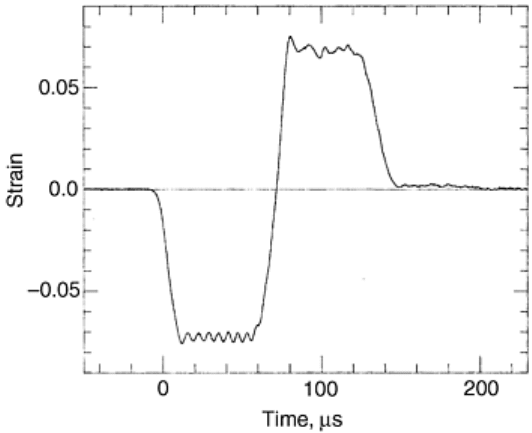
Fig. 9 A typical stress pulse generated by the stress-reversal Hopkinson bar technique. Source: Ref 7
It is important to bear in mind the significance of the perfect impedance matching of the striker bar, incident
bar, and incident tube, as well as the configuration of the transfer flange in the design of the loading fixture for
proper functioning of the stress-reversal Hopkinson technique.
From the equality of particle velocities at contacting surfaces and the conservation of linear momentum, it
follows that the particle velocity in the incident bar and incident tube at impact is V
0
/3. The particle velocity of
the compressed portion of the striker bar, relative to its unstressed part, then is 2V
0
/3. When the reflected
release-wave front in the striker reaches the contact with the transfer flange, the striker bar begins to move at
velocity V
0
/3 away from the transfer flange. At the same instant, the compression wave in the incident tube
imparts to the transfer flange exactly the same particle velocity (i.e., V
0
/3) in exactly the same direction. Thus,
the contact surfaces remain in contact for a short period, t
0
= 2l
0
/C
0
, until the striker separates at a third of its
initial impact velocity, as the flange comes to rest; here, l
0
is the common length of the striker bar and the
incident tube, and C
0
is their common longitudinal elastic-wave speed.
Strain Rate Jump. The stress-reversal technique can be used to change the strain rate during the course of
Hopkinson bar compression or tension experiments (Ref 14). Consider a recovery compression system first.
The loading (striker) end of the incident bar includes a transfer flange, an incident tube, and a reaction mass, as
sketched in Fig. 10(a). Suppose the transfer tube is in contact with the transfer flange. Then, as the striker bar
impacts the incident bar over the transfer flange, elastic compressive stresses are induced in both the incident
bar and the incident tube, as well as in the striker bar, in accordance with their impedances. To change
(decrease) the stress (and, hence, the strain) in the incident bar in the course of the experiment, a predetermined
gap is introduced between the transfer flange and the incident tube (Fig. 10b). As the striker bar now impacts
the incident bar, a compressive stress pulse is imparted into this bar, resulting in the shortening of the bar. Once
the incident bar is sufficiently shortened to come in contact with the incident tube over the transfer flange, a
stress pulse is also imparted into the incident tube, reducing the compressive stress (and, hence, the
compressive strain) in the incident bar. Since the sample strain rate is a linear function of the incident strain in
the incident bar, the procedure allows implementation of a change in the sample strain rate during the course of
the experiment. By proper choice of the gap and the involved impedances, a desired change in the sample strain
rate can be achieved.