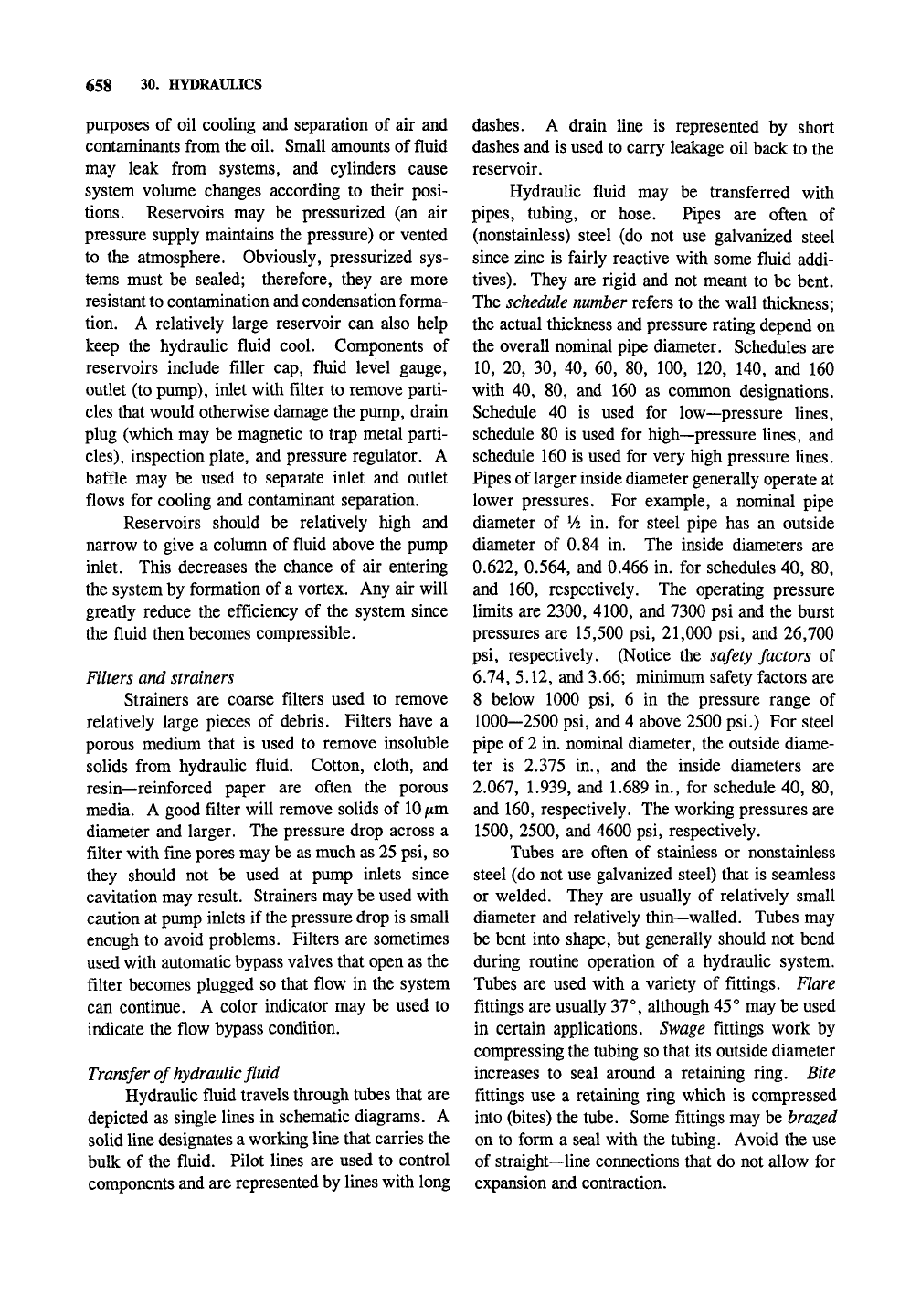
658 30. HYDRAULICS
purposes of oil cooling and separation of air and
contaminants from the oil. Small amounts of fluid
may leak from systems, and cylinders cause
system volume changes according to their posi-
tions.
Reservoirs may be pressurized (an air
pressure supply maintains the pressure) or vented
to the atmosphere. Obviously, pressurized sys-
tems must be sealed; therefore, they are more
resistant to contamination and condensation forma-
tion. A relatively large reservoir can also help
keep the hydraulic fluid cool. Components of
reservoirs include filler cap, fluid level gauge,
outlet (to pump), inlet with filter to remove parti-
cles that would otherwise damage the pump, drain
plug (which may be magnetic to trap metal parti-
cles),
inspection plate, and pressure regulator. A
baffle may be used to separate inlet and outlet
flows for cooling and contaminant separation.
Reservoirs should be relatively high and
narrow to give a column of fluid above the pump
inlet. This decreases the chance of air entering
the system by formation of a vortex. Any air will
greatly reduce the efficiency of the system since
the fluid then becomes compressible.
Filters and strainers
Strainers are coarse filters used to remove
relatively large pieces of debris. Filters have a
porous medium that is used to remove insoluble
solids from hydraulic fluid. Cotton, cloth, and
resin—reinforced paper are often the porous
media. A good filter will remove solids of
10
fim
diameter and larger. The pressure drop across a
filter with fine pores may be as much as 25 psi, so
they should not be used at pump inlets since
cavitation may result. Strainers may be used with
caution at pump inlets if the pressure drop is small
enough to avoid problems. Filters are sometimes
used with automatic bypass valves that open as the
filter becomes plugged so that flow in the system
can continue. A color indicator may be used to
indicate the flow bypass condition.
Transfer of hydraulic fluid
Hydraulic fluid travels through tubes that are
depicted as single lines in schematic diagrams. A
solid line designates a working line that carries the
bulk of the fluid. Pilot lines are used to control
components and are represented by lines with long
dashes. A drain line is represented by short
dashes and is used to carry leakage oil back to the
reservoir.
Hydraulic fluid may be transferred with
pipes,
tubing, or hose. Pipes are often of
(nonstainless) steel (do not use galvanized steel
since zinc is fairly reactive with some fluid addi-
tives).
They are rigid and not meant to be bent.
The schedule number refers to the wall thickness;
the actual thickness and pressure rating depend on
the overall nominal pipe diameter. Schedules are
10,
20, 30, 40, 60, 80, 100, 120, 140, and 160
with 40, 80, and 160 as common designations.
Schedule 40 is used for low—pressure lines,
schedule 80 is used for high—pressure lines, and
schedule 160 is used for very high pressure lines.
Pipes of larger inside diameter generally operate at
lower pressures. For example, a nominal pipe
diameter of Vi in. for steel pipe has an outside
diameter of 0.84 in. The inside diameters are
0.622, 0.564, and 0.466 in. for schedules 40, 80,
and 160, respectively. The operating pressure
limits are 2300, 4100, and 7300 psi and the burst
pressures are 15,500 psi, 21,000 psi, and 26,700
psi,
respectively. (Notice the safety factors of
6.74, 5.12, and 3.66; minimum safety factors are
8 below 1000 psi, 6 in the pressure range of
1000—2500 psi, and 4 above 2500 psi.) For steel
pipe of 2 in. nominal diameter, the outside diame-
ter is 2.375 in., and the inside diameters are
2.067,
1.939,
and 1.689 in., for schedule 40, 80,
and 160, respectively. The working pressures are
1500,
2500, and 4600 psi, respectively.
Tubes are often of stainless or nonstainless
steel (do not use galvanized steel) that is seamless
or welded. They are usually of relatively small
diameter and relatively thin—walled. Tubes may
be bent into shape, but generally should not bend
during routine operation of a hydraulic system.
Tubes are used with a variety of fittings. Flare
fittings are usually 37°, although 45° may be used
in certain applications. Swage fittings work by
compressing the tubing so that its outside diameter
increases to seal around a retaining ring. Bite
fittings use a retaining ring which is compressed
into (bites) the tube. Some fittings may be brazed
on to form a seal with the tubing. Avoid the use
of straight—line connections that do not allow for
expansion and contraction.