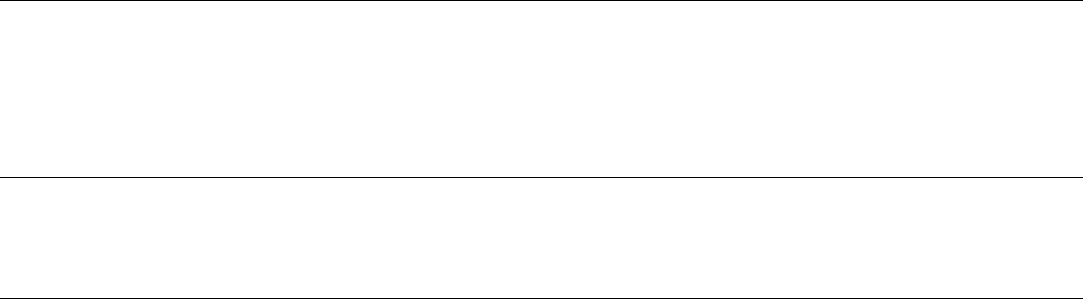
Fig. 42
Principal components of a universal unit for the immersion scanning of testpieces of various shapes and
sizes. See text for discussion.
Adjustable brackets and lazy-susan turntables can be provided on the tank bottom for support of testpieces. Clean,
deaerated water containing a wetting agent usually covers a testpiece by a foot or more, providing excellent coupling
between search unit and testpiece. For operator comfort, water temperature is usually kept at about 21 °C (70 °F), often
by automatic control.
The immersion-scanning unit shown in Fig. 42 represents a high degree of versatility in its capability to accommodate
testpieces of various sizes and shapes and to scan using various search patterns. The entire instrument cabinet and search
unit can be moved longitudinally on side rails along the length of the tank. Also, the search unit is suspended from a
manipulator mounted on a bridge, thus enabling it to be moved from side to side. These movements of the search unit are
most appropriate for scanning rectangular flat testpieces.
The universal unit illustrated in Fig. 42 can also be used for scanning testpieces of various circular shapes. For example, a
round disklike workpiece can be placed on the turntable (shown at right end of tank) and rotated while the search unit is
moved radially outward, thus producing a spiral scanning pattern. The spiral pattern is displayed on a disk-type recorder.
A cylindrical testpiece can be scanned in a helical pattern, with a drum-type recorder being used to display the data.
Accessory equipment is also available for scanning long cylinders in a horizontal position.
Reference cited in this section
8.
R.H. Grills and M.C. Tsao, Nondestructive Testing With Portable Ultrasonic Imaging System, in
Monitoring in Industrial Plants Using Nondestructive Testing and Electromechanical Methods,
American Society for Testing and Materials, 1987, p 89-101
Ultrasonic Inspection
Revised by Yoseph Bar-Cohen, Douglas Aircraft Company, McDonnell Douglas Corporation; Ajit K. Mal, University of California, Los
Angeles; and the ASM Committee on Ultrasonic Inspection
*
Inspection Standards
The standardization of ultrasonic inspection allows the same test procedure to be conducted at various times and
locations, and by both customer and supplier, with reasonable assurance that consistent results will be obtained.
Standardization also provides a basis for estimating the sizes of any flaws that are found.
An ultrasonic inspection system includes several controls that can be adjusted to display as much information as is needed
on the oscilloscope screen or other display device. If the pulse length and sensitivity controls (or their equivalents) are
adjusted to a high setting, numerous indications may appear on an A-scan display between the front-surface and back-
surface indications. On the other hand, at a low setting, the trace between front-surface and back-surface indications may
show no indications even if flaws of prohibited size are present. Inspection or reference standards are used as a guide for
adjusting instrument controls to reveal the presence of flaws that may be considered harmful to the end use of the product
and for determining which indications come from flaws that are insignificant, so that needless reworking or scrapping of
satisfactory parts is avoided.
The inspection or reference standards for pulse-echo testing include test blocks containing natural flaws, test blocks
containing artificial flaws, and the technique of evaluating the percentage of back reflection. Inspection standards for
thickness testing can be plates of various known thicknesses or can be stepped or tapered wedges.
Test blocks containing natural flaws are metal sections similar to those parts being inspected. Sections known to
contain natural flaws can be selected for test blocks.