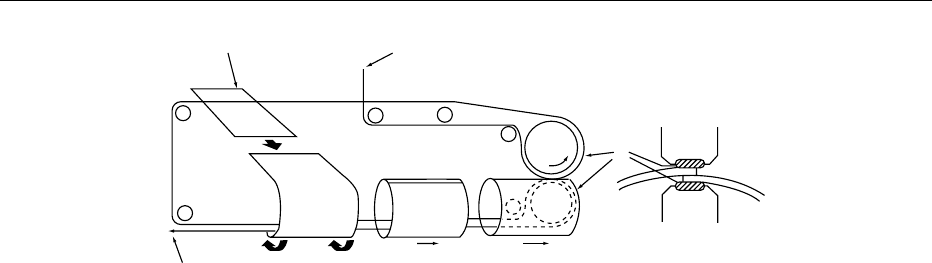
0033 Internal lacquers must be inert, must provide a
good barrier, and must also have a good mechanical
resistance, as well as thermal resistance if the product
is to be thermally processed. The lacquer must
comply with the regulations for materials intended
for food contact, i.e., only approved substances that
had sustained successful migration or extraction tests
and that do not impart any flavor to the contents,
may be used.
0034 The barrier provided by the lacquer depends on its
chemical composition and on its porosity (which
must be as low as possible) and which in turn depends
on the thickness of the lacquer. Control of the amount
of lacquer applied, usually measured in terms of the
mass of dry film per area of metal sheet, is very
important since a thin layer will not cover the surface
completely, and a layer that is too thick will lead to
brittleness, lack of flexibility, and poor adhesion, as
well as being uneconomical.
0035 The lacquer must be resistant to mechanical solici-
tations during can and ends manufacturing oper-
ations, as in the case of three-piece cans and most
DRD two-piece cans that are produced from a pre-
coated metal sheet. Flexibility and adhesion are also
important characteristics of lacquers, as during
retorting, the can tends to deform, due to a pressure
imbalance.
0036 The lacquer is usually applied by roller coating to
the metal in the flat form sheet or coil before fabrica-
tion. Spraying is used for coating the internal surface
of DWI two-piece cans that cannot be produced
from prelacquered sheets, owing to the considerable
amount of metal deformation and surface disruption
occurring during ironing operations. Powder coating,
where the resin is applied dry in the form of a fine
powder, usually under the direction of an electrostatic
field, is used for the protection of welded side seams
(internal side), where heavy coatings are required.
A postfabrication repair lacquering is applied to
cans used to pack products with very demanding
protection requirements, to compensate for natural
application imperfections and layer damage during
can fabrication.
0037After application, the lacquer must be dried by
solvent removal, oxidation, and/or heat polymeriza-
tion. This process is usually performed in a forced
convection oven using hot air up to 210
C for up to
15 min. Recent developments include resin formula-
tions, which need lower temperatures and shorter
curing times, often through the use of ultraviolet
radiation (these ultraviolet-curing resins are virtually
solvent-free).
0038The more common chemical families of protective
lacquers are the phenols, epoxy, polyesters, and vinyl.
The resins are rarely used pure. They are modified
and/or combined with other resins and additives that
confer specific characteristics. Table 3 summarizes
the major lacquers’ characteristics and applications.
0039Phenolic resins are produced by the action of for-
maldehyde on phenol and are characterized by having
a high degree of reticulation enhancing barrier, hard-
ness and chemical inertia, but limited flexibility due
to the presence of the bulge phenolic ring.
0040Epoxy resins are produced by polymerization of
bisphenol A with glycerol epichlorohydrine. Epoxy
is highly reactive, allowing for combination with
other resins, and it has a good chemical resistance. It
is very flexible because of its linear structure, without
reticulation, and it is often combined with phenolics
giving the epoxy-phenolic family, one of the most
widely used families of resins for lacquering. A
three-dimensional structure is formed during curing,
either by straight blending of a solid epoxy resin with
a solid phenolic resin or by condensation of a mixture
of two resins in appropriate solvents. Epoxy-phenolic
lacquer combines the good adhesion properties of the
epoxy resin with the high chemical resistance proper-
ties of the phenolic resin. The balanced properties of
12
5
3
33
4
3
fig0012 Figure 12 Welding side seam of a three-piece can: 1, blank feed; 2, wire fed; 3, welding rolls (electrodes); 4, copper wire (welding
contact); 5, used wire. From Bakker M and Eckroth D (1986) The Wiley Encyclopedia of Packaging Technology. New York: John Wiley, with
permission.
CANNING/Cans and their Manufacture 831