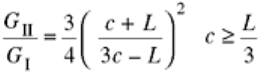
(Eq 35)
For c < L/3, crack face contact may occur, which invalidates the analysis above. Equation (35) may be used for
initial (approximate) calculation of the mode mix, which ultimately should be calculated using Eq 33b.
The preceding sections of this article have presented a practical overview of the characterization methods used
to measure the fundamental mechanical properties of advanced composite materials. Methods for determining
basic engineering strength and elastic properties of lamina, structural properties of laminates, including open-
hole and damage tolerance performance, and the material fracture properties have been presented.
Understanding these static engineering properties and structural performance characteristics is crucial for
making material selection decisions and for preliminary design development. While necessary, these properties
are not the complete set of data required to design a structure. Design engineers must address numerous other
issues, such as environmental effects, fatigue behavior, creep, and behavior under extreme dynamic loading.
Two articles that follow provide valuable insights into how high strain rate and fatigue behavior of composites
are characterized.
Footnote
*
The section “Interlaminar Shear Properties of Fiber-
Reinforced Composites at High Strain Rates” was written
by John Harding and Stephen Hallett, Oxford University. The section “Fatigue Testing and Behavior of Fiber-
Reinforced Composites” was written by W. Steven Johnson and Ramesh Talreja, Georgia Institute of
Technology.
References cited in this section
4. J.M. Whitney, I.M. Daniel, and R.B. Pipes, Experimental Mechanics of Fiber Reinforced Composite
Materials, revised ed., Society for Experimental Mechanics; Prentice-Hall, Englewood Cliffs, 1984
8. L.A. Carlsson and R.B. Pipes, Experimental Characterization of Advanced Composite Materials, 2nd
ed., Technomic, Lancaster, 1987
9. D.W. Wilson and L.A. Carlsson, Mechanical Characterization of Composite Materials, Physical
Methods of Chemistry, 2nd. ed., Vol VII, B.W. Rossiter and R.B. Baetzold, Ed., John Wiley & Sons,
1991, p 139
50. H.L. Ewalds and R.J.H. Wanhill, Fracture Mechanics, Edward Arnold, London, 1989
51. S.-M. Lee, An Edge Crack Torsion Method for Mode III Delamination Fracture Testing, J. Compos.
Technol. Res., Vol 15, 1993, p 193
52. P. Davies, B.R.K. Blackman, and A.S. Brunner, “Standard Test Methods for Delamination Resistance of
Composite Materials: Current Status, Appl. Compos. Mater., Vol 5, 1998, p 345
53. J.W. Gillespie, Jr. and L.A. Carlsson, Interlaminar Fracture of Laminated Composite Materials,
Delaware Composites Design Encyclopedia, Vol 6, Technomic, Lancaster, 1990, p 113
54. Z. Suo, Delamination Specimens for Orthotropic Materials, J. Appl. Mech., Vol 57, 1990, p 627
55. W.B. Bascom, R.J. Bitner, R.J. Moulton, and A.R. Siebert, The Interlaminar Fracture of Organic-Matrix
Woven Reinforced Composites, Composites, Vol 11, 1980, p 9
56. T.K. O'Brien and R.H. Martin, Results of ASTM Round Robin Testing for Mode I Interlaminar Fracture
Toughness of Composite Materials, J. Compos. Technol. Res., Vol 15, 1993, p 327