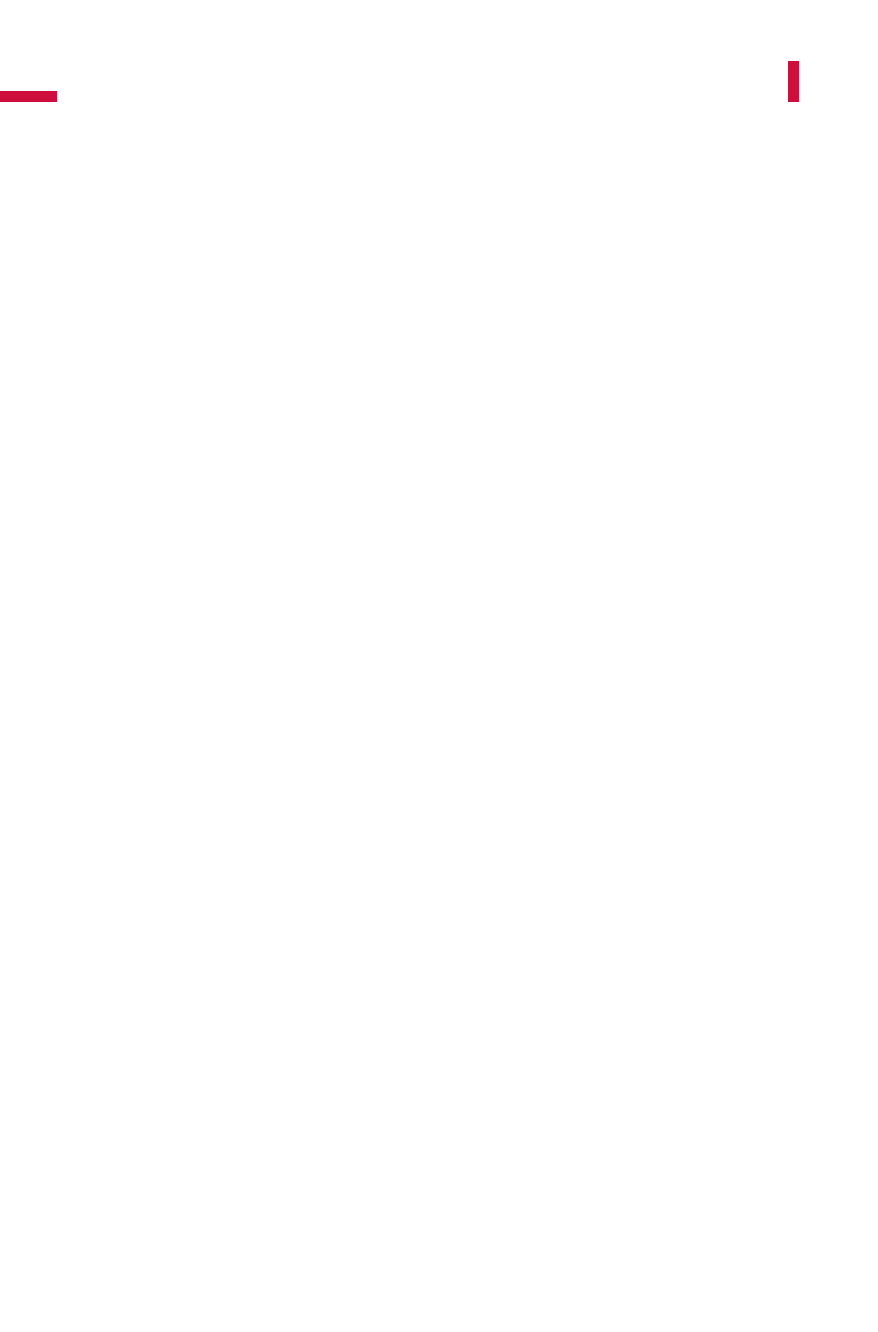
part. Our present example has a mechanical ejector curve with a stroke
of 200mm which is travelled through at 80°crank angle: In this case,
no pneumatic ejector is required. The starting point for the ejector
curve can be optionally selected, allowing the curve in the diagram
(Fig. 6.6.2)to be displaced horizontally. The slope of the ejector curve
can be configured in such a way that it corresponds approximately to
the linear portion of the slide curve.
Starting with the transverse movement of the connecting rod, the
slide ejector curve is generated by the corresponding kinematic
(Fig. 6.6.2, dashed line). For the transfer study, this curve can be dis-
placed only vertically.
The curve of the pneumatic ejector, whose actual distance from the
slide curve must be determined with the transfer study, runs parallel to
the slide curve (Fig. 6.6.2, broken line).The slide ejector acts mechani-
cally briefly after the bottom dead center and can be operated pneu-
matically after that.
In addition to these main press motions, in universal transfer devices
the curves for opening and shutting the grippers are also significant. The
opening and closing times can normally be adjusted within certain lim-
its, e.g. within a 30°range, making the curves horizontally displaceable
in the transfer study. The opening stroke is determined by the required
diameter of the upper die (Fig. 6.6.2, opening stroke 100 mm). Where
mostly slender punches are used, this stroke is smaller than for female
dies used on the side of the slide, for example when producing long rod-
shaped parts or parts in closing devices. Depending on the opening
stroke, these movements require a smaller (approx. 30°for around
40 mm) or a larger (approx. 60°for around 100 mm) crank angle range.
Through the forward and reverse movement, lateral transportation
takes place. Forward motion can be initiated as soon as the grippers
engage the part, and must have been completed before the grippers
open, i. e. the upper die elements make contact with the transported
part. The forward and return motions require a crank angle of approx.
80 to 100°. The return motion takes place during the infeed and press-
ing cycles.
Transport studies of 3D transfer devices involve a lift-up motion in
addition to the movements previously described. This motion starts
briefly after the ejector movement and after the closing of the grippers.
It ends with the lowering motion which should have been completed
482
Solid forming (Forging)
Metal Forming Handbook / Schuler (c) Springer-Verlag Berlin Heidelberg 1998