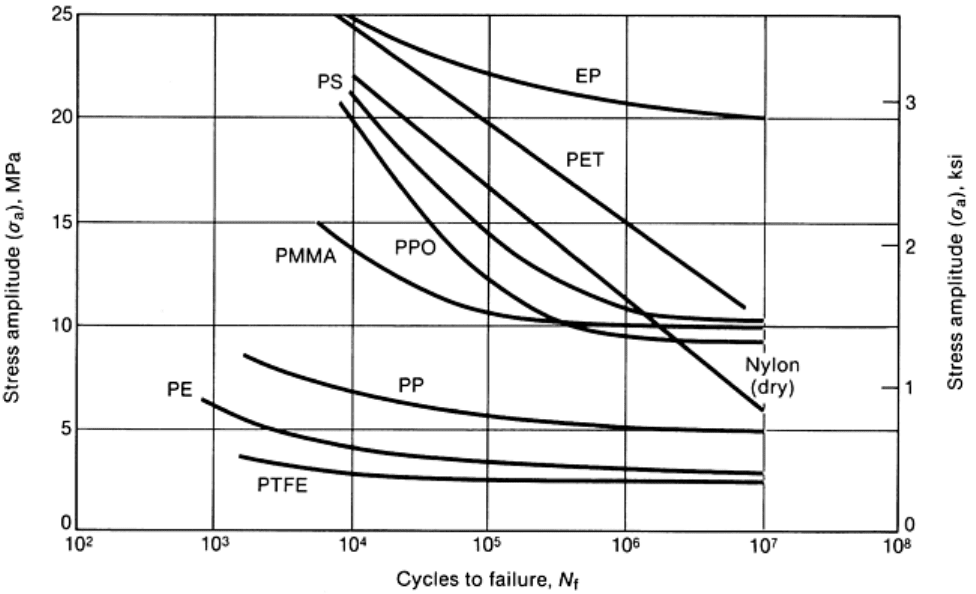
where σ
max
is the maximum stress and σ
min
is the minimum stress of the fatigue cycle. The stress amplitude,
also denoted as S, is generally plotted against the number of cycles to failure, N, on a linear-log scale, which is
called an S-N plot. A general trait of these plots is that the number of cycles to failure increases as the stress
amplitude is reduced. In some polymers, there is a critical stress level, often referred to as the endurance limit
of the material, below which the specimen does not fail in less than 10
7
cycles.
Figure 2 shows the S-N behavior of several commodity plastics. It should be noted that nylon and polyethylene
terephthalate (PET) do not exhibit an endurance limit. Other plastics—including polyethylene (PE),
polypropylene oxide (PPO), polystyrene (PS), polytetrafluoro-ethylene (PTFE), polypropylene (PP),
polymethyl-methacrylate (PMMA), and epoxy (EP)—exhibit a stress limit below which failure does not occur
in less than 107 cycles for these testing conditions. Because plastics are sensitive to many factors including
frequency, temperature, mean stress, and molecular structure, the fatigue test conditions must closely mimic the
service conditions of the polymeric component. Despite the simple nature of these experimental tests, the S-N
approach is widely accepted in the engineering plastics community for design applications where stress
concentrations are expected to be minimal or where the fatigue life of the component is likely to be dominated
by the nucleation of a crack.
Fig. 2 Stress amplitude versus cycles to failure, or S-N behavior, of several commodity plastics
Displacement and Strain-Based Loading. While stress-based tests are appropriate for the evaluation of plastics
chosen for load-controlled applications, these tests might not be suitable for circumstances where the structural
component is likely to experience fluctuations in displacement or strain. In such instances, strain- or
displacement-based tests might be more appropriate. In such tests, the configuration typically is based on a
fixed cantilever subjected to repeated constant deflection. The initial stress range will typically decay under
cyclic loading (much like a stress relaxation experiment) and is caused by plastic deformation or softening of
the polymer. Hysteretic heating from deformation can further result in an inaccurate prediction of the cyclic
stress amplitude (Ref 9). However, because stresses generally decay in this type of test, thermal failures are
rarely encountered (Ref 5).
Strain-based tests are often utilized for components with accumulated strain or blunt notches (Ref 5). The
majority of strain-based fatigue tests are performed using fully reversed loading conditions, generally
accompanied by a cyclic softening phenomena in plastics (Ref 2, 9). Under cyclic strain conditions, the fatigue
response is best characterized by the cyclic stress-strain curve. This curve is created by testing several
specimens subjected to a range of controlled cyclic strain limits. Tests are continued for each specimen until the
hysteresis loops become saturated. A curve is fit through the amplitude of these saturated hysteresis loops in