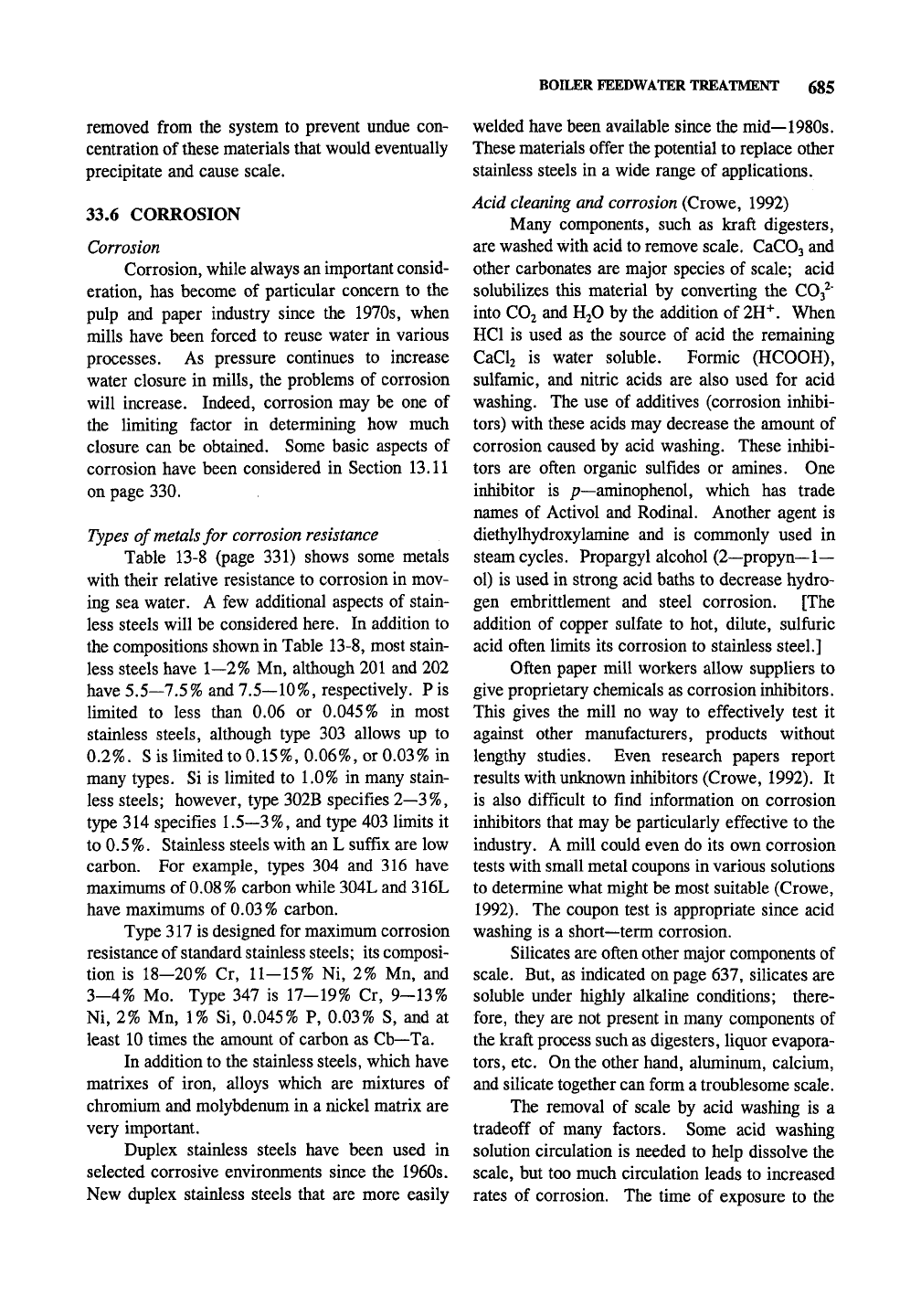
BOILER FEEDWATER TREATMENT 685
removed from the system to prevent undue con-
centration of these materials that would eventually
precipitate and cause scale.
33.6 CORROSION
Corrosion
Corrosion, while always an important consid-
eration, has become of particular concern to the
pulp and paper industry since the 1970s, when
mills have been forced to reuse water in various
processes. As pressure continues to increase
water closure in mills, the problems of corrosion
will increase. Indeed, corrosion may be one of
the limiting factor in determining how much
closure can be obtained. Some basic aspects of
corrosion have been considered in Section 13.11
on page 330.
Types of metals for corrosion resistance
Table 13-8 (page 331) shows some metals
with their relative resistance to corrosion in mov-
ing sea water. A few additional aspects of stain-
less steels will be considered here. In addition to
the compositions shown in Table 13-8, most stain-
less steels have 1—2% Mn, although 201 and 202
have 5.5—7.5% and 7.5—10%, respectively. P is
limited to less than 0.06 or 0.045% in most
stainless steels, although type 303 allows up to
0.2%. S is limited to 0.15%, 0.06%, or 0.03% in
many types. Si is limited to 1.0% in many stain-
less steels; however, type 302B specifies
2—3%,
type 314 specifies 1.5—3%, and type 403 limits it
to 0.5%. Stainless steels with an L suffix are low
carbon. For example, types 304 and 316 have
maximums of
0.08%
carbon while 304L and 316L
have maximums of 0.03% carbon.
Type 317 is designed for maximum corrosion
resistance of standard stainless steels; its composi-
tion is 18—20% Cr, 11—15% Ni, 2% Mn, and
3-4% Mo. Type 347 is 17-19% Cr, 9-13%
Ni,
2% Mn, 1% Si, 0.045% P, 0.03% S, and at
least 10 times the amount of carbon as Cb—Ta.
In addition to the stainless steels, which have
matrixes of iron, alloys which are mixtures of
chromium and molybdenum in a nickel matrix are
very important.
Duplex stainless steels have been used in
selected corrosive environments since the 1960s.
New duplex stainless steels that are more easily
welded have been available since the mid—1980s.
These materials offer the potential to replace other
stainless steels in a wide range of applications.
Acid
cleaning
and
corrosion
(Crowe, 1992)
Many components, such as kraft digesters,
are washed with acid to remove scale. CaCOj and
other carbonates are major species of scale; acid
solubilizes this material by converting the COj^'
into CO2 and HjO by the addition of 2H+. When
HCl is used as the source of acid the remaining
CaCl2 is water soluble. Formic (HCOOH),
sulfamic, and nitric acids are also used for acid
washing. The use of additives (corrosion inhibi-
tors) with these acids may decrease the amount of
corrosion caused by acid washing. These inhibi-
tors are often organic sulfides or amines. One
inhibitor is /?-aminophenol, which has trade
names of Activol and Rodinal. Another agent is
diethylhydroxylamine and is commonly used in
steam cycles. Propargyl alcohol (2—propyn—1—
ol) is used in strong acid baths to decrease hydro-
gen embrittlement and steel corrosion. [The
addition of copper sulfate to hot, dilute, sulfuric
acid often limits its corrosion to stainless steel.]
Often paper mill workers allow suppliers to
give proprietary chemicals as corrosion inhibitors.
This gives the mill no way to effectively test it
against other manufacturers, products without
lengthy studies. Even research papers report
results with unknown inhibitors (Crowe, 1992). It
is also difficult to find information on corrosion
inhibitors that may be particularly effective to the
industry. A mill could even do its own corrosion
tests with small metal coupons in various solutions
to determine what might be most suitable (Crowe,
1992).
The coupon test is appropriate since acid
washing is a short—term corrosion.
Silicates are often other major components of
scale. But, as indicated on page 637, silicates are
soluble under highly alkaline conditions; there-
fore,
they are not present in many components of
the kraft process such as digesters, liquor evapora-
tors,
etc. On the other hand, aluminum, calcium,
and silicate together can form a troublesome scale.
The removal of scale by acid washing is a
tradeoff of many factors. Some acid washing
solution circulation is needed to help dissolve the
scale, but too much circulation leads to increased
rates of corrosion. The time of exposure to the