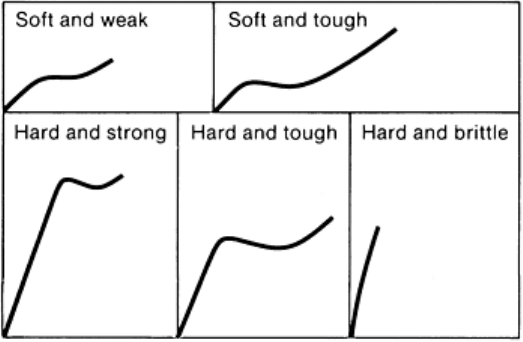
stretched farther than metallic bonds, it is possible to have a recoverable strain in glassy polymers of 5% or
more. At such large strains, it is possible for the assumptions of small-strain elasticity to break down. Any
standard test procedures based on small-strain elasticity may have to be modified to account for large elastic
strains.
The mechanical behavior of polymers is also time dependent, or viscoelastic. Therefore, data based on short-
term tests have the possibility of misrepresenting the tested polymer in a design application that involves long-
term loading. The magnitude of the time dependence of polymers is very temperature dependent. Well below
the T
g
, glassy or semicrystalline polymers are only very weakly viscoelastic. For these polymers, test data based
on a time-independent analysis will probably be adequate. As the temperature is increased, either by the
environment or by heat given off during deformation, the time dependence of the mechanical response will
increase.
Under viscoelastic conditions, one method useful for obtaining long-term design data is the time-temperature
superposition principle. This principle states that the mechanical response at long times at some particular
temperature is equivalent to the mechanical response at short times but at some higher temperature (Ref 8). By
determining shift factors, it is possible to determine which temperature to use in obtaining long-term data from
short-term tests. This is essentially true for linear viscoelastic behavior in the absence of a phase change.
The short-term tensile test (ASTM D 638 and ISO 517) is one of the most widely used mechanical tests of
plastics for determining mechanical properties such as tensile strength, yield strength, yield point, and
elongation. The stress-strain curve from tension testing is also a convenient way to classify plastics (Fig. 6). A
soft and weak material, such as PTFE, is characterized by low modulus, low yield stress, and moderate
elongation at break point. A soft but tough material such as polyethylene shows low modulus and low yield
stress but very high elongation at break. A hard and brittle material such as general-purpose phenolic is
characterized by high modulus and low elongation. It may or may not yield before break. A hard and strong
material such as polyacetal has high modulus, high yield stress, high ultimate strength (usually), and low
elongation. A hard and tough material such as polycarbonate is characterized by high modulus, high yield
stress, high elongation at break, and high ultimate strength.
Fig. 6 Tensile stress-strain curves for several categories of plastic materials
Because of the diversity of mechanical behavior, the tension testing of plastics is subject to potential
misapplication or misinterpretation of test results. This is particularly true for thermoplastics, which have some
important differences with thermoset plastics. Compared to thermoset resins, thermoplastics exhibit more
disruption or changes in the secondary bonding between the molecular chains during tension testing. This leads
to a variety of postyield phenomena, such as the stiffening observed in polyethylene (Fig. 4). Another example
is shown in Fig. 7. At the yield point the average axis of molecular orientation in thermoplastics may begin to
conform increasingly with the direction of the stress. The term draw is sometimes used to describe this
behavior. There is usually a break in the stress-strain curve as it begins to flatten out, and more strain is
observed with a given increased stress. The result is that the giant molecules begin to align and team up in their
resistance to the implied stress. Frequently, there is a final increase in the slope of the curve just before ultimate
failure (Fig. 7). The extent to which this orientation takes place varies from one linear thermoplastic to the next,
but the effect can be quite significant. Even the smallest amount of the teaming-up effect imparts greatly
improved impact resistance and damage tolerance. In thermoplastics, there is much more area under the stress-