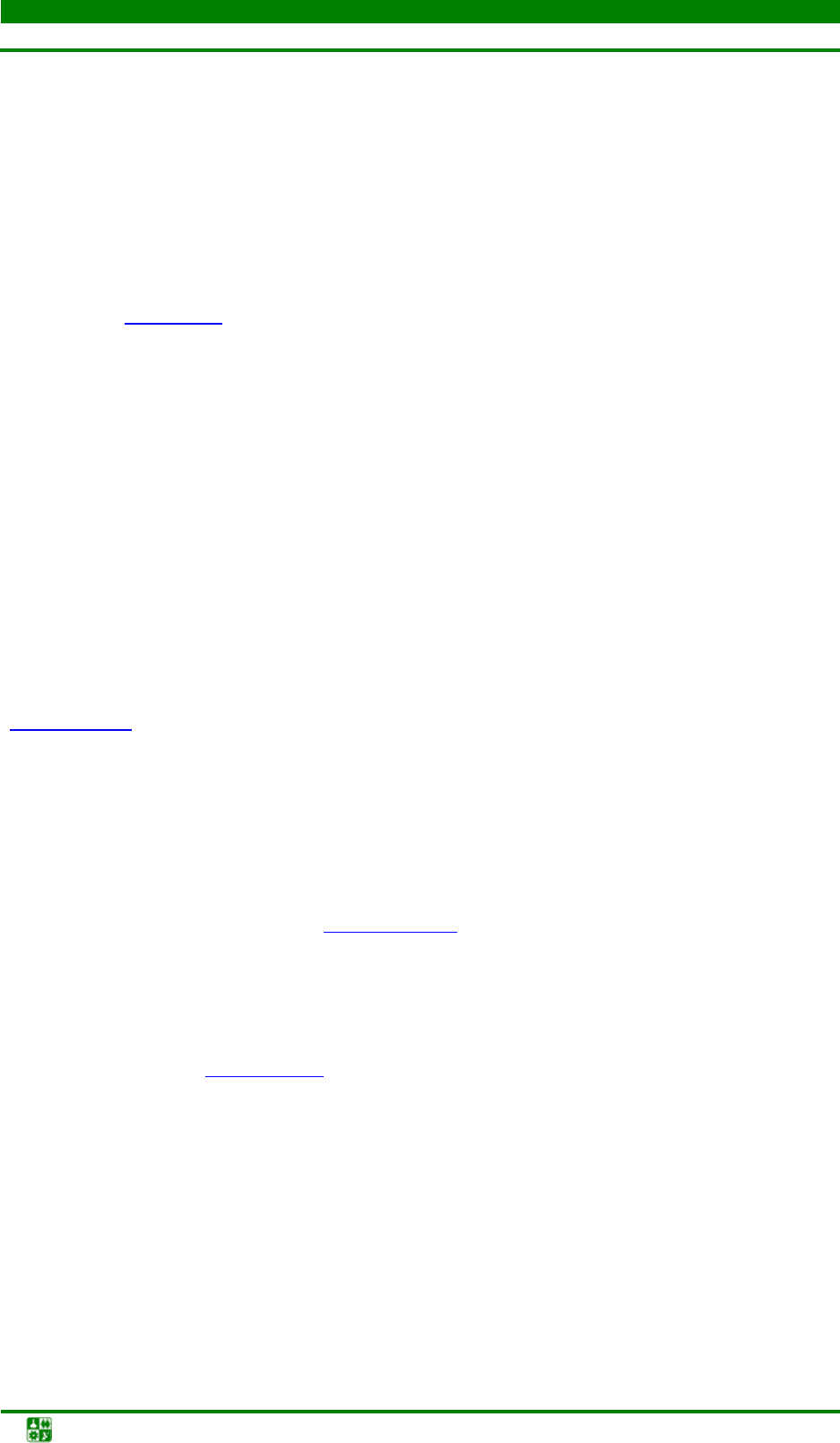
ГЛАВА 6. ТЕХНОЛОГИЯ ПОЛУЧЕНИЯ ЗАГОТОВОК ПЛАСТИЧЕСКИМ ДЕФОРМИРОВАНИЕМ
6.5. Методы получения машиностроительных профилей
Технология конструкционных материалов. Учебное пособие -173-
прессование – прессование металлов под непосредственным воздействием
давления жидкости до 2000 МПа и выше.
6
6
.
.
5
5
.
.
2
2
.
.
2
2
.
.
В
В
о
о
л
л
о
о
ч
ч
е
е
н
н
и
и
е
е
Волочение заключается в протягивании (чаще всего в холодном состоя-
нии) прокатанных или прессованных заготовок через отверстие в матрице
(волоке), поперечное сечение которой меньше поперечного сечения
заготовки (рис. 6.27
). При протягивании прутка через отверстие с силой Р
возникают силы реакции N, которые обжимают заготовку.
Степень обжатия q = (F
0
– F
1
)/F
0
(где F
0
и F
1
– площади поперечного
сечения соответственно до и после волочения), допускаемая за один проход,
зависит от обрабатываемого материала и составляет для сталей 10–19 %, для
цветных металлов − до 36 %. Чтобы не было обрывов, напряжение при воло-
чении не должно превышать 0,6 предела прочности материала заготовки. Для
получения профилей необходимых размеров производят волочение за
несколько проходов через ря
д постепенно уменьшающихся отверстий. В
результате холодной пластической деформации происходит упрочнение
(наклеп) металла. Для снятия наклепа и повышения пластичности производят
промежуточный рекристаллизационный отжиг.
Из различных сортов стали и цветных металлов волочением изготав-
ливают проволоку диаметром 0,002–10 мм, разнообразные профили
(рис. 6.27, a
), калиброванные прутки диаметром 3–150 мм, холоднотянутые
трубы диаметром до 500 мм и с толщиной стенки 0,1–10 мм достаточно
высокой точности с блестящей гладкой поверхностью. Благодаря наклепу
волочением можно повысить прочность и твердость металла.
Инструмент и оборудование для волочения. Инструментом для
волочения служит волочильная матрица (волока). Волоки могут быть
цельными, составными и роликовыми. Цельная волока 1 имеет отверстие,
состоящее из четырех зон (рис. 6.27, б
): смазочной воронки I, рабочего
конуса II, калибрующего пояска III и выходного конуса IV. Угол рабочего
конуса зависит от деформируемого материала и составляет 6–12°. Ширина
калибрующего пояска обычно 2–10 мм. Волока изготавливается из инстру-
ментальных сталей, твердых сплавов и технических алмазов и устанавли-
вается в обойме 2 (рис. 6.27, б
).
Волочение производится на волочильных станах, в которых заготовки с
помощью тянущего устройства протягиваются через отверстие матрицы.
Различают волочильные станы периодического действия с прямо-
линейным движением тянущего устройства (чаще всего цепные) и станы
непрерывного действия (барабанные).
Скорость волочения достигает 10 м/с, а для тонкой проволоки – 40 м/с.
Волочение прутков, проволоки и труб.
Основу технологического
процесса составляет маршрут волочения, который показывает последователь-
ное изменение размеров заготовки по проходам. Степень обжатия для