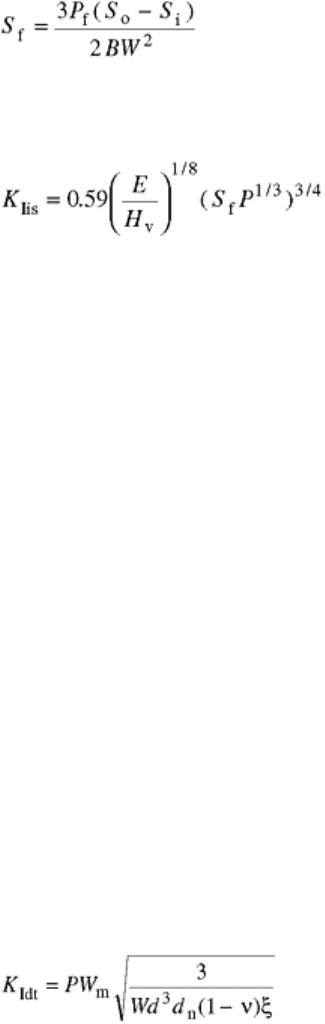
SEPB and SCF) without the need to precrack the test specimen (Ref 27). In addition, measurement of the notch
depth at fracture allows the use of the same well-established equations, such as those used for SEPB method
(e.g., Eq 11, 12, and 15) for calculating fracture toughness.
The IS method is based on the applications of Eq 1 and 4 to the flexural strength testing of flexural test
specimens that have been indented (either Knoop or Vickers) with ever-increasing indentation forces. The size
of the controlled indentation flaw increases with increasing indentation force. Therefore, for a material with a
deterministic fracture resistance, the measured flexural strength will decrease with increasing flaw size (or
increasing indentation force). The mathematics have been worked out relating fracture resistance, flexural
strength, and flaw size for sharp indenters producing median cracks (Ref 3).
The actual mechanics of the conducting test involve first placing one indentation each in a series of standard
flexure test specimens (each test specimen receives one indentation at one indentation force), such as those
specified in ASTM C 1161 (Ref 28) at ever-increasing indentation forces using either a Knoop or Vickers
indenter. A standard flexural strength test is then conducted, preferably in four-point flexure to avoid the
necessity of trying to align the small indentation with the nose of the loading support in three-point flexure. For
four-point flexure, the flexural strength is calculated as:
(Eq 17)
where S
f
is the flexural strength and P
f
is the force at fracture (typically maximum force for a brittle material).
The fracture toughness using the indentation strength method for the particular test can then be calculated using
the relation (Ref 29):
(Eq 18)
where P is the indentation force.
Obvious advantages of the IS method are that it involves readily available flexure test specimens and test
standards for both flexure strength and indentations. In addition, the IS method does not require a subjective
measure of crack size (from the viewpoint of the fracture-mechanics community, this is also an obvious
weakness) (Ref 2). Another weakness is that hardness and elastic modulus need to be measured separately. A
final point is that the constant 0.59 in Eq 18 as determined from logarithmic regression analysis (Ref 2) has an
estimated standard deviation of 0.12 (a somewhat large source of variability for a “constant”). While the IS
method is attractively simple, relative measurements on a given material “are typically reliable to much better
than 20%” (Ref 3), making the results of limited value compared to some of the other methods discussed up to
this point.
Other Test Methods for Fracture Toughness at Ambient Temperature
Many other successful methods for determining fracture toughness of brittle materials (not yet standardized)
have been introduced and refined over the past several years. Some of the more popular methods are discussed
in the following sections. Note that these discussions are limited to sharp-crack methods because of the
limitation of methods using blunt notches.
The double torsion (DT) method was once seen as a strong contender for a standard test method (Ref 4, 7, 8, 9,
and 10). This method (Fig. 10) allows the use of a variety of basic specimen shapes and test geometries,
although the most common is a long, thin plate with a side groove cut along its length to guide and crack
(although there is evidence that with good alignment, better results are obtained without the groove (Ref 31).
Ball-bearing supports tend to minimize friction and help alignment. Various analyses have shown that the
applied stress intensity factor is independent of crack length over the dimensionless crack length range of 0.55
to 0.65 a/W (Ref 4). One formulation for stress intensity factor for determining fracture toughness using the DT
method is (Ref 30):
(Eq 19)
where W
m
is half the test specimen width minus half the notch width, d is the total thickness, d
n
is the notch
depth, and ξ is a correction factor for thick test specimens such that ξ = 1 - 0.6302t + 1.20t exp (-π/τ) where t =