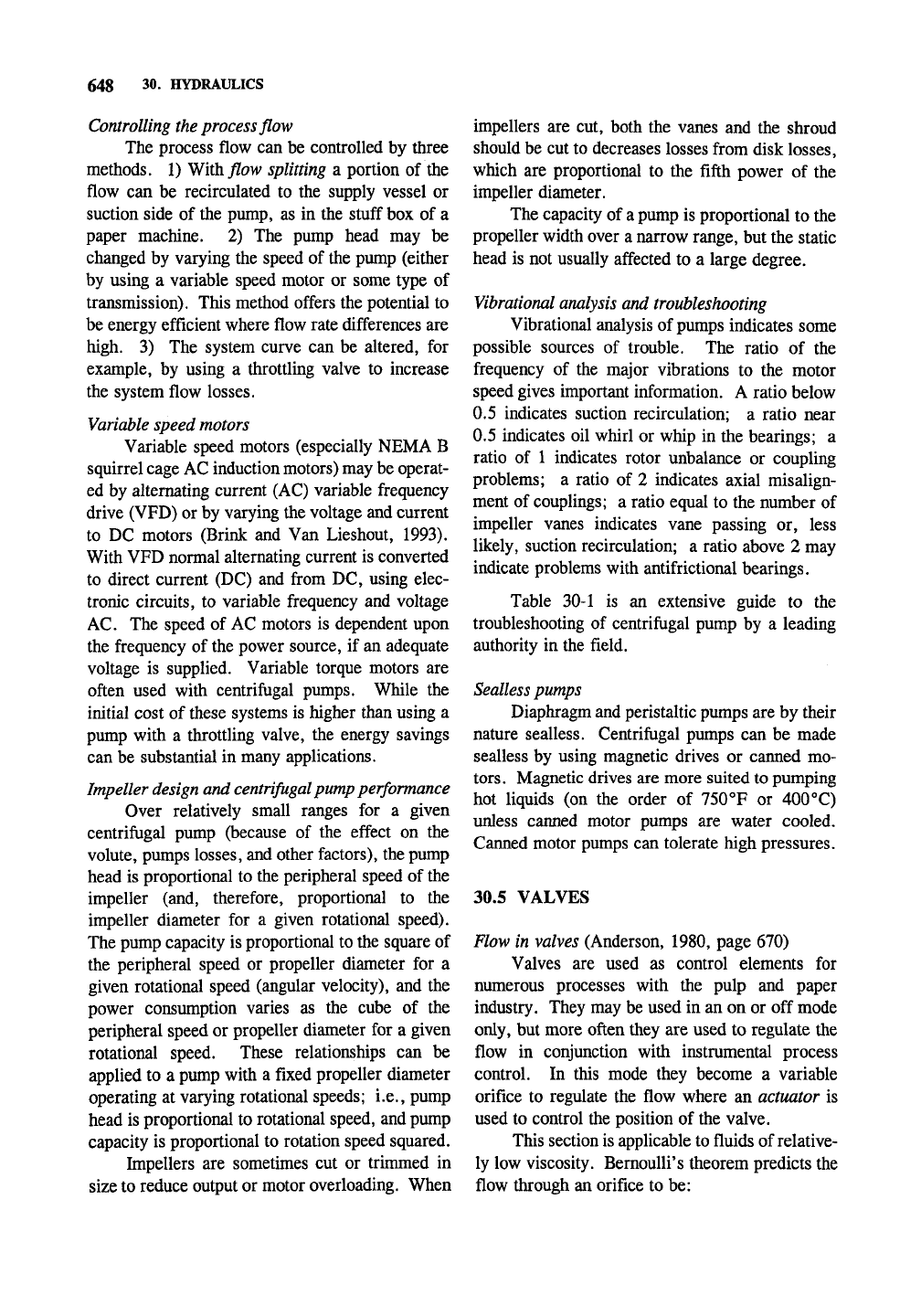
648 30. HYDRAULICS
Controlling
the process flow
The process flow can be controlled by three
methods. 1) With flow splitting a portion of the
flow can be recirculated to the supply vessel or
suction side of the pump, as in the stuff box of a
paper machine. 2) The pump head may be
changed by varying the speed of the pump (either
by using a variable speed motor or some type of
transmission). This method offers the potential to
be energy efficient where flow rate differences are
high. 3) The system curve can be altered, for
example, by using a throttling valve to increase
the system flow losses.
Variable
speed motors
Variable speed motors (especially NEMA B
squirrel cage AC induction motors) may be operat-
ed by alternating current (AC) variable frequency
drive (VFD) or by varying the voltage and current
to DC motors (Brink and Van Lieshout, 1993).
With VFD normal alternating current is converted
to direct current (DC) and from DC, using elec-
tronic circuits, to variable frequency and voltage
AC.
The speed of AC motors is dependent upon
the frequency of the power source, if an adequate
voltage is supplied. Variable torque motors are
often used with centrifugal pumps. While the
initial cost of these systems is higher than using a
pump with a throttling valve, the energy savings
can be substantial in many applications.
Impeller
design
and centrifugal pump performance
Over relatively small ranges for a given
centrifugal pump (because of the effect on the
volute, pumps losses, and other factors), the pump
head is proportional to the peripheral speed of the
impeller (and, therefore, proportional to the
impeller diameter for a given rotational speed).
The pump capacity is proportional to the square of
the peripheral speed or propeller diameter for a
given rotational speed (angular velocity), and the
power consumption varies as the cube of the
peripheral speed or propeller diameter for a given
rotational speed. These relationships can be
applied to a pump with a fixed propeller diameter
operating at varying rotational speeds; i.e., pump
head is proportional to rotational speed, and pump
capacity is proportional to rotation speed squared.
Impellers are sometimes cut or trimmed in
size to reduce output or motor overloading. When
impellers are cut, both the vanes and the shroud
should be cut to decreases losses from disk losses,
which are proportional to the fifth power of the
impeller diameter.
The capacity of a pump is proportional to the
propeller width over a narrow range, but the static
head is not usually affected to a large degree.
Vibrational analysis
and troubleshooting
Vibrational analysis of pumps indicates some
possible sources of trouble. The ratio of the
frequency of the major vibrations to the motor
speed gives important information. A ratio below
0.5 indicates suction recirculation; a ratio near
0.5 indicates oil whirl or whip in the bearings; a
ratio of 1 indicates rotor unbalance or coupling
problems; a ratio of 2 indicates axial misalign-
ment of couplings; a ratio equal to the number of
impeller vanes indicates vane passing or, less
likely, suction recirculation; a ratio above 2 may
indicate problems with antifrictional bearings.
Table 30-1 is an extensive guide to the
troubleshooting of centrifugal pump by a leading
authority in the field.
Sealless
pumps
Diaphragm and peristaltic pumps are by their
nature sealless. Centrifugal pumps can be made
sealless by using magnetic drives or canned mo-
tors.
Magnetic drives are more suited to pumping
hot liquids (on the order of 750°F or 400°C)
unless canned motor pumps are water cooled.
Canned motor pumps can tolerate high pressures.
30.5 VALVES
Flow in valves (Anderson, 1980, page 670)
Valves are used as control elements for
numerous processes with the pulp and paper
industry. They may be used in an on or off mode
only, but more often they are used to regulate the
flow in conjunction with instrumental process
control. In this mode they become a variable
orifice to regulate the flow where an actuator is
used to control the position of the valve.
This section is applicable to fluids of relative-
ly low viscosity. Bernoulli's theorem predicts the
flow through an orifice to be: