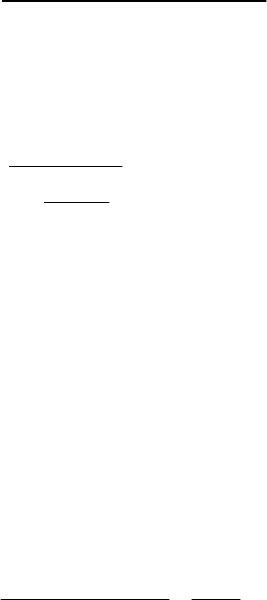
2010 SECTION VIII, DIVISION 2
4-124
()
1
3
1
12
min ,
λ
−
+
=
⎡⎤
++
⎣⎦
pr
pr n pr
Lt
C
Lt L
(4.5.119)
0.5=+
nm n n
Rt (4.5.120)
ln
n
xn
nn
n
t
R
t
R
=
⎡⎤
+
⎢⎥
⎣⎦
(4.5.121)
()
41 43
0.5
λ
=+++
tne
t t L L for nozzles inserted through
the vessel wall
(4.5.122)
()
41
0.5
λ
=+
tne
t L for nozzles abutting the
vessel wall
(4.5.123)
[
exp=−
tt
Cx (4.5.124)
c) STEP 3 – Determine the maximum local primary membrane stress in the nozzle at the intersection.
2
13
2
2
on nm t xn
L
nn
RCCC PR
P
tC t
λ
=+ (4.5.125)
d) STEP 4 – The maximum local primary membrane stress at the nozzle intersection shall satisfy Equation
(4.5.126). If the nozzle is subjected to internal pressure, then the allowable stress,
allow
S , is given by
Equation (4.5.43). If the nozzle is subjected to external pressure, then the allowable stress is given by
Equation (4.5.44).
L allow
PS≤ (4.5.126)
4.5.12.2 If the nozzle is subject to external forces and moments from supplemental loads as defined in
paragraph 4.1, then the local stresses at the nozzle-to-shell intersection shall be evaluated in accordance
with paragraph 4.5.15.
4.5.13 Spacing Requirements for Nozzles
4.5.13.1 If the limits of reinforcement determined in accordance with paragraph 4.5.5 for nozzles in
cylindrical or conical shells or paragraph 4.5.10 for nozzles in spherical or formed heads, do not overlap, no
additional analysis is required. If the limits of reinforcement overlap, the following procedure shall be used or
the design shall be evaluated in accordance with the design by analysis rules of Part 5.
4.5.13.2 The maximum local primary membrane stress and the nozzle maximum allowable working
pressure shall be determined following paragraphs 4.5.5 or 4.5.10, for each individual nozzle with the value of
R
L determined as follows.
a) For two openings with overlapping limits of reinforcement (see Figure 4.5.11):