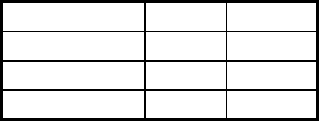
Material t, mm
D, mm
0° Uni tape 1.00 3.00
90° Uni tape
2.50 7.50
Fabric 2.50 7.50
Fig. 14 Boeing-modified ASTM D 695 compression test fixture. Source: Ref 10
The standard specimen is 80.8 mm (3.2 in.) long and 12.7 mm (0.5 in.) wide. Specimen thickness
recommendations are given in the table in Fig. 14. A thin, tabbed specimen subjected to compression is face-
supported along its length, except for the 4.8 mm (0.19 in.) long gage section, and buckling is commonly not a
problem. For compressive strength determination, two continuous lateral supports without the strain gage recess
are used. Typically, untapered [0/90°] or plain-weave fabric tabs made from the same type of material as that
being tested are used. To determine the modulus, a strain gage is bonded at the center of an untabbed specimen,
and a lateral support with a central cutout to provide clearance for the strain gage and its connections is used.
As an alternative, continuous supports may be used with an extensometer attached to the specimen edge. The
specimen should be deformed at least to 0.3% (Ref 10).
The end-load introduction can cause axial splitting or bearing failures on the loaded ends. This must be
prevented and has prompted the use of tabs and end caps. Another problem is alignment. Alignment depends on
the machining precision of the specimen ends; that is, on the parallelism between opposing ends and the
perpendicularity of these ends to the specimen loading axis. Not only must the specimen be precise, but the test
machine platens must also be precisely parallel and aligned with the axis of the test machine. Tolerances for
specimen thickness and thickness of the tabbed region (t and D in Fig. 14) are ±0.1 mm (±0.004 in.). Tabs must
be flat, parallel, and of equal thickness to within 0.05 mm (0.002 in.). Ends must be surface ground flat to
within 0.03 mm (0.001 in.) and perpendicular to the reference axis. The third source of alignment error is
specimen insertion. Much of the fixture-design complexity revolves around the preservation of specimen
alignment in the test machine.
Because of the end loading, severe stress concentrations exist at the loaded ends. For the untabbed specimens
used to measure modulus, this is not considered a problem because the central region is far away from the
loaded edges. For the tabbed strength specimen, the use of tabs prevents failure at the loaded ends. For valid
strength tests, failure modes and strength values similar to those seen with other compression test methods have
been observed (Ref 10). Specimen fabrication, bonding of end tabs, and testing are equivalent to those specified
for the IITRI test.
A number of studies have been conducted exploring the use of [0/90°] laminate configurations to obtain better
strength results (Ref 24, 25). Results have shown that the highest strengths and lowest variability are measured
using [90/0
2
/90°]s laminates. Work by Welsh and Adams (Ref 26) confirmed the benefit of using [90/0°]
laminate subgroupings to achieve higher strengths for either IITRI or modified ASTM D 695 test
configurations. This is one area where serious consideration is being given to develop a standard based on
laminate tests for determination of lamina properties.
Extending this concept, Adams and Welsh (Ref 27) have developed a new test method that uses combined
loading to measure compression strength. The method uses both shear and end loading to test the [90/0°]
laminate specimen and has been shown to produce results that are consistent with properly conducted tests
using existing ASTM methods. An advantage of the method is the ease of testing and very consistent (low
scatter) results. The method is currently under review for ASTM standardization.
Flexure Testing
Flexure, or bending, tests have emerged because of the simplicity of specimen preparation and testing. Figure
15 shows stresses developed in the three-point flexure test. It is readily observed that gripping, buckling, and
end-tabbing are not issues for this test and that testing is very simple. Analysis of the test reveals that the
bending moment is balanced by a distribution of normal stress, σ
x
. The top side is under compression while the
bottom surface is under tension. Theoretically, the neutral axis is identically at the midplane where the shear
stress, τ
xy
, is maximum (see, e.g., Ref 28). In practice, differences in the tension and compression moduli
exhibited by many composites invalidate this assumption, moving the neutral axis off the midplane of the beam
and, unless corrected, making standard data reduction calculations erroneous. Depending on the span-to-