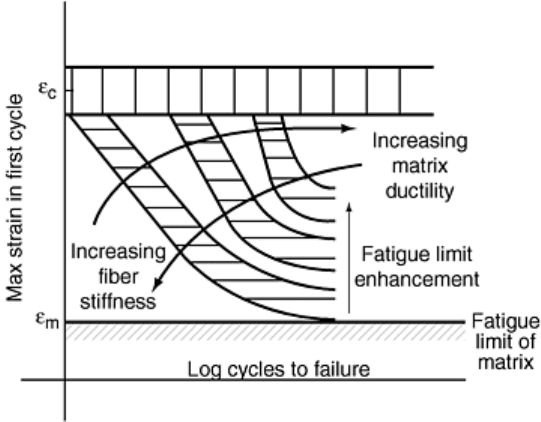
ductility, the mechanisms are affected and the resultant effects on the fatigue life can be easily understood by
observing changes in the fatigue life diagrams. For instance, an increase in the fiber failure strain will displace
region 1 upwards, while increasing fiber stiffness will delay matrix crack growth, shifting region 2 to the right
as indicated in Fig. 55. On the other hand, increasing matrix ductility will enlarge the crack-tip plastic zone,
thereby increasing crack-tip opening displacement and straining the bridging fibers further. The detrimental
effect on fatigue life by this change in the mechanism will shift region 2 (Fig. 51) to the left (Fig. 55). Finally,
improved fatigue properties of the matrix material and reduced fiber stiffness will raise the composite fatigue
limit, reducing thereby the range of strain in which fatigue failure can occur.
Fig. 55 Trends in the fatigue life diagram induced by fiber stiffness and matrix ductility
In high temperature materials, such as MMCs and CMCS, the residual stresses can be large. For instance, in
SCS-6/Ti-15-3, the residual stress on cooldown to the room temperature is compressive in the fibers. The
inelastic cyclic deformation can relieve this stress and thereby increase the probability of fiber failure. This
changes region 1 of the fatigue life diagram from having a horizontal scatter band of nonprogressive fiber
failure to a sloping scatter band of cycle-dependent progressive failure. At high temperatures, the residual
compressive stress in fibers decreases while the matrix inelastic deformation increases. These two effects
render the fiber failure mechanism of region 1 even more progressive. The slope of region 1, thus, increases
with increasing temperature (Ref 80).
In CMCs, where both constituents are brittle, the source of irreversibility in cyclic loading is provided primarily
by friction at the debonded fiber/matrix interfaces. The fiber stress redistribution with cycles is caused by load
transfer between matrix and fibers through the frictional shear stress at the interface. At room temperature, at
which the matrix behaves in a brittle manner, its role in the fatigue process is not significant. Region 1 and
region 2 of the fatigue life diagram are then not as easily separable as in PMCs and MMCs. The dominant
mechanism in both regions is fiber failure, whose progression is governed by the fiber/matrix interface. A
fatigue limit still exists but is not governed by the matrix. As discussed in (Ref 81), the fatigue limit in this case
is given by the threshold below which the rate at which fibers are broken in a cycle is exceeded by the rate at
which fibers bridge the matrix crack.
Effects of Fiber Architecture. In multidirectional laminates, other mechanisms in addition to those previously
described come into play. These additional mechanisms consist primarily of multiple intralaminar cracking of
off-axis plies and interlaminar cracking (delamination). These mechanisms can be viewed as subcritical, while
those associated with failure of on-axis plies should be viewed as critical. The role of the subcritical
mechanisms is thus seen as effecting stress transfer from off-axis plies to on-axis plies. This stress transfer
occurs progressively, and failure occurs when the on-axis plies are stressed to their limiting value.
The progression of intralaminar cracking in off-axis plies is conveniently described by the evolution of the
average number of cracks per unit length normal to the crack planes (or inverse of the average crack spacing).
This crack density parameter is shown plotted against the number of load cycles of different maximum load
value for a glass/epoxy cross ply laminate in Fig. 56. The evolution rate of this parameter depends on the