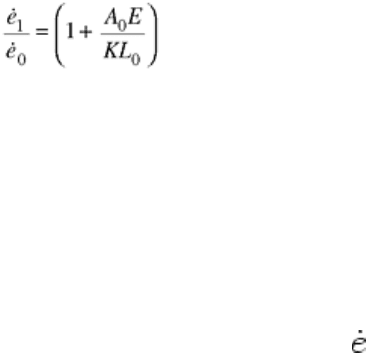
However, beyond the yield point, the stress rate is small so that the strain rate remains close to the specific
crosshead rate (Eq 11). Thus, ductile materials, for which a rather long time will elapse before reaching ultimate
strength, have a time-average strain rate from the beginning of the test to ultimate that is only slightly less than
the specific crosshead rate. Also, because the load rate is zero at ultimate as well as at yield, the instantaneous
strain rate at ultimate equals the specific crosshead rate.
During a test at constant crosshead speed, the variation of strain rate from initial to yield-point values is
precisely the inverse of the crosshead speed change required to maintain a constant strain rate (Eq 9):
(Eq 12)
Consequently, in an ordinary tension test, the yield strength and ultimate tensile strength may be determined at
two different strain rates, which can vary by a factor of 20 to 100, depending on machine stiffness. If a yield
drop occurs, elastic recovery of machine deflections will impose a strain rate even greater than the specific
crosshead rate given by Eq 12.
A point of interest from the analysis involves testing of different sized specimens at about the same initial strain
rate. Assuming that these tests are to be made on one machine under conditions for which K remains
substantially constant, the crosshead speed must be adjusted to ensure that specimens of different lengths,
diameters, or materials will experience the same initial strain rate. In the typical case where the specimen is
much stiffer than the machine, (1 + A
0
E/KL
0
) in Eq 10 can be approximated simply by (A
0
E/KL
0
), so that the
initial strain rate is approximately
0
= SK/A
0
E. Thus, specimens of various lengths, tested at the same
crosshead speed, will generally experience nearly the same initial strain rate. However, changing either the
specimen cross section or material necessitates a corresponding change in crosshead speed to obtain the same
initial rate.
A change in specimen length has substantially the same effect on both the specific crosshead rate (S/L
0
) and the
stiffness ratio of specimen to machine (A
0
E/KL
0
) and, therefore, has no net effect. For example, an increase in
specimen length tends to decrease the strain rate by distributing the crosshead displacement over the longer
length; however, at the same time, the increase in length reduces the stiffness of the specimen so that more of
the crosshead displacement goes into deformation of the specimen and less into deflection of the machine.
These two effects are almost exactly equal in magnitude. Thus, no change in initial strain rate is expected for
specimens of different lengths tested at the same crosshead speed.
References cited in this section
4. G.E. Dieter, Mechanical Metallurgy, McGraw-Hill, 2nd ed., 1976, p 349
5. D.J. Shippy, P.P. Gillis, and K.G. Hoge, Computer Simulation of a High Speed Tension Test, J. Appl.
Polym. Sci., Applied Polymer Symposia (No. 5), 1967, p 311–325
6. P.P. Gillis and D.J. Shippy, Vibration Analysis of a High Speed Tension Test, J. Appl. Polym. Sci.,
Applied Polymer Symposia (No. 12), 1969, p 165–179
7. M.A. Hamstad and P.P. Gillis, Effective Strain Rates in Low-Speed Uniaxial Tension Tests, Mater. Res.
Stand., Vol 6 (No. 11), 1966, p 569–573
8. P. Gillis and J.J. Gilman, Dynamical Dislocation Theories of Crystal Plasticity, J. Appl. Phys., Vol 36,
1965, p 3375–3386
9. J.E. Hockett and P.P. Gillis, Mechanical Testing Machine Stiffness, Parts I and II, Int. J. Mech. Sci., Vol
13, 1971, p 251–275
10. W.G. Johnston, Yield Points and Delay Times in Single Crystals, J. Appl. Phys., Vol 33, 1962, p 2716
11. H.G. Baron, Stress-Strain Curves of Some Metals and Alloys at Low Temperatures and High Rates of
Strain, J. Iron Steel Inst. (Brit.), Vol 182, 1956, p 354