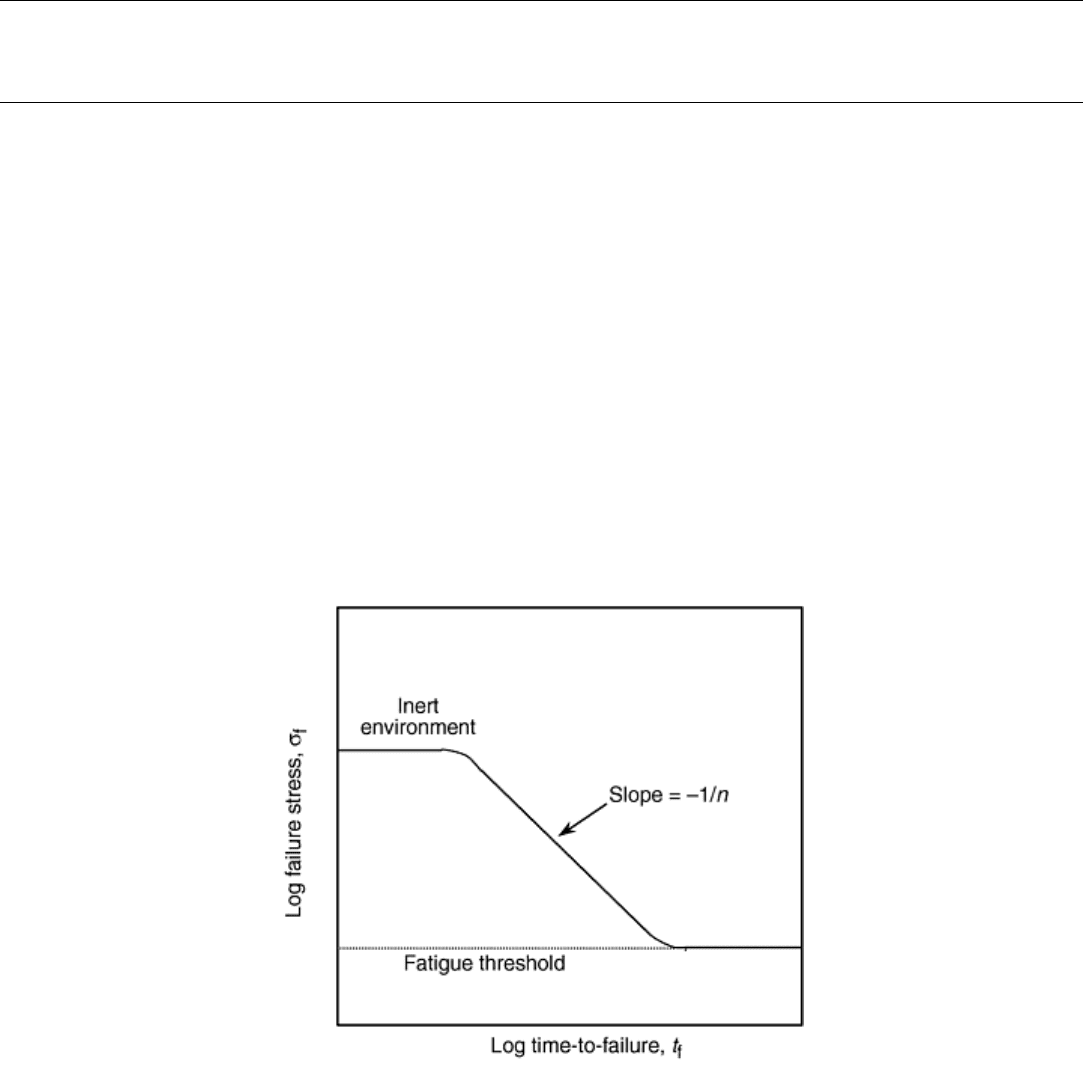
Fatigue Testing of Brittle Solids
J.A. Salem, Glenn Research Center at Lewis Field; M.G. Jenkins, University of Washington
Strength-Based Test Methods
Strength-based methods or “indirect” methods employ smooth test specimens, such as flexural beams or tensile
specimens, and estimate fatigue properties from strengths measured over different time intervals. Strength-
based methods directly sample the flaw distribution within or on the surface of the test specimens. The cracks
thus develop from at least some of the same sources as in a component of the same material. However, the
results are subject to the scatter inherent in the strength distribution of the material, and thus a relative large
number of tests are required. Further, strength-based methods do not measure the actual crack size but infer it
from the measured strength.
Three basic strength test methods and accompanying analytical relations have been developed for determining
the fatigue parameters and behavior of ceramics and glasses: static loading, dynamic loading, and cyclic
loading.
Static Loading. Typically, tensile specimens or flexure specimens (e.g., beams or plates) are subjected to a
constant load in the environment of interest. The time-to-failure and the applied stress are recorded and used to
determine the fatigue parameters according to any of the Eq 1, 2, 3, 4, and 5. The generalized slow crack
growth behavior for static loading is shown in Fig. 2.
Fig. 2 Generalized failure stress as a function of time-to-failure on a logarithmic scale for ceramics and
glasses exhibiting environmentally induced slow crack growth
One test method, Japanese Industrial Standard (JIS) 1632 “Test Methods for Static Bending Fatigue of Fine
Ceramics,” has been standardized for the determination of fatigue strength by static loading (Ref 18) at room or
elevated temperatures. The standard gives guidance on the test method but not in the calculation of fatigue
parameters such as A and n.
Uniaxial flexural test specimens are manufactured and tested in three- or four-point loading in accordance with
JIS R 1601, “Test Method for Flexural Strength (Modulus of Rupture) of Fine Ceramics” (Ref 56). The use of
at least three stress levels is recommended, and the breaking times at one of the stress levels must be distributed
between 0 and 100 h, minimum. No requirement on the number of test pieces is specified; however, three tests
per stress level are recommended. Tests may be stopped after 100 h if failure has not occurred. An initial
fatigue stress equal to 75% of the fracture strength is used. Subsequent stresses differing by 5 to 10% from the
initial fatigue load are applied, depending on the initial time-to-failure and scatter in the data. An example of
failure stress data as a function of the failure time is shown in Fig. 3 (Ref 18).