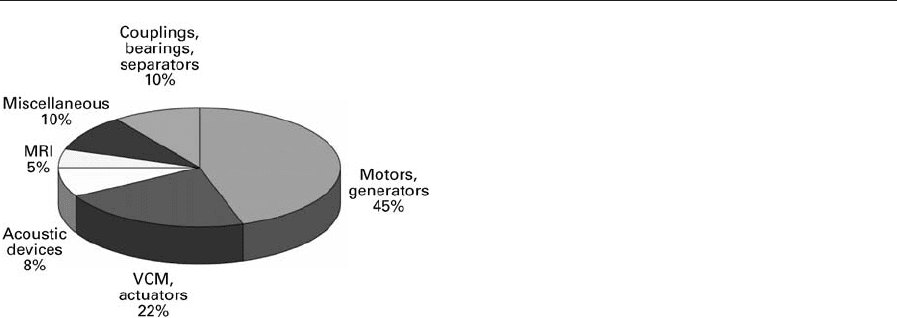
the electric motor is ubiquitous and consumes 40–
45% of all electrical energy generated. Most of this
energy is consumed by large industrial electric drives,
but nonetheless an increasing proportion is consumed
by small electric motors used in domestic appliances,
for example, in refrigerators which operate continu-
ously. Regardless of the motor application there is
pressure to improve electric motor efficiency as peo-
ple and governments become more aware of the con-
sequences of global warming, due to the emission of
the greenhouse gas, CO
2
, from large coal-fired power
stations.
Electric motors are present in many household
products (for the purposes of this section ‘‘domestic’’
is defined as any product that is found in the home).
Products containing electric motors can be grouped
according to their domestic application area and
a list, by no means exhaustive, includes: laundry—
washing machine and clothes dryer; kitchen–dish-
washer, microwave oven, fan-forced convection
oven, refrigerator, food blender, electric knife, gar-
bage disposal unit, mixmaster, etc; bathroom—hair-
dryer, electric tooth brush, hair clippers, electric
shaver, etc; entertainment—videorecorder, CD play-
er, hi-fi system, camcorder, walkman, camera, etc;
home study—personal computer, printer, photocop-
ier, facsimile machine, etc; general household—
vacuum cleaner, exhaust fans, ceiling fans, swimming
pool and spa pumps, air-conditioner, fans in gas and
electric heating systems, etc; and garage—electric
drills, saws, routers and grinders, electric screwdriver,
electric lawn mower, edge clipper, garden shears, ga-
rage door/gate opener, etc.
Some products or appliances may contain as many
as four or five individual motors, for example, a
camcorder, and where there is a motor there is likely
to be power and control electronics, for example, a
switch-mode power supply that incorporates magnetic
components. Not included in domestic appliances is
the family automobile, which may contain up to 40 or
even more electric motors. The use of magnetic ma-
terials is not just confined to motors, as they are used
in speakers in televisions and hi-fi systems, holding
devices, water-meters, watt-hour meters and fluores-
cent lighting ballasts.
1. Motor Technology
A conventional brushed d.c. electric motor can be
viewed as having three key components: a field sys-
tem, which usually consists of a winding around teeth
on a stator yoke; an armature, consisting of a series
of coils wound in slots on a rotor; and a commutator,
for making the electrical connection to the armature
coils (Hamdi 1994). The stator and armature lami-
nations are made from a soft magnetic material, usu-
ally low-loss silicon steel laminations, and are part of
the magnetic circuit which carries and guides the
magnetic flux in the machine. In a permanent magnet
machine the field system uses permanent magnets
rather than producing the field by passing current
through coils.
The replacement of the wound field system by per-
manent magnets results in a significant improvement
in motor efficiency, as no electrical energy is used in
field production. The motor can then be turned in-
side-out with the field magnets being attached to the
rotor, a multiphase armature winding on the stator,
and the commutator replaced by electronic switching
devices which switch the current through the stator
windings (see Fig. 2). This configuration has the ad-
vantage of improved thermal performance, as im-
proved cooling is obtained by having the high-current
stator winding in good thermal contact with the mo-
tor case. Motors of this type are known as permanent
magnet brushless d.c. motors or just brushless d.c.
motors (Hughes 1993, Gieras and Wing 1997).
Modern permanent magnet brushless d.c. motors
have the advantages of high torque or power per unit
volume, improved efficiency, better dynamic response
(due to the low inertia of the rotor), reduced volume,
reduced weight, mechanical simplicity and reliability
(as there are no brushes or commutator), and quiet
operation (Hanitsch 1989). These improvements did
not happen overnight, but are the result of advances
in materials science over the past 30 years, particu-
larly the development of rare-earth permanent mag-
nets (Sm
2
Co
17
and Nd
2
Fe
14
B) (see Rare Earth
Magnets: Materials), and new soft magnetic materi-
als, such as amorphous or glassy metals (see Amor-
phous and Nanocrystalline Materials). In parallel with
these developments in materials science there have
been major advances in magnetic circuit design, using
computational methods based on finite-element
techniques, and a revolution in semiconductors, re-
sulting in low-cost microprocessors and digital signal
Figure 1
Expected application of Nd
2
Fe
14
B in Europe for 1995
(Krebs 1995).
470
Magnetic Materials: Domestic Applications