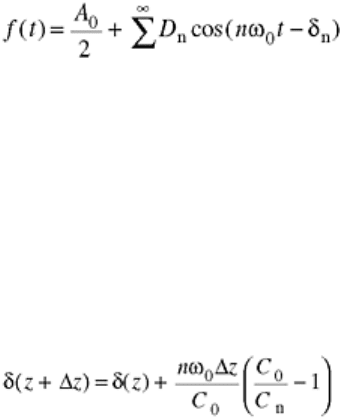
The 1- and 2-wave analyses used to calculate average stress discussed in the theory section implicitly assume
that the strain-time pulses measured at the strain gages are identical with those at the ends of the bars in contact
with the specimen. This assumption, however, is not correct because the specimen is normally smaller in
diameter than the bar such that the bar ends are not uniformly loaded across their diameter and, therefore, will
indent elastically. In addition, as the bars are compressed longitudinally, albeit elastically, they expand radially
in response to the applied force (i.e., the Poisson effect). While the exact mathematical descriptions of these
effects on the propagation of an elastic pulse through a large elastic rod are very complex, the result is that
different frequencies of pulses induced in the bars disperse with distance traveled in the bar. The result of this
dispersion is such that the pulse induced in the input bar through the impact of the striker bar does not
immediately rise into a steady square-wave impulse of fixed amplitude but rather “rings” up. These end effects
quickly dampen after the wave has propagated about ten bar diameters (Ref 40, 67).
The wave propagation behavior thereafter becomes fully described by the equation of motion in an infinite
cylindrical solid. The solution of the equation of motion for these boundary conditions was derived
independently during the late 19th century by the mathematicians Pochhammer (Ref 70) and Chree (Ref 71).
These relations were later specifically applied to address dispersion in the SHPB (Ref 12, 15, 40, 72, 73, 74).
The pressure bars have been determined to vibrate predominantly in a fundamental mode (i.e., while there are
an infinite number of potential solutions to the equation of motion according to the vibrational mode, only one
frequency appears to dominate in long elastic bars).
This vibration of the bar leads to wave dispersion that can mask resolution of the fine details in the stress-strain
data of interest, particularly at higher strain rates where the period of the oscillations can be a large fraction of
the total strain measured. While this elastic dispersion cannot be eliminated, techniques have been adopted
based on the Pochhammer-Chree equation of motion to correct for any additional dispersion that occurs during
the wave propagation from the specimen/bar interfaces to the gage locations (Ref 40, 72, 74, 75, 76, 77).
At any position, z, along the pressure bar, the wave, f(t), may be represented by an infinite cosine Fourier series:
(Eq 20)
where ω
0
is the frequency of the longest wavelength component (n = 1), and δ
n
is the phase angle of component
nω
0
. The wave dispersion in the pressure bars occurs because higher-frequency components travel more slowly
than lower-frequency components and thus lag behind the leading edge of the wave. The dispersion results in a
change of relative position and amplitude of the oscillations, together with a gradual increase in the rise time of
the pulse as it travels along the bar. Because the strains measured in the pressure bars are measured by strain
gages located some distance from the specimen, the pulse shapes at the strain-gage positions will be modified
because of the dispersion effects and therefore do not accurately represent the pulse shapes at the specimen
location.
The dispersion of the waves alters the phase angle, δ, such that at a position, z + Δz, the new phase angle can be
calculated:
(Eq 21)
where C
0
is the longitudinal wave speed in the bar, and C
n
is the velocity of component nω
0
. The value of C
n
depends on the wavelength and on the mode of vibration; in the SHPB case, this is dominated by the
fundamental mode (Ref 12). The phase angle at any position along the bar can be calculated using Eq 21, and
the wave reconstructed at that new position using Eq 20. Accordingly, the raw stress-versus-strain data
calculated using either the 1- or 2-wave analysis can be dispersion corrected by mathematically moving the
wave to a common point on the bar (e.g., the bar-sample interface). This correction removes a large amount of
the inherent wave dispersion, thereby yielding smoother final stress-strain curves (Ref 40, 43, 55, 72, 73, 78,
79).
Direct-Impact Compression Hopkinson Pressure Bar. Several researchers have suggested that one way to avoid
the dispersion problem in the incident bar is to dispense with the incident bar altogether and impact the sample
directly with the striker bar (Ref 72, 80 81 82 83 84 85 86 87 88). The initial intent of the direct-impact bar was
to be used as a means of increasing the maximum strain rate achievable. While maximum higher strain rates
can, in principle, be achieved using this technique, direct Hopkinson bars pose several difficulties. The first
difficulty is that, because there is no incident bar, there is no means to calculate the strain rate and thereby the
strain. Direct strain measurement on the sample and/or high-speed photography must be used to track diametral