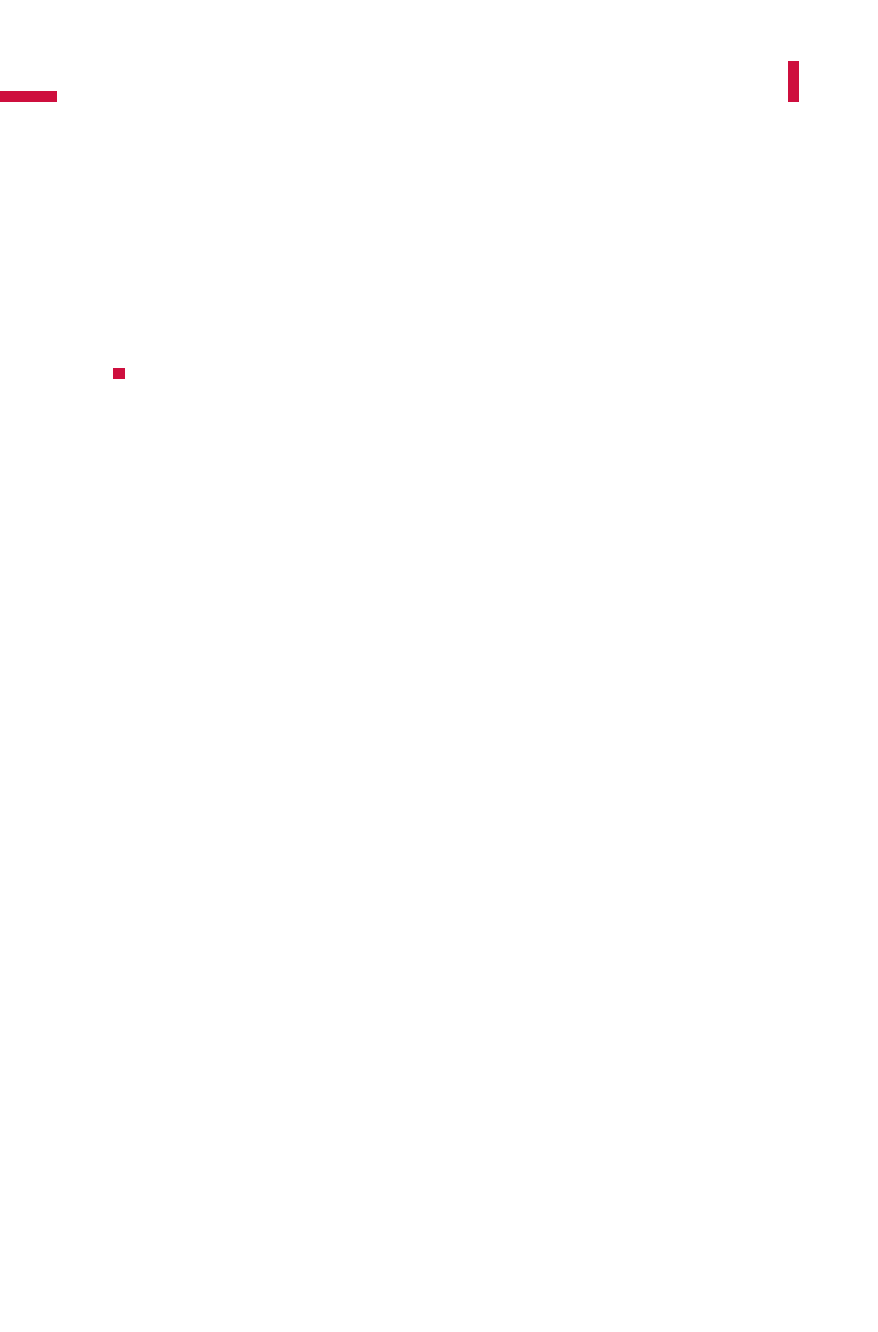
cold forging, and the necessary supporting effect of the substrate mate-
rial is not achieved. Once a continuous increase in the hardness of the
substrate material through to the actual coating has been successfully
achieved, more success can be expected. It may be possible to achieve
this result using plasma nitriding and subsequent coating with CrN or
TiAlN, or through the development of special sandwich coatings.
6.7.4Die closing systems (multiple-action dies)
Recent developments in the field of die closing systems have substan-
tially increased the range of parts that can be produced using the cold
and warm forging methods. Flashless forging of spiders, spherical hubs,
tie rod ends, T-fittings for radiator construction, rotors and parts with
different gearing has only become possible with the development of die
closing systems.
With an additional closing force initiated in the die set, female dies
are closed before the bottom dead center of the slide is reached.
Somewhat later, the material is then formed, flashless, in the closed die
by penetration of the punch. Flashless pressing is only possible if the
pre-form can be completely located in the dies when these are closed.
The closing force itself can be initiated by means of elastomers,
hydraulic systems, or mechanically by the kinematics of the press.
Elastomers offer the advantage that their design is simple and their
spring characteristic can be adjusted within certain limits by altering
the material composition. However, they only permit limited travel.
The elastomers also have to be exchanged periodically. Hydraulic clos-
ing systems generate high closing forces within a minimum of space,
and can thus be positioned adjacent to each other in multiple-station
dies. By adjusting the pressure, a greater closing force range can be cov-
ered. However, their design is more complex, and they call for a num-
ber of safety precautions to protect both the operator as well as the dies.
In modern presses, mechanical initiation of closing motions can be
achieved over a large crank angle range. However, the investment here
is substantially higher than that needed for elastomer or hydraulic sys-
tems.
Figure 6.7.9illustrates the basic layout of a hydraulic closing system
integrated fully into the die. In the provided example, there is a closing
502
Solid forming (Forging)
Metal Forming Handbook / Schuler (c) Springer-Verlag Berlin Heidelberg 1998