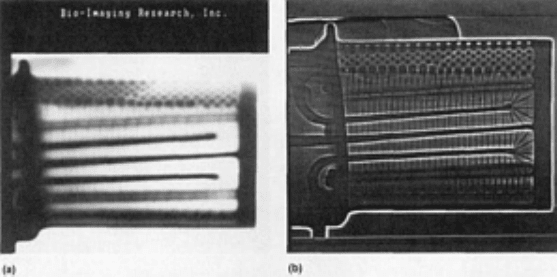
Digital image processing can be used to enhance imagery by multiple video frame integration and averaging techniques
that improve the signal-to-noise ratio of the image. This enables the radiographer to digitally adjust the contrast of the
image and to perform various edge enhancements to increase the conspicuity of many linear indications (Fig. 11).
Fig. 11
Digital radiography images of an investment cast jet engine turbine blade showing detail through a
wide range in material thickness. The
trailing edge of the blade (along the top of the image) is 2 mm (0.080
in.) thick, the root section of the blade (to the far left in the image) is 19 mm (0.75 in.) thick, and the shelf
area (to the right of the root section) is 25 mm (1 in.) thick. The ima
ge shown in (a) is unprocessed; the image
in (b) is processed to subdue the background and to enhance edges and internal features.
Isaacson, Bio-Imaging Research, Inc.
Interpretation of the radiographic image requires a skilled specialist who can establish the correct method of exposing the
castings with regard to x-ray energies, geometric relationships, and casting orientation and can take all of these factors
into account to achieve an acceptable, interpretable image. Interpretation of the image must be performed to establish
standards in the form of written or photographic instructions. The inspector must also be capable of determining if the
localized indication is a spurious indication, a film artifact, a video aberration, or a surface irregularity. The article
"Radiographic Inspection" in this Volume provides additional information on real-time digital systems.
Computed tomography, also known as computerized axial tomography (or CAT scanning), is a more sophisticated x-
ray imaging technique originally developed for medical diagnostic use (Ref 2). It is the complete reconstruction by
computer of a tomographic plane, or slice of an object. A collimated (fan-shaped) x-ray beam is passed through a section
of the part and is intercepted by a detector on the other side. The part is rotated slightly, and a new set of measurements is
made; this process is repeated until the part has been rotated 180°.
The resulting image of the slice (tomogram) is formed by computer calculations based on electronic measurement (digital
sampling) of the radiation transmitted through the object along different paths during the rotating scan. The data thus
accumulated are used to compute the densities of each point in the cross section, enabling the computer to reconstruct a
two-dimensional visual image of the slice.
The shapes of internal features are determined by their computed densities. After one slice is produced through a
complete rotation, either the part or the radiation source and detector can be moved and a three dimensional image built
up through the scanning of successive slices.
Compared to electronic radiography, computed tomography provides increased sensitivity and detection capabilities. The
contrast resolution of a good-quality tomographic image is 0.1 to 0.2%, which is approximately two orders of magnitude
better than with x-ray film.
In addition, images are produced in a quantitative, ready-to-use digital format (Ref 3). They provide detailed physical
information, such as size, density, and composition, to aid in evaluating defects. Methods are being developed to use this
information to predict failure modes or system performance under operating loads. The data can also be easily
manipulated to obtain various types of images, to develop automated flaw detection techniques, and to promote efficient
archiving. Figures 12 and 13 illustrate the uses of computed tomography for examining castings. More detailed
information can be found in the article "Industrial Computed Tomography" in this Volume.