production overhead costs of $200,000 were also incurred in
connection with the shaping process. There were no opening or closing inventories in the shaping department. The
process account for shaping for the year ended 31 March 20X3 is as follows.
PROCESS 1 (SHAPING) ACCOUNT
Units $ Units $
Direct materials 1,000,000 500,000 Output to Process 2 1,000,000 900,000
Direct labour 200,000
Production overheads
200,000
1,000,000
900,000
1,000,000
900,000
When preparing process accounts, balance off the quantity columns (ie ensure they total to the same amount on both
sides) before attempting to complete the monetary value columns since they will help you to check that you have missed
nothing out. This becomes increasingly important as more complications are introduced into questions.
When using process costing, if a series of separate processes is needed to manufacture the finished product, the
output of one process becomes the input to the next until the final output is made in the final process. In our example,
all output from shaping was transferred to the second process, colouring, during the year to 31 March 20X3. An
additional 500,000 units of material, costing $300,000, were input to the colouring process. Direct labour costs of
$150,000 and production overhead costs of $150,000 were also incurred. There were no opening or closing inventories
in the colouring department. The process account for colouring for the year ended 31 March 20X3 is as follows.
Assessment
focus point
286433 www.ebooks2000.blogspot.com