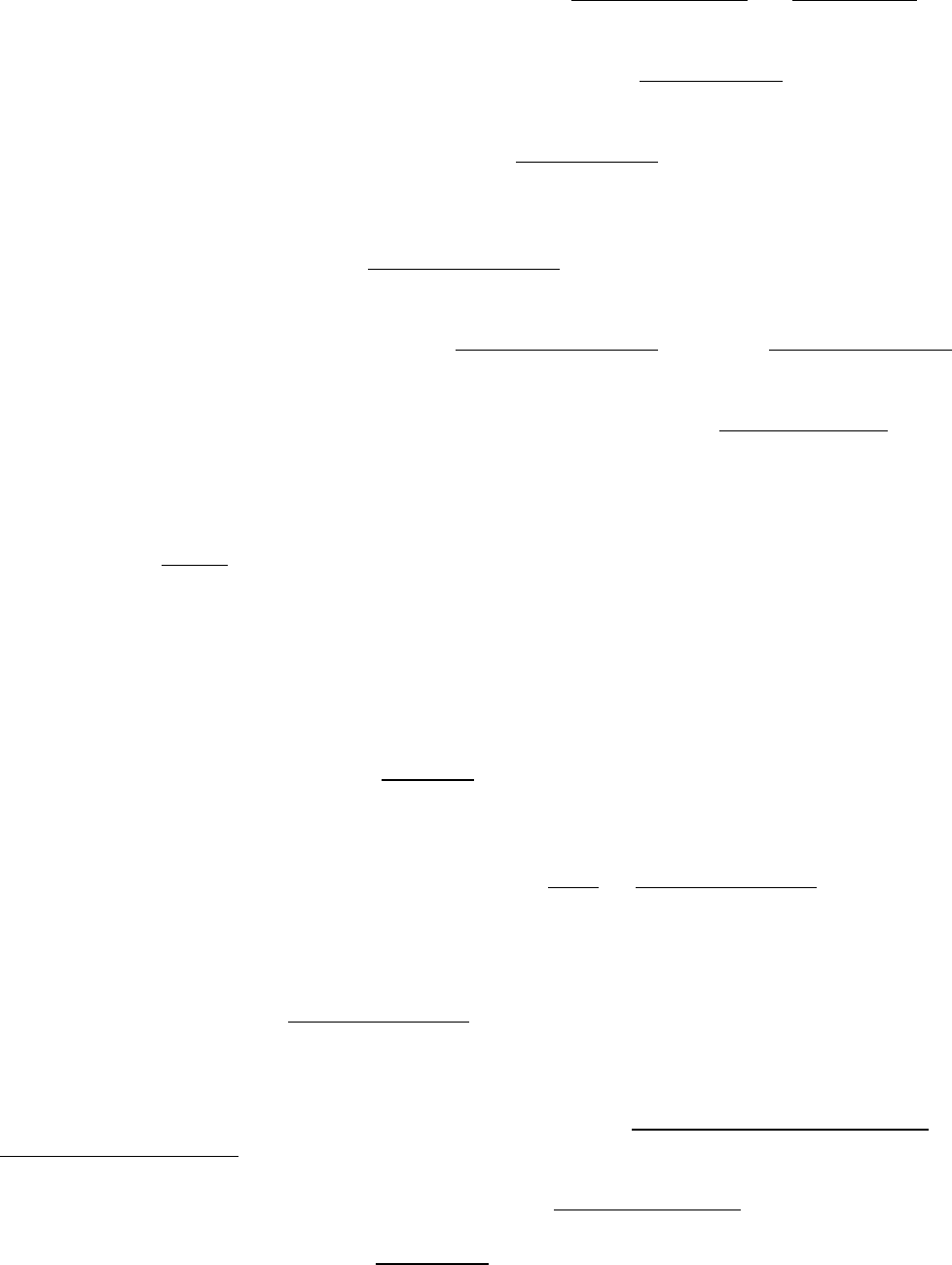
A gray and amorphous fracture surface that results when a metal is sufficiently ductile for the crystals to
elongate before fracture occurs. When a fibrous fracture is obtained in an impact test, it may be regarded
as definite evidence of toughness of the metal. Contrast with crystalline fracture and silky fracture.
fibrous structure
(1) In forgings, a structure revealed as laminations, not necessarily detrimental, on an etched section or
as a ropy appearance on a fracture. It is not to be confused with the ductile fracture of a clean metal. (2)
In wrought iron, a structure consisting of slag fibers embedded in ferrite. (3) In rolled steel plate stock, a
uniform, fine-grained structure on a fractured surface, free of laminations or shale-type discontinuities.
As contrasted with (1), it is virtually synonymous with ductile fracture.
file hardness
Hardness as determined by the use of a steel file of standardized hardness on the assumption that a
material that cannot be cut with the file is as hard as, or harder than, the file. Files covering a range of
hardnesses may be employed. See also scratch hardness test.
fixed-load or fixed-displacement crack-extension-force curves
Curves obtained from a fracture mechanics analysis for the test configuration, assuming a fixed applied
load or displacement and generating a curve of crack-extension force versus the effective crack size as
the independent variable.
flare test
A test applied to tubing, involving tapered expansion over a cone. Similar to pin expansion test.
flattening test
A quality test for tubing in which a specimen is flattened to a specified height between parallel plates.
flexibility
The quality or state of a material that allows it to be flexed or bent repeatedly without undergoing
rupture. See also flexure.
flexural modulus
Within the elastic limit, the ratio of the applied stress on a test specimen in flexure to the corresponding
strain in the outermost fiber of the specimen. Flexural modulus is the measure of relative stiffness.
flexural strength
The maximum stress in the outer fiber at the moment of crack or break.
flexure
A term used in the study of strength of materials to indicate the property of a body, usually a rod or
beam, to bend without fracture. See also flexibility.
flow
Movement (slipping or sliding) of essentially parallel planes within an element of a material in parallel
directions; occurs under the action of shear stress. Continuous action in this manner, at constant volume
and without disintegration of the material, is termed yield, creep, or plastic deformation.
flow lines
Texture showing the direction of metal flow during hot or cold working. Flow lines often can be
revealed by etching the surface or a section of a metal part.
flow stress
The stress required to produce plastic deformationin a solid metal.
forged roll Scleroscope hardness number (HFRSc or HFRSd)
A number related to the height of rebound of a diamond-tipped hammer dropped on a forged steel roll.
It is measured on a scale determined by dividing into 100 units the average rebound of a hammer from a
forged steel roll of accepted maximum hardness. See also Scleroscope hardness number and
Scleroscope hardness test.
formability
The ease with which a metal can be shaped through plastic deformation. The evaluation of the
formability of a metal involves measurement of strength and ductility, as well as the amount of
deformation required to cause fracture. Workability is used interchangeably with formability; however,
formability refers to the shaping of sheet metal, while workability refers to shaping materials by bulk
deformation (i.e., forging or rolling).
forming limit diagram (FLD)